The real estate market is annually replenished with new proposals for development using innovative materials and technologies. The construction of houses from foam blocks is gaining momentum, although not all masonry specialists have tried working with foamed concrete. Environmentally friendly material has its own characteristics, which are important to consider in work. Although foam block is sometimes confused with other materials, the number of houses made of it is growing around the world.
Content [Hide]
- 1 Building a house from foam concrete: how porous materials are obtained
- 2 Dimensions of the foam block for building a house and its important properties
- 3 What is the difference between the construction of houses from foam blocks: characteristics of cellular material
- 4 Construction of houses from foam blocks: the undeniable advantages of the material
- 5 Features of building houses from turnkey foam blocks
- 6 What should be the foundation for a one-story house made of foam blocks
- 7 What materials are used for the construction of houses from turnkey foam blocks
- 8 Features of the technology of laying block walls
Building a house from foam concrete: how porous materials are obtained
High-speed construction is becoming more and more popular: it is possible to quickly find your own home and celebrate a housewarming. Not all materials are suitable for this purpose. The cellular structure, somewhat reminiscent of foam rubber or pumice, is inherent in new varieties of porous concrete.
Foam block construction is gaining popularity due to the special properties of the material, although it is often confused with aerated block (it is softer) and related structures. Block masonry successfully competes in the construction market, since often houses made of foam blocks are cheaper and warmer than buildings made of traditional shell rock, concrete slabs, natural or artificial stone and brick.
Most modern types of cellular blocks are made on the basis of foamed concrete. This material, recommended for the private construction of aerated concrete houses, can be classified as artificial cement foam from natural raw materials in the form of convenient blocks. In fact, foam concrete is a cement mortar that has undergone foaming and polymerization due to additives that determine its type.
Currently known porous materials:
- gas slag concrete and foam slag concrete;
- aerated concrete and foam concrete;
- foam silicate and gas silicate;
- foam concrete and aerated concrete;
- foam silicate and gas silicate.
Porous block varieties differ in various characteristics, including cell size, base density and color, which determines the cement base. These are Portland cement, Portland slag cement, slag and lime mixture and other inclusions.
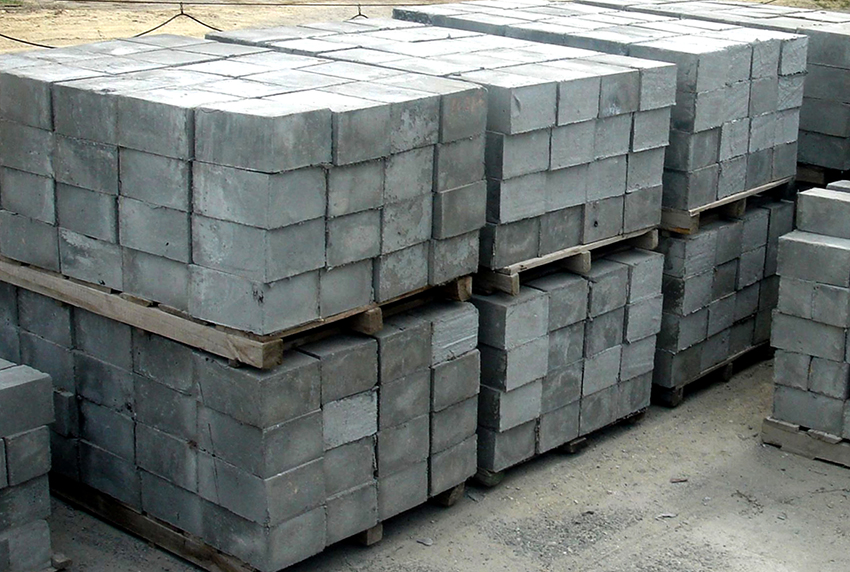
Porization of foam concrete is obtained due to gas that is released as a result of a chemical reaction
The main distinguishing feature is the porization method, most often due to the gas that is released as a result of a chemical reaction during the interaction of the mixed components. In the case of foam block masonry, a special foaming agent is used, which is obvious from the name. The process of hardening building materials is also carried out in different ways - by natural drying, under pressure or under the influence of high temperatures. Some materials then have high thermal insulation characteristics.
Dimensions of the foam block for building a house and its important properties
Construction companies have already appreciated the environmentally friendly light gray material. It is convenient for laying, not very heavy and, as they say, "does not sink in water, does not burn in fire." It is produced with the addition of sand and a special foam component that does not have a negative effect on health. The foam structure is produced in a packaging that is convenient for transportation and stacking:
- partition blocks for internal walls - 100x300x600 mm;
- the main material for masonry walls - 200x300x600 mm.
This is a standard option, but at the request of the customer, a large batch of blocks of a different format can be produced. For example, dimensions of 300x400x600 mm, 200x300x500 mm and 200x400x600 mm are practiced. It is also possible to cast corner modules. If there is a need to create blocks of other dimensions, you should be aware that only the length or width parameters can be reduced or increased - this is displayed in the photo of foam blocks.
The way of laying is much easier than working with bricks, where you need sufficient qualifications and experience. The surface of the blocks is easy to process, they are easy to cut and connect with building glue, making original designs. Instead of cement mortar, you can use a special adhesive base, removing excess, so that you do not have to level the surface later. From above, the material is covered with layers of plaster or other finishing.
Useful advice! When building a house from blocks, if there is excess length, the excess can be cut off and a segment inserted in the middle of the row with a gap of no more than 3 mm.
The composition of foam concrete does not contain harmful chemical components, so it is recommended for people who care about their health or have problems with respiratory diseases. This material can even be used for the construction of children's and medical institutions.
Convenient sizes and the correct shape of the blocks make it possible to quickly erect walls, reducing the cost of the process of laying a foam block with your own hands and with the involvement of specialists. The low cost of the material and the high speed of wall removal make such construction economically profitable.
What is the difference between the construction of houses from foam blocks: characteristics of cellular material
Currently, there is no building material that would be universal in all respects, meet all the requirements and is devoid of flaws. The outer part of the foam block wall needs insulation and cladding, but the material itself demonstrates high thermal insulation performance. For interior work, a lot of starting plaster and finishing are not required, as it is a fairly smooth homogeneous material.
For interior and exterior decoration, you can use common materials:
- decorative plaster;
- facade and interior paint;
- polymer siding;
- wallpapers of all varieties;
- facing stone and brick;
- lining;
- plastic sheathing;
- tiles, porcelain stoneware and other tiles.
Note! Porous materials have difficulty supporting heavy structures. Therefore, it is better to abandon the heavy lathing and reinforcement, which should be mounted on dowels, brackets and other holders in the wall. It is important to think over the choice of finishes before starting to build a house from foam blocks.
Among other characteristics, builders who worked with this material note its following properties:
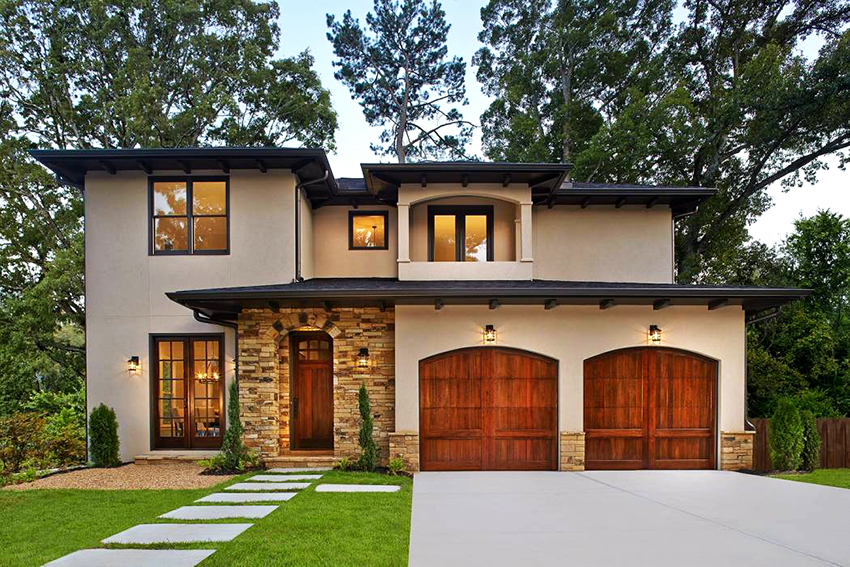
Foam concrete is characterized by high sound insulation, frost resistance and environmental friendliness
- frost resistance;
- high sound insulation;
- environmental friendliness of raw materials and a block ready for laying;
- sufficient thermal insulation;
- comfortable microclimate in the house - a consequence of thermal inertness and absorption of steam from the room;
- heat resistance - longer than ordinary concrete and reinforced concrete products, it keeps the temperature during fire, preserving the metal reinforcement and frame;
- vapor barrier - the wall "breathes", absorbing and giving off excess moisture;
- the possibility of embodying any architectural idea within 2-3 floors.
Important recommendations! Although the material gives off moisture and does not sink, it is better not to expose the foam block for building a house to extreme checks. It was possible to drain the buildings from it even after the flood, but excessive porosity does not imply the use of the material in swampy areas, flood meadows and lowlands, where there is often abundant and rapid snow melting.
Construction of houses from foam blocks: the undeniable advantages of the material
Foamed concrete is an economically profitable material intended for buildings in the budget segment and commercial construction, characterized by a lot of positive characteristics:
- one of the most budgetary proposals of the modern construction market;
- it is characterized by ease of use: thanks to the simplicity of the masonry, which even inexperienced builders can handle, DIY installation is available (significant savings);
- large-format blocks contribute to a fast pace of construction, which gives
the ability to start and complete the construction in one season - provided that the foundation for the house is made of foam blocks; - homogeneous pores without large voids - a guarantee of maintaining the properties and density of any fragment after cutting with vertical and horizontal laying;
- smooth surface facilitates plastering and finishing, while saving materials;
- in all respects, a profitable and economical material - a two-story cottage made of foam blocks is cheaper than a small dacha made of brick or wood;
- thanks to easy cutting and processing of blocks, upon completion of construction, you can easily change the shape of openings for windows and interior doors, create arches to unite adjacent rooms and complete original partitions for zoning, make strobes for communications;
- relatively soft material facilitates cutting and drilling of blocks with simple tools and fixtures;
- no expensive solid foundation is required, since ready-made foam block houses are much lighter than other buildings of the same format;
- foamed concrete buildings belong to an inexpensive segment of the market, which significantly expands the client base of companies engaged in the construction of private buildings, and the customer receives competitive turnkey projects for the construction of houses from foam blocks;
- pieces of blocks lend themselves to gluing, while maintaining their properties, which minimizes waste and a relatively clean area, which allows you to additionally save on cleaning the territory;
- a thin-layer mortar or glue base is enough to securely bond the segments, they dry quickly;
- despite the porosity, the structures are tight and reliable;
- with sufficient waterproofing of the walls, you can build a house from foam blocks with your own hands, and it will last at least 70-80 years;
- material available throughout the country - a batch can be purchased in warehouses or through a distribution network, as well as ordered from catalogs.
Important! The experience of construction firms shows that clients who have a two-story house made of foam blocks often order country houses from similar materials or invest in real estate of a similar type.
Of course, nothing is perfect, and aerated concrete has its drawbacks, which are worth talking about frankly.
Build a house from foam blocks: detectable and probable disadvantages
This material is quite specific, so you should not take on a construction site without thoroughly studying all its pros and cons. It is important to know that the foam block has such drawbacks:
- relative fragility of the material - due to sharp impacts on the blocks (or as a result of other mechanical damage) corners can break off, cracks and splits occur, which is why it is recommended to transport it in Euro pallets;
- caution is also necessary when loading and unloading a batch, laying (it is better not to throw, not to drop blocks), accuracy is also needed when cutting;
- a residential building made of foam blocks with your own hands is the best option, but it is not recommended to use this material for the construction of a pool, bathhouse, sauna, that is, rooms with excessive moisture, the likelihood of leaks and flooding;
- the known ability of porous materials to absorb excess moisture, like a sponge, is also observed in aerated concrete - it is important to ensure that the walls of the premises are not waterlogged, otherwise thermal and frost resistance will be lost;
- the structure of foam concrete does not tolerate excess load, therefore it is recommended to build a low cottage, a summer cottage on 2-3 levels or a country house from foam blocks with an attic, but it can be used on the upper floors when increasing the number of storeys (without a pool or sauna);
- when building a site, blocks should not be laid on the ground due to increased moisture capacity;
do not use the material when laying the foundation, the walls must have hermetic insulation (from the ground, foundation, protection of the outer surface of the walls); - in the heat, the walls are difficult to plaster without a primer or preliminary moistening;
- foam concrete is not the hardest and most durable material, so over time you can find cracks in vertical seams, chips under lintels, at corners and joints with other materials.
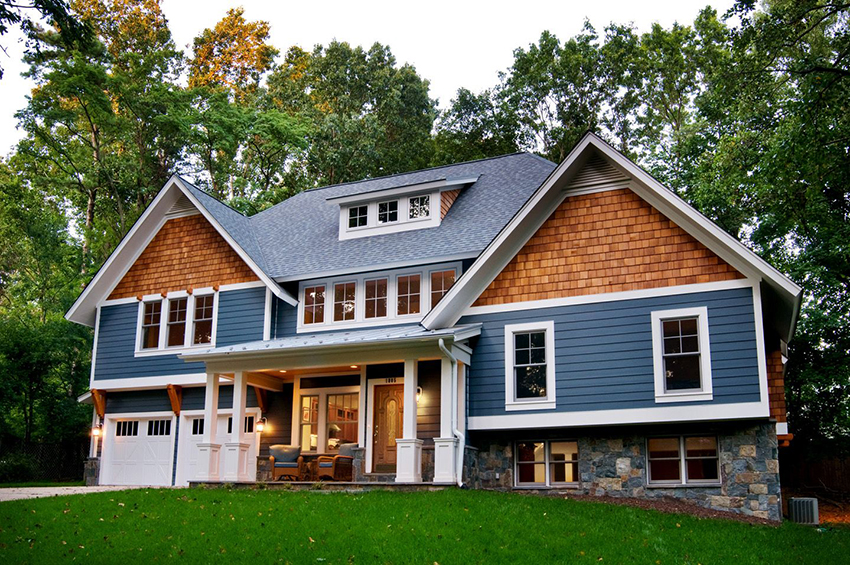
It is impossible to build houses higher than 2-3 floors from foam concrete, because the material cannot withstand excessive loads
Useful advice! It is recommended to direct significant savings from the cost of purchasing the material itself and building a house from blocks with your own hands on prevention and elimination of shortcomings. It is necessary to pay special attention to increased waterproofing and protection of the wall surface from possible damage.
Features of building houses from turnkey foam blocks
Private home ownership is becoming more and more popular in the Russian Federation. Therefore, many are interested in options and prices, projects and construction rates. The question of how to build a house from foam blocks with your own hands also remains relevant.
Related article:
House project from foam blocks with a description: from planning to finishing
Turnkey houses: from getting to know the peculiarities of building materials to putting the facility into operation. Properties, advantages and characteristics of the material.
If this is a small 6 by 6 house made of foam blocks, which must be built with your own hands, it can be made in 2 seasons (subject to some building experience). To begin with, the foundation is poured, after its shrinkage, a box is made and the rafters for the roof are installed. For the next season, you can start the final phase: bring in communications, make a rough finish, insert windows and doors, install plumbing.
Customers who have applied to construction companies can be offered different readiness options for 50% prepayment with subsequent payments:

By choosing to build a turnkey house, the customer will eventually receive a full-fledged house with a landscaped area
- plots with a ready-made foundation for the construction of houses from foam blocks with their own hands;
- fully completed box with a roof;
- a house without finishing with supplied communications;
- turnkey construction, when the client receives housing 100% readiness with a landscaped area.
The total amount of work determines the cost of the object. Usually payment is made in installments - on condition of half of the prepayment. The most expensive has always been a complete construction cycle. The customer does not interfere with anything, trusting the specialists, only chooses a project and after a while accepts a new turnkey house.
Turnkey foam block house with phased construction: from project to move-in
Today it is profitable to build a house from turnkey foam blocks - from choosing a site to housewarming. Landscaped territory, built road from the highway (if agreed), all communications and even interior design - many construction companies offer such services. At the same time, the customer has the right to visit the facility without warning in order to assess the quality and pace of work in accordance with the terms of the contract.
High qualifications are required at each stage. Although building a cottage from foam blocks costs about half the cost of building similar objects from other materials, the price should not affect the quality. Savings come from other factors:
- the cost of aerated concrete blocks;
- a small (compared to brickwork) layer of mortar or glue;
- high speed of laying walls due to large-format material;
- the cost of work in the budget segment is much lower (no high qualifications are needed);
- plastering of walls does not require preliminary leveling (subject to technological installation);
- the thermal stability of the foam block is also the savings on expensive insulation.
Useful advice! The funds saved during the construction of budget houses can be used to attract high-class builders by signing a turnkey contract.
Before clarifying how much it costs to build a house from foam blocks, it is important to decide which part of the work will be done independently, and which is better to entrust to specialists. Individual design is expensive, but it takes into account all aspects, including relief features, soil structure, which determine the choice of foundation, and the calculation of the cost of the entire volume of construction work.
It is very difficult to remodel a house, and sometimes even impossible. Therefore, from the very beginning, it is important to decide not only from what to build, but also how, while it is necessary to take into account the following factors:
- number of storeys (this material does not withstand the load of high-rise buildings);
- area around the perimeter (for example, a large one-story house 10 by 10 from a foam block or a smaller format, a house from a foam block 8 by 8, but with 2 floors);
- layout, including the number of living rooms and auxiliary premises;
- exterior cladding and interior wall decoration;
- kind of foundation;
- type of boiler and heating circuit;
- communication line diagram;
- site decoration (with landscaping, lighting and garden).
Before building a house from a foam block, they prepare a plan for building a site with a facade and floor sketches of the house. You can use a typical project, but in this case, there are usually some inconsistencies, as a result of which it has to be corrected. When designing yourself, you can use several ready-made options, but first you need to figure out what exactly should be reflected in the development.On the Internet, you can find good examples of photos of block houses.
What should be the foundation for a one-story house made of foam blocks
There are several options for the foundation. Foamed concrete structures are much lighter than other buildings, which makes it possible to count on a lighter base. Usually, concrete slabs are laid or concrete is poured into the trench using formwork. This will provide an even load from the foam block house under construction, the photos are a good example of this.
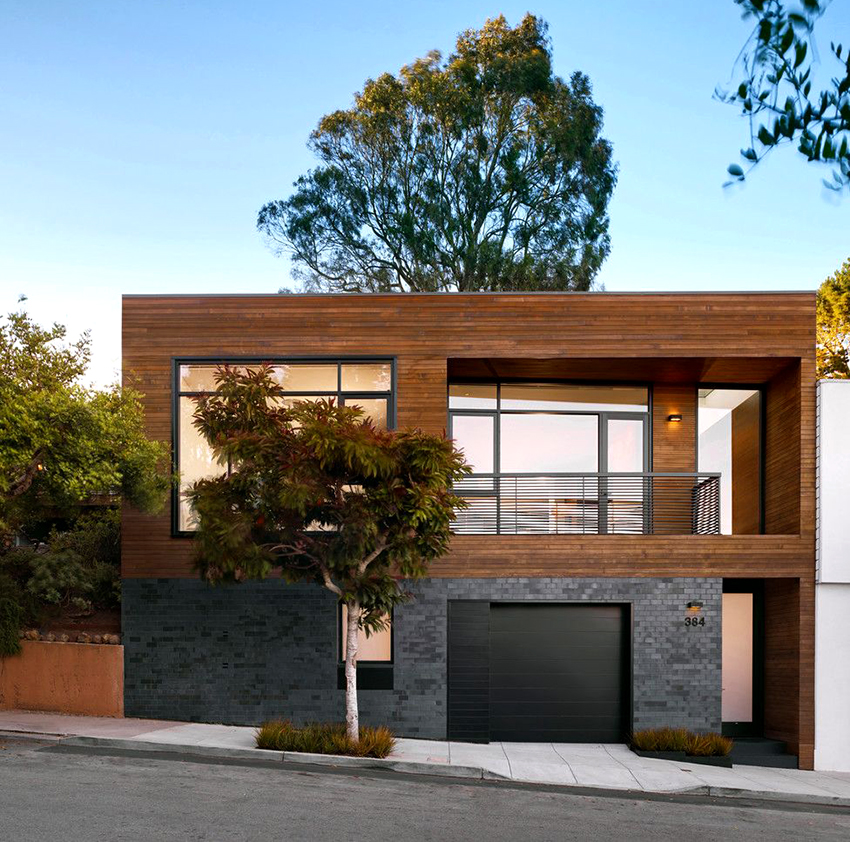
If the project has a small house made of foam blocks, then you can use a conventional strip foundation
If the project involves a basement, then you need a full-fledged pit along the entire perimeter. The basement or semi-basement floor is an additional usable area, in this case the foundation is built differently - to the full height and more solid. But on the lower level, you can organize a wine cellar and a small workshop, a boiler room for autonomous heating and a cellar for blanks.
If this level is not in the project, then you can limit yourself to a light strip foundation for external and load-bearing walls. On the prepared site, markings are made and a trench is dug. The type of foundation largely determines the strength of the entire building.
Useful advice! If you do everything correctly, then you will need soil samples to calculate the expected load and determine the type of foundation. This is usually done by an architect who prepares a project before building a house from blocks to order with reference to a specific location.
The main types of soils found in our country:
- rocky;
- semi-rocky (stony);
- clayey;
- loamy;
- peat;
- sandy;
- sandy loam;
- saline.
On unstable soils, a reliable monolithic foundation is needed, which will ensure the integrity of the building for many decades. This is especially important for aerated concrete structures: they are less sturdy than brick houses. In this case, even with significant subsidence, the likelihood of wall cracking is minimized.
How is the foundation for a house made of foam blocks
At the prepared site of the site allocated for construction, the perimeter of the future house is marked. Usually the stakes are hammered and the ropes are pulled. This is a place for digging a trench for a foundation, the depth of which can vary from 50 to 120 cm. The foundation is constructed in different ways - from rubble stone, on screw or concrete piles, or it will simply be a strip monolith made of concrete. The assumed load, wall thickness and masonry material determine the width of the foundation. Usually it varies within half a meter, but should be slightly wider than the walls.
Note! The bottom of the trench of a house made of a foam block 10 by 10 m is compacted after digging, the pillow is covered with a layer of crushed stone and sand and thoroughly compacted. Its level should be below the soil freezing line. On moving soils (swamps, sands), piles are recommended.
The walls of the trench are equipped with formwork, which is lined with roofing material or dense polyethylene. Next, a reinforced belt is prepared from scraps of reinforcement and thick metal rods tied with a metal wire.
A trench with reinforcement is poured with concrete, for which cement and sand are mixed in a ratio of 3: 1. M400 grade cement is recommended. The finished foundation is allowed to settle for at least a month. After that, a layer of reliable waterproofing is made (roofing material and waterproofing mastic) so that moisture from the soil and foundation is not transferred to the walls.
Important! The load on the foundation in buildings with a complex configuration is calculated using special formulas using computer programs. It is better to entrust this process to specialists. The base is recommended to be made with a margin.
A more solid foundation is also needed when annexes or complex heavy structures are planned, such as a bath or a sauna, a greenhouse, an indoor pool, stairs and a mansard-type roof.
What materials are used for the construction of houses from turnkey foam blocks
Currently, the construction of private houses is carried out on the basis of the latest technologies and using modern materials. There are different options, but construction companies offer a solution that is optimal in terms of price and quality.
Important! In custom-built houses, all technical standards are observed, the wood is impregnated with antifungal fungicides, antiseptics such as the Finnish TIKKURILA, steam, sound and waterproofing must be performed, heaters are laid. The same materials should be used for individual building according to a standard project.
The cost of a foam block house usually includes a traditional foundation tied to soils by type of terrain and other components (optional):
- single-layer walls up to 380 mm thick, which are clad from the outside with siding, brickwork or decorative plaster (combined design is possible);
- interfloor floors, beams impregnated with a fire retardant or fungicide, coated with colorless varnish;
- wooden (or metal) stairs made of pine or ash;
- the floor is covered with natural wood (pine) on top of a screed, expanded clay pillow and a substrate or laminate (decor - at the request of the customer);
- on the ceiling filing - drywall with plaster, lining or other material, if it is assumed by the interior design, for example, a stretch ceiling or combined multi-level structures;
- roof rafter system with insulation along the beams, roof lathing - according to all the rules, including vapor barrier and outer coating with ondulin or metal tiles (other options are possible);
- entrance doors - metal with dusting, interior doors - eco-veneer, veneer or solid wood (inserts for stained-glass windows);
- windows - metal-plastic double-glazed windows, double-glazed windows can be used, if additional sound insulation is needed, lamination under wood or a completely wooden alternative, the number of transoms is negotiated with the customer;
- heating - a closed circuit with a boiler, aluminum or bimetal batteries, a fireplace in the living room or hall and "warm floor" is possible;
- communications - traditional, electrical wiring - copper, hidden, with grounding, sockets and switches, metal-plastic pipes;
- imported plumbing, ready-made sewerage wiring with a septic tank (a cesspool is equipped).
The cost of services includes other costs, including transport and remote accommodation for the team.
How to calculate the material for a house from blocks
After there is a ready-made development plan, they begin to calculate the number of foam blocks. When assigning work to construction companies, you should not think about it: they will calculate everything themselves. When the pasture of the box and the main part of the construction is planned to be done by hand, it is important to know how many foam blocks are needed per house. It is not worth buying an excess amount, especially since the material is easily sawn, the remnants are easily glued together and stacked in a row.
Note! The material is sold in cubic meters.

To correctly calculate the material, you need to know the exact dimensions of the foam blocks that are planned to be purchased
For the correct calculation, you need to know the parameters of the blocks, which can vary, and the area of the walls. If the house is 10x10 m, then the length along the perimeter is 40 m. The height of a one-story building (usually no more than 3.5-4 m) is multiplied by the perimeter. The resulting indicator is multiplied by the block thickness (for example, 0.3 m) - this is the required number of cubic meters.
How to calculate foam blocks for a house for partitions (interior or interior walls)? According to the above scheme, we summarize the quantity. For a one-story house, approximately 50 cubes will be required. When block materials are accurately calculated and purchased, costs for glue and concrete mortar are added.
Useful advice! When purchasing materials, the indicators are rounded up so that there is some margin. If cladding bricks or materials for decorative cladding of the basement are required, they are considered separately.
Features of the technology of laying block walls
Although houses made of porous concrete are built much faster than similar buildings from traditional materials, all stages and technologies are followed so that there are no complaints about shortcomings.
Any houses are erected the same way, only at different times - from choosing a building site to interior design and general improvement of the territory. However, blocks are a relatively large building material, and a slight vertical deviation gives a chance to start building a "skyscraper". Laying begins from the corners towards, pulling a cord between them to orientate horizontally and vertically. If the first row is laid correctly, the entire forcing of the walls should go without problems.
Useful advice! For this job, you will need a paddle for applying an adhesive base and a rubber hammer for fitting. Construction dust is removed with brushes, excess mortar is immediately removed.
The blocks in each row are shifted relative to the previous row so that the vertical seams do not coincide. The ends are joined by groove-spikes (if available in the batch) and fitted with a rubber hammer. After 2-3 rows, reinforcement is performed in specially designed grooves, the reinforcement is poured with concrete. Lintels are made over windows and doors by means of special blocks or beams filled with concrete. In the last row, a brick dressing is needed for installing the roof. The rest of the stages, including finishing, are carried out using classic technologies. On the Internet you can find examples of videos of building houses from foam blocks.
Obviously, aerated concrete blocks are not only innovative, but also beneficial in all respects building material. It is readily used by construction companies and non-professionals with minimal experience in wall construction. A feasible task is to build a block house with your own hands, since there is nothing complicated in this technology. Provided that the foundation is ready, it is quite possible to build your own house in one season.