Modern awnings, thanks to the use of the latest building materials in their designs, can have a wide variety of configurations. Owners of their own estates and country houses especially fell in love with polycarbonate canopies for a private house with their own hands: photos of convenient and practical structures convince of their extraordinary versatility. Covering most of the yard polycarbonate canopy, you don't have to worry that a sudden rain will catch you by surprise, forcing you to collect garden tools, shoes, equipment left on the street. The structure, attached to the house, will hide the car from the scorching sun, and if you are planning to have dinner with friends in the fresh air, the meeting will not have to be postponed due to bad weather.
Content [Hide]
- 1 Types of canopy structures attached to the house
- 2 Canopy materials: which polycarbonate is better
- 3 What is the best thickness of polycarbonate for canopies
- 4 DIY polycarbonate canopy drawings
- 5 Do-it-yourself polycarbonate canopies to a private house: photos of universal structures
- 6 How to make polycarbonate awnings with your own hands
Types of canopy structures attached to the house
Both for sheds installed separately and for structures adjacent to the house, a single rule applies: structures must be combined with existing architectural forms and fit into the overall landscape design. The awnings attached to the house rest on the racks on one side, and on the other are statically attached to the wall of the house, garage or fence. There are several types of frames for such structures:
- awnings with shed roof - the most familiar simple structure. The installation technology is quite simple. When calculating the angle of inclination of a flat roof, the possibility of rapid melting of snow cover in winter is taken into account;
- gable structures are common roof forms that have two slopes. The angle of inclination in such structures is 35-45 degrees, which ensures snow melting under its own weight and the absence of stagnant rainwater. Recently, gable canopies with concave and curved slopes are gaining popularity;
- the arched (semicircular) shape of the roof is an actual design from the standpoint of functionality and originality. The emergence of the newest materials with plastic properties made it possible to successfully use such structures for awnings, canopies and other structures. A semicircular roof facilitates timely snow removal.The bending radius of the arch depends on the minimum allowed by the manufacturer for the material used;
For self-production and installation of a polycarbonate canopy, especially if the work is done for the first time, it is recommended to choose a design with pitched roof... It is quite simple to manufacture and you can handle the installation without having special skills.
It will be much more difficult to design, manufacture and install domed or arched polycarbonate canopies to a private house with your own hands (photos on the network show the complex designs of such structures). Here it is necessary to take into account the directions of the channels in the panels of cellular polycarbonate, the permissible bending radius, the thickness of the material and other points that require certain knowledge and skills.
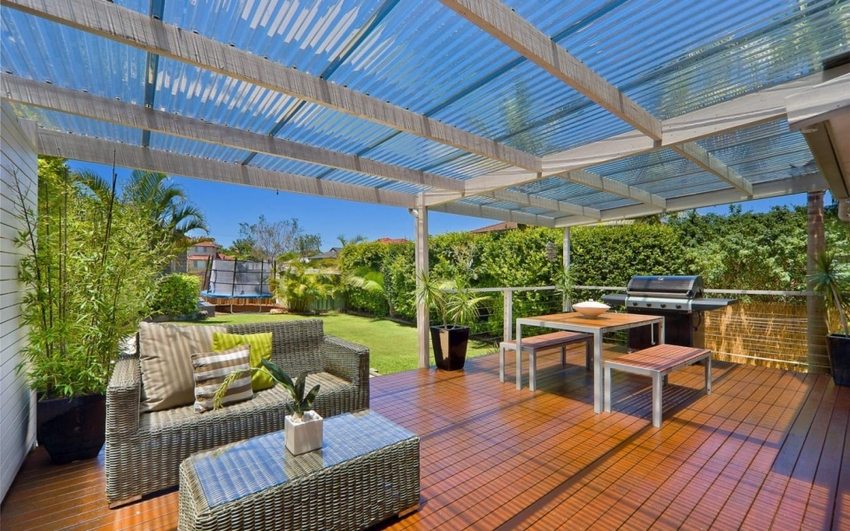
Polycarbonate is distinguished by its ability to transmit sunlight well, while protecting from harmful radiation
Canopy materials: which polycarbonate is better
The canopy is a simple structure in the form of a roof mounted on support posts. For supports, you can use wood (logs or beams), a metal profile pipe with various sections, as well as brick posts. A metal profile and a wooden beam are also used for assembling the frame, only the section is selected smaller than for the supports.
The material for covering canopies can be varied. It is the roof that gives the structure a certain appearance. It can be plastic slate, asbestos-cement slate, metal tile, copper sheets, corrugated board, polycarbonate.
Due to a number of unique properties, polycarbonate is the most demanded as a covering for awnings. This material is in many ways superior to metal and glass, not inferior to them in environmental friendliness and strength. The high resistance to loads of cellular polycarbonate in comparison with glass is determined by the presence of longitudinal stiffeners of the cellular structure.
Although monolithic polycarbonate is stronger than cellular polycarbonate, each has its own advantages. The choice to cover one type or another directly depends on the requirements for the structure.
Solid polycarbonate has an incredible light transmittance of up to 90%. Honeycomb samples have slightly lower translucent qualities, but at the same time they perfectly scatter light and create a barrier to ultraviolet radiation. The use of cellular polycarbonate sheets for awnings is due to the following properties:
- high structural strength - several layers, interconnected by stiffening partitions at different angles, form a cellular structure, providing high strength;
- stability, ability to withstand strong wind and snow load;
- impact resistance - the material not only does not form fragments upon rupture, but also almost does not deform under mechanical stress;
- flexibility - it is possible to give the material any required shape without deteriorating its characteristics;
- high percentage of light transmission with UV protection;
- resistance to temperature fluctuations - can be operated at temperatures from -40 to + 55 ° C;
- light weight - allows for installation without resorting to the use of special mechanisms (the material is 15 times lighter than glass of the same size);
- ease of cutting - the material is perfectly processed with cutting tools, drilled, and there are no fragments;
- fireproof - a hardly flammable material, self-extinguishing upon termination of contact with a fire source. The hole formed during the melting allows the smoke to escape, eliminating the risk of suffocation;
- resistant to chemical and atmospheric influences;
- durable - retains its properties throughout the entire period of operation, which is 10-11 years;
- easy to care for - does not require additional processing, can be quickly cleaned.
As for the aesthetic component, manufacturers produce not only colorless transparent sheets, but also samples with a range of colors. This allows you to give structures made of cellular polycarbonate a spectacular appearance.
Helpful advice! When choosing the color of polycarbonate for covering the canopy, you should give preference to tones that do not distort the natural colors of objects located under the structure. When using panels of red and orange, all objects will have a corresponding characteristic shade.
What is the best thickness of polycarbonate for canopies
The characteristics of polycarbonate are largely determined by the structure of the material: the cellular panels are hollow, their specific gravity is much lower than that of solid sheets. Consequently, their cost is lower.
The parameters for choosing polycarbonate for awnings are: its decorative features, geometric shapes, purpose, economic indicators.

The canopies adjacent to the house are supported on one side of the racks, and on the other they are attached to the wall of the capital structure
It is recommended to use for awnings polycarbonate thick 4 mm or more. You can analyze the parameters of various types of panels based on their performance properties:
Parameters and properties of polycarbonate panels | Units | Honeycomb structure | Monolithic structure |
Standard width | m | 2,1 | 2,05 |
Sheet length | m | 6/12 | 3,05 |
Specific gravity of the material | kg / cm² | 1,3 | 7,2 |
Minimum bending radius | m | 1,05 | 0,9 |
Thermal resistance | m² ºС / W | 0,28 | 0,2 |
Duration of operation | year | 12 | 25 |
Translucency degree | % | 82 | 90 |
When determining the optimal thickness of honeycomb panels, the purpose of the canopy and the degree of load on the structure are taken into account. For sheets with a honeycomb structure, consider the following:
- polycarbonate with a thickness of 4 mm is used for small canopies with maximum rounding (canopies, greenhouses);
- sheets with a thickness of 6-8 mm cover structures of significant area that can withstand the effects of strong winds and snow loads (sheds for the courtyard, parking places, swimming pools);
- sheet thickness of 10 mm is used for the operation of the structure under extreme environmental conditions.
The thickness of the monolithic polycarbonate panels can vary from 4 to 12 mm. This material is twice as strong as its cellular counterpart. The most commonly used thickness of a solid sheet for awnings is 4-6 mm, which may well guarantee the strength of a structure in any climatic conditions.
DIY polycarbonate canopy drawings
In order for the manufacture, assembly and installation of the structure to be carried out without any unexpected difficulties, you should develop a drawing of a polycarbonate canopy with your own hands. This will allow you to properly prepare all the elements of the frame and avoid possible waste of materials. Sketches of the future construction should take into account the design features of the selected shape of the canopy. If possible, the parameters of the adjacent structure are chosen such that when cutting pipes and cutting plastic, as little waste as possible remains.
If an arched structure is chosen, the frame of which is made of a shaped pipe, it is necessary to have special equipment for bending pipes. Not everyone has such a tool at hand, but, even with a pipe bender, it is quite difficult to give the material a correct bend in shape.
Cutting polycarbonate for a semicircular structure is also fraught with some difficulties. Therefore, for work performed independently, it is recommended to opt for a shed polycarbonate canopy. For the frame of this design, it is much easier to calculate the amount of a profile pipe and cut out the required polycarbonate sheets.
Helpful advice! In the design diagrams, such a distance between the transverse elements of the crate should be provided so that the joint line of the panels falls on the profile pipe of the frame. Thus, the polycarbonate coating will be rigidly fixed.
When covering the roof with polycarbonate, you should take into account the installation features of this material:
- typical polycarbonate panels are produced in lengths of 6 or 12 m and a width of 2.1 m. Based on these parameters, the dimensions of the structure are calculated, which allows you to get as little waste as possible;
- the panels are connected to each other using end profiles (their length is 6 m), which can be matched to the color of polycarbonate. They are securely attached and do not require additional fixation;
- the length of the end profile covering the final cut is 2.1 m;
- for covering semicircular roofs, the polycarbonate sheet is positioned so that the bend is in the transverse direction of the air channels;
- the location of the sheets of cellular polycarbonate should be such as to ensure the unhindered drainage of condensate from the internal channels. Otherwise, the honeycomb inside the plastic will become moldy, which will affect the light transmission qualities;
- in pitched canopy structures, the upper end of cellular polycarbonate is closed with a continuous self-adhesive tape to avoid moisture, dust, insects. The lower end is processed with a perforated tape, which allows moisture to be discharged outside. In arched canopies, micro-perforated tape is used at both ends;
- the mounting holes are created with a slightly large diameter, which will allow the polycarbonate to expand or contract freely depending on the temperature. Do not make the holes too large;
- when installing panels, self-tapping screws with thermal washers are used, which are selected in the color of polycarbonate.
Helpful advice! The use of thermal washers of the appropriate colors gives the coating a neat aesthetic appearance and excludes moisture and dust from entering the polycarbonate panel through the mounting hole.
The project also provides for the thickness of polycarbonate corresponding to the selected design:
- awnings of impressive size with an inclined shape - sheets 10 mm thick;
- arched and semicircular awnings - an 8 mm panel will do;
- for adjoining sheds of a lean-to design with a gentle slope, polycarbonate is chosen with a sheet thickness of 16 mm, capable of withstanding a possible snow load in winter.
All these nuances should be taken into account before installing a polycarbonate canopy to a private house with your own hands. A photo of self-made structures will serve as an example for the manufacture of your unique structure.
Do-it-yourself polycarbonate canopies to a private house: photos of universal structures
Carports adjoining the home tend to cover most of the yard. Some people prefer to close the entire local area. This approach contributes to the universality of the use of structures:
- it is easy to place a car under it, protecting it from rain, hail, snow;
- the canopy will protect the paving slabs in the yard from premature destruction and cracking;
- thanks to Aweigh the porch and steps will always remain dry, which eliminates the possibility of slipping;
- the design will exclude wetting of garden tools and equipment, various items left on the street;
- thanks to the translucency of polycarbonate, under the canopy can be placed mini flower beds;
- very convenient is the outlet of the water pipe to the yard. Thanks to the hinged cover, you can do household chores without going into the house during the entire summer period in any weather: wash dishes, vegetables and fruits, preserve food, etc.;
- a functional structure is a canopy for a summer residence: those who like to harvest and dry fruits do not have to worry that direct sunlight or moisture will fall on the raw materials;
- with the arrival of autumn, the sheltered courtyard will not have to be constantly cleared of falling leaves and branches, and in winter, you will not have to spend a lot of time clearing snow.
Using carports made of polycarbonate for a car, you save it from many negative effects:
- polycarbonate coating protects the paintwork layer of the car from sunlight, keeping it in perfect condition;
- the roof of the canopy will become an obstacle to rainfall and small objects falling on the body. In winter, it protects against snow drifts;
- a car parked under a canopy is well ventilated, which protects body elements from corrosion;
- unloading or loading things into the car, especially in inclement weather, is much more convenient under a canopy;
- the space protected by the canopy can be used for servicing and repairing the car, regardless of weather conditions;
- even if there is a garage in the yard, it is often more convenient to leave the car under a shed if you need it after a while.
It is very convenient to use the area under a canopy for family breakfasts and dinners in the fresh air, especially if the structure is adjacent to the wall in which the kitchen windows are located. In this case, the hostess will come in handy to serve dishes and cooked dishes directly from the kitchen to the street. You can also quickly cope with cleaning dishes after a feast.
The canopy that protects the porch and the entrance to the house allows you to leave the shoes used in the yard and garden outside the door without fear of getting wet, which contributes to keeping your home perfectly clean. And the canopy attached to the house, the covering of which protects the balcony or terrace, will make it possible to place a comfortable soft leisure furniture.
How to make polycarbonate awnings with your own hands
Before proceeding with the independent manufacture of a polycarbonate canopy adjacent to the house, it is necessary to decide what materials the racks and the frame of the structure will be made of.
Material selection
For the support posts of the wooden structure of the awnings, a beam of various sections is used, for the lathing - a board. Wood is an environmentally friendly material that is easy to process and lasts for a long time with proper care, and the structure from it will cost less than metal. In addition, when working with wood, there is no need for a welding machine and special skills. Among the disadvantages can be noted the ease of inflammation, susceptibility to decay. Therefore, it is necessary to monitor the design and treat wooden surfaces with special compounds in time.
In metal structures, a profile pipe of various sections is used. The recommended metal thickness is at least 2 mm. Metal structures have high strength, resistance to moisture, long service life. To prevent corrosion, the metal surface is primed and painted. To connect the parts, welding or bolting is used. You can give the canopy structure an elegant openwork look by using forged elements. However, forged structures will cost much more.
Installation and concreting of wooden poles
Before making a canopy, you should determine the amount of material required for the structure. All calculations are made in accordance with drawings and sketches. It is recommended to purchase material in an amount 5-10% more than the calculated one: this will allow you to quickly replace incorrectly prepared or damaged elements.
To make a wooden canopy with a polycarbonate roof, you will need the following materials:
- timber with a section of 150x150 mm - for supporting posts and for horizontal frame beams. The required amount of material depends on the length and width of the structure;
- board for rafters, purlins with a section of 100x150 mm. The number depends on the distance between the rafters. For a polycarbonate coating, a step of 0.5-0.7 m is selected;
- fasteners, hardware;
- polycarbonate sheets.
They start by marking the territory. Points are outlined where the vertical support posts of the canopy will be located.The height of the supports is taken equal to the height of the canopy, taking into account the depth of the racks by 55-60 cm.
Helpful advice!When marking, it should be taken into account that the removal of the roof of the structure from the outside should be 15-20 cm.
Supports, as a rule, are located at a distance of 1-2 meters from each other. The step between the supports is selected depending on the length of the structure and the thickness of the roofing. First, the racks are installed next to the wall of the house, and then a row of racks on the outside of the structure. All supports should be located clearly opposite each other. The height of the racks must take into account the slope provided by the project.
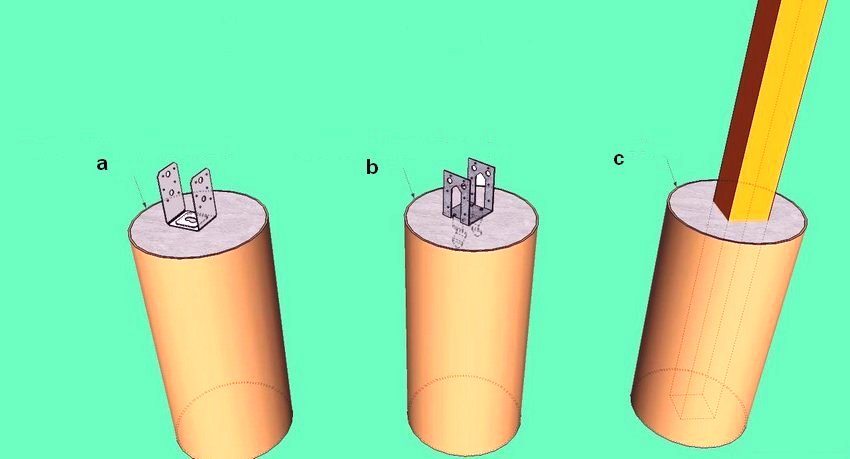
Methods for installing support pillars: a - dismantled anchor (anchor); b - double-sided anchor (anchor); c - into concrete
For concreting the supports, pits are arranged with a width and depth of half a meter. A layer of sand and gravel is poured into the bottom of the pits. Then the support is installed, which has previously been subjected to antiseptic treatment and wrapped in a waterproofing material. Check the verticality of the installation and pour concrete. In this form, the support is left until the concrete mixture has completely set.
Frame fabrication
The construction of a wooden frame starts from the inner row from the wall. Wooden beams are mounted to the support posts. To obtain the required length, the beams are joined together using metal plates. The position of the beams must be strictly horizontal. The beams are fastened to the supports using self-tapping screws. In addition, the beams are additionally attached to the wall of the house by means of fasteners.
Once the horizontal beams are installed, fasteners for the cross members are mounted to them. In order to make the structure more rigid, it is recommended to reinforce the beams with spacers on both sides of the support posts. The spacers are fixed with self-tapping screws at an angle of 45 degrees.
Next, proceed to the installation of the transverse elements. As a rule, the beams are mounted first at the edges, then the middle and then the intermediate cross beams. Once all the joists are in place, the edges are closed with an end board. For the strength of the structure, the extreme beams on the left and right are strengthened with rafter legs. This will strengthen the structure in case of possible excessive snow load.
Covering the frame with polycarbonate sheets
Coating the frame with polycarbonate begins with cutting out the plastic, the surface of which is marked with a marker. The polycarbonate is cut along the marked lines with a circular saw, the blade of which has fine teeth. When cutting sheets, they should be well fixed so that there is no vibration. After that, the channels of cellular polycarbonate are cleaned of shavings and sawdust. When cutting material, it is necessary to take into account the location of the channels inside the polycarbonate: they must be located in such a way that moisture can drain freely.
After the material is cut, it is placed on the frame and the places of fasteners are marked.Here you need to take into account that the distance from the edge of the sheet to the first hole should be more than 40 mm, and the spacing of the fasteners should be 35-45 cm. Further, in the designated places, mounting holes are drilled with a slightly larger diameter than that of the self-tapping screw. When all the holes are made, the polycarbonate sheets are fixed to the frame. When fastening the sheets, self-tapping screws and thermo washers are used. After fastening the self-tapping screw, the cap for the hole in the cap snaps into place, which ensures complete sealing of the fastening.
Polycarbonate panels are connected to each other with a plastic profile, which is selected to match the color of the sheet. You should also make sure that the joint line of the panels falls on the transverse elements of the sheathing.
Related article:
Sheds in the courtyard of a private house: photo of light and graceful designs. Forms and construction of awnings. Photo of carports. A canopy from a profile pipe. Decking for covering awnings.
As soon as the polycarbonate panels are fixed on the frame, they begin to process the ends of the coating. The upper ones are closed with a special aluminum tape, which prevents dust and moisture from entering the sheet. And the bottom end is sealed with a special tape with perforation, which not only prevents dust from entering, but also ensures the drain of accumulated condensate. After completing the installation, you can equip the awning with a water drain.
Polycarbonate-coated sheds attached to the house are simple, but widely used structures that can well be made and installed on their own. Such structures do not require additional reinforcement using trusses. The main thing is to choose the right angle of inclination, which will ensure smooth and fast snow melting.