The bed plays an important role in the life of any person. The choice of design should be approached with all responsibility. A comfortable sleeping place is the key to sound sleep, reliable support for the spine and a guarantee of good health. Today there are many design options, the cost of which depends on the type, shape and material of the product. If you want to save money, you can make the bed yourself.
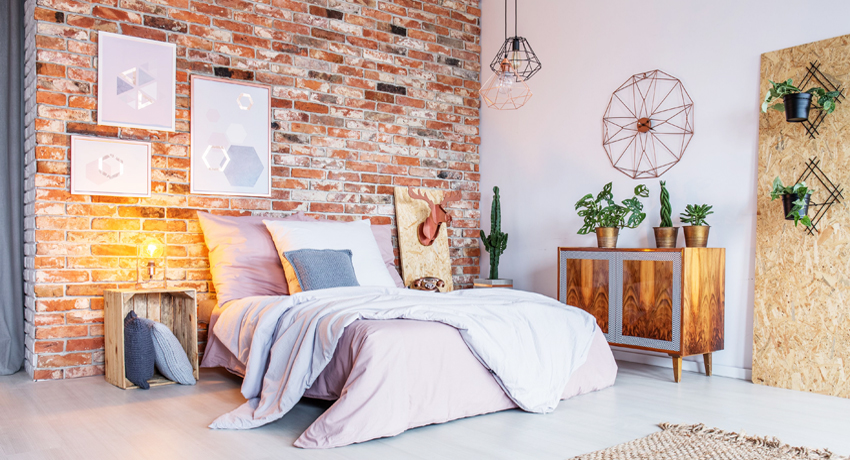
Making the bed yourself will allow you to create a unique model that matches the design of the room in which it will be located
Content [Hide]
- 1 Bed construction: components of the bed
- 2 What material can the bed frame be made from?
- 3 What are the sizes of 2-bed, single and one-and-a-half beds
- 4 Do-it-yourself single bed made of wood
- 5 Making a double bed with your own hands
- 6 How to make a round bed with your own hands
- 7 How to make a podium for a bed with your own hands
- 8 Do-it-yourself wardrobe bed made of wood: photo of drawings and progress of work
- 9 DIY technology for making a wooden bed with a lifting mechanism
- 10 How to make a sofa bed yourself: manufacturing steps
Bed construction: components of the bed
The main elements of any type of bed are the frame and base. The structure has two side panels and two support walls or two side panels and one support. The bed does not have to be equipped with side elements, it can stand on four legs, the height of which varies from 20 cm.
If the product rests on the sidewalls, there are usually storage boxes under the mattress. They can slide out to the side of the structure, or the storage space opens when the mattress is lifted from the foot side. This mechanism is called gas lift.
The do-it-yourself bed frame is represented by a box consisting of two supporting backs with drawers or four supporting side panels with hinged backs. In the case of the second option, wooden or metal legs are included in the design.
The base is attached to the frame, which is the support for the mattress. The element can be made in the form of a spring structure, a metal mesh, a rack-and-pinion movable or fixed base. The most popular is the slatted bed bottom in the form of slats, which are characterized by strength, reliability, convenience and durability. They are made from birch or beech.
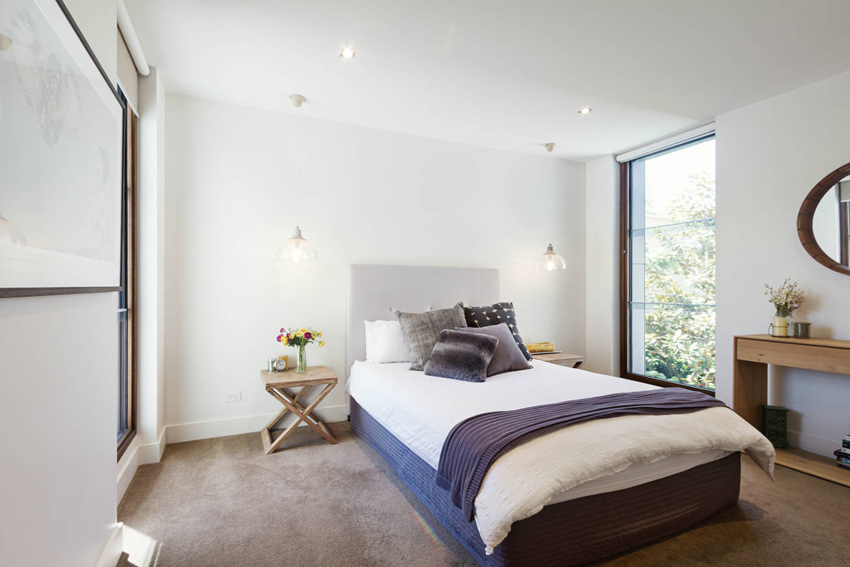
Headboard can be rectangular, round, curved and any other shape, or may be absent
Important! The more slats the base of the bed is equipped with, the stronger and more durable the structure is.
The headboard is a decorative element. It can be flat, curved, solid, openwork, wicker, lattice, vertical, inclined, upholstered with fabric or leather, decorated with carvings or paintings, as shown by photos of beds made of wood with their own hands.
The presence of a footboard is determined by the bed model. Many people prefer products without this element, which does not create a barrier for the legs, which is especially important for a tall person.
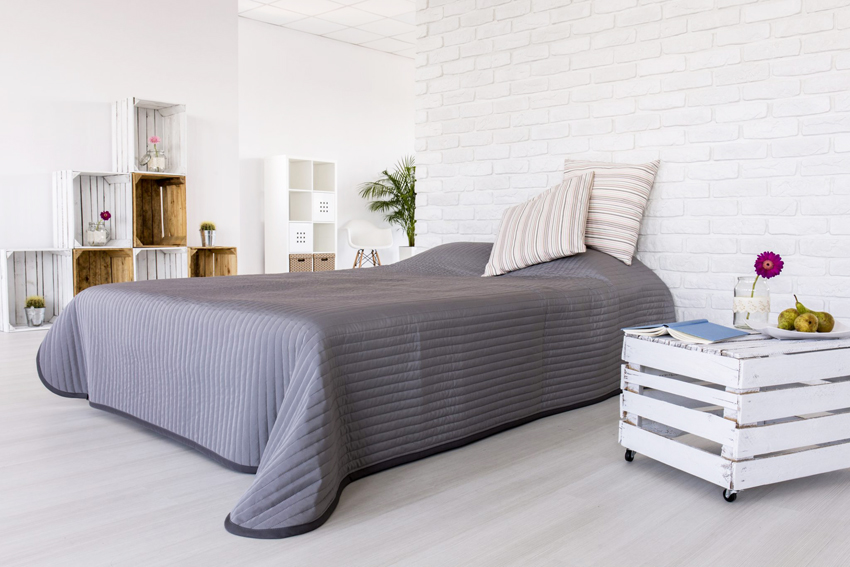
When choosing a height for a future bed, you should consider and mattress size
What material can the bed frame be made from?
The bed frame can be made of wood, metal, MDF, chipboard or rattan. The tree is still the most popular. This is due to its high technical and operational characteristics. The material is strong, environmentally friendly and durable. Wooden products have a presentable and luxurious appearance.
Elite expensive products are made of mahogany or teak wood. More affordable beds are made from solid beech, oak, ash, pine, cherry, alder or birch. The specific type of wood determines the cost of the structure. A bed made of logs looks unusual and original.
Particleboard or MDF are also often used for the production of beds. This is due to the affordable cost of the material compared to the price of solid wood. Pressed wood boards are distinguished by a rich color palette. The surface can be monochromatic or imitate wood shades.
The disadvantage of the material is some toxicity, which arises due to the presence of formaldehyde in the composition of products. There are also options for plywood beds, characterized by strength and durability.
Metal beds have firmly settled in modern interiors. The material is characterized by high strength, wear resistance and durability. Metal structures are made with gilding or silver, imitate the look of an aged product, and can be covered with leather or fabric. Such designs fit perfectly into rooms decorated in country, modern or high-tech style.
What are the sizes of 2-bed, single and one-and-a-half beds
The dimensions of the bed, which are indicated on the drawings of the beds, are selected based on the parameters of the person, the size of the room, the number of people who will sleep on it, and the specific habits of the owners. There are also two ways to measure the dimensions of a structure. In European countries, the metric system is used, that is, the size of the product is indicated in meters. In the USA, UK and Australia, the base unit of measurement is the foot.
Important! The dimensions of the bed and mattress must be calculated using the same measurement system as meters may not correspond to feet.
The length of the berth should be selected taking into account the height of the person with a margin of at least 20 cm.The standard size of the product is in the range of 180-200 cm.
The width is chosen based on the person's physique and the number of people sleeping on the bed. Depending on this criterion, products can be single, double, one and a half and children.
The single-bed design is characterized by a standard width of 100-150 cm. One-and-a-half products are chosen by those who love space. Such designs will have a width of 120-160 cm. European manufacturers produce products up to 140 cm in size, and American manufacturers - 120-137 cm.

Dimensions double beds usually range from 140 to 160 cm wide
Double bed has a width of 160 cm, which will be enough for a comfortable positioning of two people of average build on it.For thin owners of a sleeping bed, there are models characterized by a parameter of 140 cm.Fans, during sleep, are advised to use a bed with a width of up to 200 cm.
The height of the bed can vary from 20 to 90 cm, depending on the type of construction. Low products are produced with a height of 20-30 cm, standard - 40-60 cm, high - 70-90 cm.
The latter design option is often installed in small rooms, where it is important to rationally use every centimeter of space. Here you can equip a spacious storage system in the bed area.
The bed can be not only rectangular, but also round. The standard size of such a product is 220 cm in diameter.
Do-it-yourself single bed made of wood
Making a single bed with your own hands at home begins with determining its dimensions. Most often, the structure has a width of 80-100 cm and a length of 200 cm.For making the frame, boards of 25x4 cm are used.For the sidewalls, you should take elements with a length of 200 cm, for the ends - 100 cm.
How to make wood bed with your own hands? Structural components can be connected in several ways. The simplest method is to fix the boards with self-tapping screws. To create a more durable structure, metal corners should be used.
Related article:
Bed for a boy: how to choose the perfect sleeping place for a future man
How to choose the right one. Varieties for newborns. Features of cribs for boys from two years old. Original models.
The second option involves connecting elements using lugs and wooden spikes. Nests are made with a jigsaw or chisel. They should be 5 cm deep and 2-3 cm wide. The prepared joints are greased with glue and assembled.
Important! The corners of the grooves should be aligned to 90 degrees.
The next step in making a single bed with your own hands is the installation of slats. For this, support strips are attached to the longitudinal beams of the structure, which must withstand the weight of a person. They are made of 4x4 cm square wooden beams and are attached to the inner side of the sidewalls with self-tapping screws.
Further, the slats are fixed to these strips parallel to each other at the same distance using metal corners.
Useful advice! You can use a sheet of plywood or thick boards as a base for the mattress.
Next, the headboard and foot of the bed are made. For this, furniture board, chipboard, MDF are used. Products can be of various configurations and heights. The final stage is the installation of the bed legs. They are usually made from logs or blocks. Products can be a continuation of the vertical racks of the headboard and foot of the bed. Their optimal height is 25 cm. They are attached with metal corners and self-tapping screws.
Making a double bed with your own hands
Before assembling a double bed, you should measure the dimensions of the mattress. In this case, an element measuring 160x200 cm is taken as a basis.To make the structure, you will need the following materials:
- timber with a section of 50x50 mm - for making the frame and legs of the bed;
- boards 30x30 mm - for supporting beams for a rack base;
- metal corner with a shelf width of 50 mm;
- self-tapping screws 40-65 mm long.
First of all, the frame for the mattress is assembled, assuming internal dimensions of 170x210 cm and a height of 20 cm. On each side, four bars are glued together, which are pulled together with clamps. You should get two blanks 180 cm long and two 220 cm long. They are connected to each other in a lock.To do this, a 5 cm long recess is cut out in the middle with a jigsaw on short elements. Spikes are made on long blanks. For this, 5 cm of timber is sawn off from both sides.
The formed grooves and spikes are coated with glue and connected at right angles. In the middle part of the frame, a longitudinal jumper with additional support is fixed using a metal corner. At the corners of the frame, legs from a bar with a height of 40 cm are attached; glue and self-tapping screws are used for this purpose.
For structural reliability, the legs can be made from a thicker bar. To give them a graceful shape, it is necessary to chamfer with a miter box on the inside at an angle of 45 degrees. Long cap screws with countersunk washers should be used to mount the legs.
Useful advice! To prevent deformation of the structure, triangular inserts are recommended at the bottom of each corner.
Along the long frame elements on the inner side, beams are attached under the rack base. Their upper edge (this is clearly seen in the drawing of a double bed) is located in the same plane with the upper border of the lintel. Slats 170 cm long are made from 20x100 mm boards. They must be laid and fixed across the lintels and longitudinal support beams with a step of 3 cm. The first and last elements must be tightly adjacent to the front and rear walls of the bed frame.
Useful advice! To exclude the creaking of the slats, the elements should be made 1 cm shorter than the frame of the frame.
How to make a double bed with your own hands: making a headboard
After assembly, the frame should be sanded with medium-grained sandpaper. The surface is applied stainAfter drying, the frame is varnished in several layers.
Wall mounted headboard for bunk bed is made of 3 boards with dimensions 25x100x1800 mm and 12 bars with dimensions 25x100x450 mm. For the first row, which will be in contact with the back, short products are used. Hidden fasteners are installed on the seamy side. At the appropriate places of the headboard, metal plates are screwed with self-tapping screws. When hung, their free edge will be inserted into the grooves of the tires.
You can make a soft headboard for a bed from a bar with your own hands, consisting of the following layers:
- plywood or chipboard (1 cm);
- foam rubber (3 cm);
- batting;
- upholstery fabric with a pattern.
A base measuring 45x180 cm is cut out of plywood. The edges should be chamfered, and then the edges should be carefully processed so as not to damage the batting and upholstery.
A blank of the same shape and dimensions is cut out of foam or expanded polystyrene. It is applied to a wooden product, several holes are made for decorative buttons. Cutting of batting and upholstery fabric is carried out according to the parameters of the workpiece with an allowance, the size of which should be equal to the sum of the thickness of all layers, multiplied by two.
Foam rubber is glued to a wooden base. Batting is stretched onto the workpiece, the popped edges of which are fixed with a furniture stapler. The number of staples can be unlimited as they will still be invisible. The operation is repeated with the upholstery.
Useful advice! To prevent the fabric from wrinkling, it must be well ironed with an iron and tightened with a clamp, which is screwed to the middle of the workpiece.
The final step is to sew on the sofa buttons by using a large boot needle and coarse thick thread. The upholstered headboard is wall-hung with wall cabinet rails.
How to make a round bed with your own hands
You can make a round bed with your own hands.It will be an unusual element of the room, capable of not only decorating it, but also solving problematic issues of space with curved walls. This design in modern interiors is installed in the center of a spacious room, giving it a royal luxury.
To create the base of a round homemade bed, a 35 mm sheet of plywood is used. It fits mattress so that none of it overlaps the sheet. With a jigsaw, a round workpiece is cut out along the outline, the front part of which is sanded. From 40x40 mm boards, it makes a cruciform frame with a diameter equal to the size of the plywood blank. Connect the products with self-tapping screws.
Useful advice! To create wooden products, special wood screws are used with a large thread.
On the edges of the cross, wooden bars are attached, the length of which corresponds to the height of the structure. They are connected with the second floor of cruciform beams. Stiffening ribs are fixed between the legs.
The end of the bed made of boards and plywood can be decorated with hardboard, which is attached around the perimeter with a stapler. Foam rubber is laid on top, which is covered with eco-leather. The surface is decorated with staggered sofa buttons.
How to make a podium for a bed with your own hands
Before you make a bed with a podium yourself, you need to decide on the location of the product. The space should allow pulling out drawers or a sleeping place. A drawing of the finished structure is created, after which the corresponding markings are made on the walls and floor of the room.
Useful advice! If the podium is located close to the wall, the skirting board must be removed at this point.
How to make a podium bed? To create a frame, you will need a bar with a section of 50x50 mm. For rough finishing, chipboard or plywood with a thickness of at least 12 mm is used. For the finishing cladding of the structure, chipboard is used. Drawers are made of plywood.
After all the elements are made according to the created drawing of the bed with their own hands, the structure is assembled. Vertical posts are attached to the floor along the perimeter of the future podium, which are fixed on 4 sides using galvanized corners and dowel-nails. The height of the elements should be less than the height of the podium by the thickness of the timber used to make the frame.
If a double bed is created, a partition of a bar or board is made in the middle, which rests on an additional row of racks. On top of the racks to create the top of the frame frame, it is necessary to lay the beams, fix them with corners and wood screws. It is required that the racks are located strictly perpendicular to the floor, and their upper part should be in a horizontal plane.
Diy podium bed: the final stage
The next step in making a podium bed with your own hands is making markings for drawers. The planks that form their frames must be attached to the bottom of the racks. Partitions are attached to them. A base for the mattress is created, which is a lattice surface.
Then the podium is trimmed. If the bed is installed on it, then it gets off with chipboard. To create a headboard, you can use furniture board, MDF or chipboard. This element is made in the form of a tall product that turns into a back.
If the bed is pulled out of the podium, chipboard is not suitable as a material for manufacturing, since the structure will be subjected to significant stress. In this case, a rough sheathing is created from OSB or thick plywood, which is sheathed on top with laminate, carpet or other material. Plywood is attached to the frame with self-tapping screws.
The pull-out bed is made in the form of a large rectangular box, inside which the mattress will be located. The simplest solution is to purchase a finished rack bottom. On the sides of the frame, plywood boards are stuffed. Wheels are attached to the bottom of the frame.
Do-it-yourself wardrobe bed made of wood: photo of drawings and progress of work
Do-it-yourself wardrobe bed at home has an unusual look. The bed is removed in a special storage, which is not visible from the side. This model fully allows you to save free space, since the assembled structure is part of the cabinet and does not take up space.
To make a transformer bed with your own hands, you can take an old structure. The frame is freed from the slats. A cabinet frame is created under it. To do this, use 40x50 mm bars, with which a rectangular structure is assembled. Using the corners, the base of the frame is fixed to the wall.
Next, the lifting mechanism and gas springs are attached to the sides of the cabinet. The first element connects to the bed frame. To fix the elements, it is very important to use strong bolts that allow you to carefully screw the parts together, since this place will take maximum loads.
Slats are installed on the frame of a floating bed, made by hand. The base of the structure is made from a chipboard sheet, which must be decorated with wallpaper or special paper, creating an imitation of a cabinet. In the upper part, on the outside of the base, you need to attach handles, pulling on which, you can unfold the bed. It is advisable to supplement the design with side lockers for storing clothes, open shelves or lamps.
DIY technology for making a wooden bed with a lifting mechanism
To create a bed with a lifting mechanism with your own hands, you should prepare a detailed drawing of the furniture assembly, and you can also find a similar diagram on specialized sites on the Internet. This will avoid many design errors that will subsequently negatively affect the functionality of the structure.
You can choose a gas or mechanical device as a lifting mechanism. The first option is based on the use of gas shock absorbers. The mechanism is either equipped with a lock or has no lock. The main advantages are soft debugging, quiet operation and ease of use.
The mechanical element operates with metal springs. It is characterized by the ability to adjust the operation of the lifting system by removing, adding, tightening or loosening the springs.
Using a drawing of a bed made of wood with your own hands, drawers, sidewalls, a headboard and the bottom of the boxes are made from chipboard or MDF. The base frame is made of wooden blocks. The bottom for the boxes is attached to it. Drawers and side elements are installed on the frame, on top of which the slatted flooring is placed under the mattress. A headboard made of chipboard is fixed on the base.
The lifting mechanism is installed according to the instructions. The lower steel bar is attached to the squared base frame, the upper one is attached to the side part. After the structure of the bed is assembled, sheathing is performed. For this, sheet foam rubber is laid on the base in several layers. From above, it is covered with an upholstery material made of fabric, dermantine or leather. The sheathing is attached to the frame with a furniture stapler. The sides of the bed are processed in the same way.
Important! In the places where the finishing touches the lifting mechanism, small gaskets are placed under the base material.
The final stage is the installation of finishing accessories in the form of rollers, castors or support legs.
How to make a sofa bed yourself: manufacturing steps
Even a novice craftsman can make a wooden sofa bed with his own hands. Photos of drawings on the Internet with the indicated dimensions of the products will help in this process. At the first stage, the frame of the box for linen is created from boards with a section of 25x200 mm.
In this case, the crossbeams must be located at a distance of 50 mm from the edges of the longitudinal elements. Bars with a section of 50x50x200 mm are inserted into these edges to strengthen the structure. For rigidity of the product, transverse slats are attached to the longitudinal beams at a distance of 600 mm from the edges. Further, the bottom of the box is sewn up with a sheet of fiberboard.
Then two frames are made - for the seat and the back. Products are made on the basis of a do-it-yourself sofa-bed drawing from beams with a section of 60x40 mm. All elements are connected to each other with nails.
Slats are attached to the finished frames by means of self-tapping screws, which provide support for the soft parts of the back and seat.
The next (most difficult) stage is the manufacture of armrests. 4 identical walls with a width of 900 mm, a height of 700 mm in a high place, and 500 mm in a low one are cut from a fiberboard sheet. The length of the highest seat of the armrest is 100 mm, the lowest is 460 mm. Wooden frames are installed along the contour of the two blanks. Further, the structure is reinforced with transverse elements. The armrest is sewn up with a second sheet of fiberboard.
Before assembling the sofa bed, the armrest is finished with foam rubber, which has a thickness of 40 mm. A roll with a width of 150 mm is made from it at the beginning of the product, reaching 50 mm in the middle and end of the product. A sheet of foam rubber is applied to the resulting side, which is covered with another roller in such a way as to provide it with a round shape.
The entire structure of the armrest is pasted over with another layer of foam rubber. Then the side is covered with fabric and equipped with sofa fittings. Next, all the elements of the sofa bed are assembled into a single structure using a transformation mechanism.
Important! The transformation mechanism is installed in such a way that a gap of 10 mm remains between the seat and backrest in the unfolded structure. It should be noted that the seat of a folded sofa should not protrude beyond the armrests.
After the bed is assembled, it is upholstered. Non-woven material is nailed onto the lamellas, on top of which foam rubber with a thickness of 60 mm is laid. Another strip of material is glued to the edge of the seat. Further, the entire surface is covered with a second layer of foam rubber, bending its edges under the seat. The same procedure is performed with the back of the sofa. Removable covers are sewn onto structural elements.
With minimal skills, you can make any type of bed yourself. The main thing is to correctly draw up a drawing of the future structure, prepare the necessary material and, following the instructions, complete its assembly.