To protect wood, concrete and polymer coatings from mechanical damage, exposure to moisture and other negative factors, the surface is opened with varnish. Today there is a wide variety of formulations that differ in technical and operational qualities. The most popular is polyurethane floor varnish, which is characterized by safety, high drying speed, strength and durability.
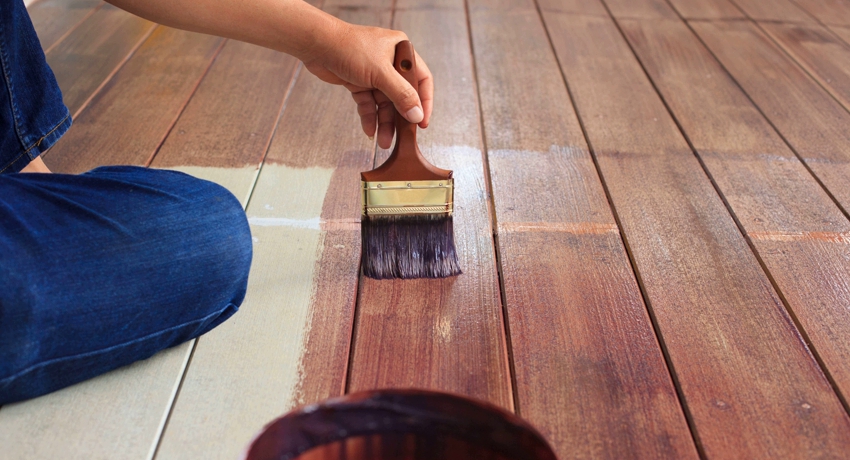
There are many varieties of polyurethane floor varnishes with different effects and characteristics.
Content [Hide]
The use of varnish and varieties of chemical compositions
The floor surface is constantly exposed to mechanical and shock loads, which lead to the formation of scratches, cracks and chips. As a result of exposure to moisture, the integrity of the surface structure is violated. Ultraviolet rays have a detrimental effect on the appearance of the floor, distorting its original shade and texture.
As a finishing element for finishing the floor, a paint and varnish coating is often used, which creates reliable protection of the base from various kinds of negative influences that arise as a result of its long-term use.
Note! Thanks to the transparent texture of the composition, you can favorably emphasize the natural structure of natural wood and not spoil the pattern of the self-leveling concrete floor.
Varnishes are classified according to the type of binder in their composition. Depending on this, the following types of material are distinguished:
- acrylic floor varnish has good elasticity, provides acceptable strength to the base, resistant to abrasion. The main advantage is the low material cost;
- the oil composition is used as a preliminary layer before the final application of varnish, which helps to create a denser and more durable surface;
- alkyd floor varnish provides a surface that is resistant to mechanical damage, but it is less resistant to shock loads;
- polyurethane compound gives the base increased strength, abrasion resistance and durability;
- acrylic-polyurethane material is characterized by good strength and resistance to mechanical stress, but inferior to the previous version. The main advantage is the low price of the varnish;
- urethane floor varnish has good elasticity, abrasion resistance and low cost. The composition is used in rooms with low traffic;
- urethane-alkyd composition is characterized by increased resistance to abrasion and impact loads;
- alcohol varnish has good adhesion and durability. However, due to its low moisture resistance, it is not recommended for wood flooring.
Polyurethane floor varnish: material characteristics
Polyurethane varnishes are widely used to protect concrete, self-leveling, wooden floors, polymer coatings, stone processing, parquet, wooden furniture and other elements. Such compositions provide reliable protection of the surface from mechanical and chemical influences.
Water-based polyurethane floor varnish contains at least 40% of the substance in the dry residue, due to which it has a low cost compared to compositions based on chemical solvents.
Polyurethane varnishes have the following advantages:
- deep penetration of the composition into the surface provides it with high strength and elasticity;
- environmental safety and non-toxicity of the material;
- surface resistance to moisture, ultraviolet rays, temperature extremes;
- high drying speed;
- durability;
- promote the formation of a dense film on the surface with an increased level of wear resistance, resistance to mechanical damage and shock loads, penetration of dirt into the pores of the coating;
- the composition provides a transparent surface that does not turn yellow over time, which allows you to emphasize the natural pattern of wood, fixing it in its original form, providing reliable protection against abrasion;
- due to active polymerization and low tension, the film after drying
- does not crack or exfoliate;
- varnish treatment of a wooden surface minimizes the likelihood of bacterial growth and the attraction of rodents;
- the composition interacts well with acrylic dyes, which allow you to obtain various shades of the surface.
The disadvantages include a persistent unpleasant odor at the time of application to the surface and the high price of polyurethane varnish.
Varieties of polyurethane varnish for wood
There are two types of polyurethane varnish: one-component and two-component. The first option is immediately ready for use. It has a liquid consistency. This material is often produced as an aerosol. It is used for a small area. Most often they are covered with wooden furniture and decorative elements.
Helpful advice! The consumption of aerosol formulations is higher than that of liquid varnishes, so the material must be purchased with a margin.

Most often, polyurethane varnish has a liquid consistency and is ready for use immediately after opening the can
The main advantage of one-component varnish is the absence of organic solvents and other toxic compounds in it. When dry, it is not able to release harmful substances into the air. One-component compositions are inferior in terms of quality to two-component ones.
Two-component polyurethane varnish for wood consists of a base and a hardener, which should be mixed in a certain proportion as indicated in the instructions. This composition is most often used for large surfaces.
Important! After mixing the components, the material retains its original performance for 4-5 hours.
There are also self-leveling compounds that provide an even, durable surface.They are often used for coatings with visible structural defects.
To reduce the cost of the material, some manufacturers dilute the polyurethane varnish with acrylic, which negatively affects the performance of the composition. Therefore, when choosing quality products, it is important to consider how much wood varnish costs. Cheap formulations are not able to provide the desired result.
Depending on the area of use, two-component varnishes can be for yacht, for plastic, furniture, parquet and universal. The latter option is intended for any type of surface. There are no latex components in plastic varnishes. Yacht compositions are actively used for finishing wooden yachts. It is also suitable for all wood surfaces. Yacht floor varnishes are characterized by high moisture resistance.
Polyurethane varnish is available in transparent form. However, there are compositions of various natural shades of natural wood, which allows you to paint the surface in the desired color.
Which is better for wood: matte varnish or glossy
Polyurethane varnishes not only favorably emphasize the natural pattern of wood, but also provide reliable protection of surfaces and products from mechanical damage, shock and the harmful effects of negative factors in the form of moisture, sun and abrasive materials. They are able to extend the life of products while maintaining their original appearance.
After application, polyurethane varnish can form a semi-glossy, glossy, semi-matt or matte surface, each of which is characterized by high strength characteristics and differs only in aesthetic appearance.
The matte finish works best in rooms with diffused daylight. It is the best option for outdoor structures. Matt floor varnish emphasizes the naturalness and naturalness of the wood, making its structure more expressive. It is also able to hide small cracks, scratches and other imperfections, so that the surface does not need to be sanded too thoroughly before varnishing. In addition, the matte finish is much easier to maintain.
The glossy water-based floor polish also enhances the texture of the natural material, giving the surface an extra shine. However, on such a coating, scratches and other minor damages stand out more clearly than on matte. On such surfaces, streaks are visible, which makes it difficult to care for them. Glossy lacquer is best suited for wood furniture.
Semi-gloss and semi-gloss varnishes are "intermediate" compositions. The first option creates a slightly blurred surface, while the second gives it a subtle shine.
Varnish application technology on wooden surfaces
The method of applying varnish is determined by the composition of the material and the type of surface to be treated. Work should be carried out at a temperature of 20-23 ° C. The minimum allowable value is 13 ° C, and the maximum is 30 ° C. The relative humidity of the air should be in the range of 50-60%, which will ensure the natural process of surface drying.
There are three methods for applying varnish to a wooden base:
- The surface is pre-treated with a stain to give it the desired shade.
- A polyurethane primer is applied to the wooden base.
- The polyurethane varnish is applied to the cleaned substrate in several layers.
Before using water-based polyurethane varnish for wood, it is necessary to prepare the base, which is ensured by removing chips, cracks and other defects, sanding the surface to a smooth coating. Further, dust and dirt are removed and the surface is degreased.If the wood is previously stained to obtain the desired color, the floor varnish is applied after the coloring composition has completely dried.
Helpful advice! If a wooden surface or structure is located in a room with high humidity or is outside a building, it is recommended to pre-treat it with an antiseptic compound.
How to use pine and natural wood floor varnish
Water based polyurethane varnish for wood can be applied with a brush, felt roller or spray gun. In the latter case, up to 5-10% of the solvent is introduced into the composition.
Helpful advice! Before applying the varnish, it is recommended to brush the surface with a dry brush to remove the lint, which will contribute to a cleaner and more accurate work.
The one-component varnish is immediately ready for use. If it covers the stain or soil mixture, 2 coats of varnish will be sufficient. Each subsequent layer is applied after the previous one has completely dried, which occurs after 5-6 hours. The finishing base is completely cured after 12 hours.
Before using a two-component, wear-resistant, moisture-resistant floor varnish, it must be prepared by mixing the base and the hardener in a certain ratio. The solution should be infused for 20-25 minutes.
Related article:
Engineered floorboard: a great way to decorate your home without going overboard
What is it and how is it different from parquet. The main characteristics of the flooring, advantages and disadvantages. Leading manufacturers.
The varnish is applied to the wooden base along the surface of the fibers with smooth, slow movements, which eliminates the formation of bubbles and ensures an even distribution of the composition without streaks. When using a brush, the composition is distributed crosswise. Floor treatment should be started from the window, moving smoothly towards the door.
How to varnish concrete floors
To improve the operational characteristics of a self-leveling concrete floor, which is exposed to large and frequent loads, the surface is opened with polyurethane varnish. The base should be prepared, leveled and cleaned from dirt and dust. To do this, you can use soapy water or clean the surface with water. After which it should dry completely.
Before applying the self-leveling varnish, the dry base can be additionally vacuumed to obtain a perfectly clean surface and to achieve a high-quality painted base.
If there are no polymer components in the composition of the self-leveling floor, the surface must first be primed, which will contribute to the formation of an airtight layer. This technology will also save the amount of varnish.
Important! Concrete surfaces are coated exclusively with two-component wear-resistant floor varnishes.
The choice of the required amount of working solution is carried out taking into account its use for 40-50 minutes.
On the surface of the self-leveling floor, before applying varnish, you can create decor. For this, special stencils and coloring compositions are used. You can also use ready-made prints.
The technology of applying varnish to a concrete surface is no different from the method of processing a wooden base. First, they pass through hard-to-reach places with a brush. The varnish is applied to the surface in small areas.
Overview of polyurethane varnish manufacturers
Water-based polyurethane mixtures are presented in a wide range. However, not all manufacturers offer quality products.The best in the field of paints and varnishes manufacturing are Perti, Polistuc, KrasKo, Irakol, VGT Enterprise.
The leading manufacturer of polyurethane-based paints and varnishes is the American company Perti, which uses high-quality components and innovative technologies, which makes it possible to obtain a material with unique technical and operational properties. Such compositions provide a high-strength coating with a diamond hardness effect, which is especially valuable for flooring in high traffic areas that are subject to significant stress.
The Italian manufacturer Polistuc offers highly abrasion resistant paints and varnishes for a variety of surfaces that provide a strong and durable finish. The company specializes in the creation of odorless, quick-drying floor varnishes.
The Russian brand Irakol is engaged in the production of high-quality paints and varnishes that may well compete with foreign counterparts. However, the products are distinguished by a lower price for polyurethane varnishes (for wood and other surfaces).
A good floor varnish is offered by the Russian company KrasKo, which is known in the world for its new approaches and non-standard solutions in the production of protective compounds for different types of material. The product range includes both universal compositions and varnishes for certain types of surfaces.
High-quality certified products are offered by the VGT Enterprise, which uses imported components in the production of paints and varnishes. Polyurethane varnishes from this brand are intended exclusively for finishing wooden surfaces. The product range includes both colorless formulations and tinted pastes in natural shades.
Wood floor varnish rating
The ZAR ULTRA INTERIOR varnish opens the rating of the best polyurethane compounds for wood. It is intended for interior decoration. The composition has a smooth self-leveling formula. The coating is characterized by increased ductility, high resistance to abrasion, wear and mechanical damage, resistance to moisture and ultraviolet rays.
A good polyurethane varnish for wood for outdoor use is the composition of ZAR ULTRA EXTERIOR, which is distinguished by increased abrasion resistance, resistance to moisture, sunlight and temperature extremes, which is ensured by the presence of special additives in the material. This option is ideal as a floor varnish in the country. Thanks to special inclusions, it prevents the processes of the nucleation of microorganisms on the surface of the wood and excludes the possibility of rotting.
For parquet and natural wood flooring, a two-component composition from the German brand Neolux Elite Premium is very popular, which forms a strong, wear-resistant and durable matte surface.
The Italian brand offers Adesiv Ice, a high-quality two-component varnish for floors in baths and similar rooms with high humidity, which is available in several versions, which allows you to obtain different types of surfaces from matte to semi-gloss. The composition provides a durable coating with increased moisture resistance.
Note! This polyurethane varnish is also suitable for concrete surfaces.
Two-component varnish Berger Aqua-Seal is suitable for both indoor and outdoor use. The composition provides a strong, wear-resistant and durable coating, which, thanks to its transparent base, favorably emphasizes the structure of the wood.
Review of the best brands of parquet varnishes
When choosing which floor varnish is better, you should pay attention to the composition for protecting parquet on a polyurethane base from the German brand Dufа PREMIUM PU PARQUET LAQUER D333.It has a transparent structure and provides a glossy finish, which is characterized by increased wear resistance, resistance to abrasion, mechanical damage and chips, and durability. The varnish protects the coating from the harmful effects of ultraviolet radiation, so that the parquet will not lose its original appearance over time.
The one-component composition is easily applied both with a roller and with a spray gun, spreading evenly over the surface without the formation of spots and streaks. Complete drying of the coating occurs after 12 hours.
One-component odorless floor varnish Borma has many positive reviews. It provides a reliable protective covering of the parquet, which can withstand any mechanical and shock loads.
The reliable protection of the parquet floor is provided by the Triumph polyurethane parquet floor varnish, which can also be used on other types of surfaces, including metal and concrete. The composition is easy to apply, dries quickly, but has an unpleasant odor. The finished coating exhibits increased resistance to moisture and temperature extremes.
The combined composition of polyurethane and acrylic 3V3 Vitrificateur Protection provides intensive protection of the surface against mechanical damage and shock loading, increased elasticity and wear resistance. The varnish has a high drying rate. The next layer can be applied after 30-40 minutes. Only a brush or roller is used to apply the varnish.
Helpful advice! The composition of 3V3 Vitrificateur Protection is environmentally friendly, therefore it can be used for living rooms and children's institutions.
Tikkurila Taika Glow parquet varnish is a non-standard option with a unique light accumulation quality. The composition not only provides reliable protection of the surface from mechanical stress, but also glows in the dark due to the ability to accumulate light from natural and artificial light sources in the daytime. Tikkurila floor varnish is easy to apply with a roller or spray gun and does not emit an odor.
Among the wide range of protective floor coverings, polyurethane varnish is recognized as popular. The composition provides reliable protection of the coating from various loads and influences. In order for the coating to last for many years, it is important to choose a quality material and adhere to the recommendations for its application.