Reinforced concrete blocks are widely used in the construction of objects for various purposes. The products are used in the construction of foundations, wall panels and partitions. Blocks come in a wide variety of views, with elements differing in scope and size. Reinforced concrete products are characterized by high technical and operational qualities, which are regulated by the current regulatory documents.
Content [Hide]
- 1 Reinforced concrete blocks: design features of products
- 2 Typical advantages and disadvantages of reinforced concrete blocks
- 3 Varieties of reinforced concrete blocks, depending on the purpose
- 4 Types of bulk reinforced concrete blocks depending on the length and type of concrete
- 5 Features of marking of reinforced concrete products
- 6 Varieties of wall concrete blocks and their area of use
- 7 Characteristics and varieties of reinforced concrete rings
- 8 How to build a basement from concrete blocks: sequence of actions
- 9 Secondary use of reinforced concrete blocks in the construction of buildings
- 10 How to make wall or ventilation reinforced concrete blocks at home
Reinforced concrete blocks: design features of products
The reinforced concrete block is made in the form of a rectangular parallelepiped, which is made of concrete reinforced with steel reinforcement. From the end sides, the product has vertical cavities necessary for a reliable connection of the elements during the formation of masonry. For this, the hollow spaces in the trapezoidal prisms are filled with mortar. On the upper plane there are two metal brackets for carrying out loading and unloading activities when transporting reinforced concrete blocks and performing installation work.
Reinforced concrete products are used in the construction of the foundations of facilities at the zero stage of construction, basement walls, basement floors, the formation of prefabricated strip foundations, the construction of technical premises, underground passages, residential buildings. You can also use concrete blocks for the fence.
Correctly selected modifications and dimensions of products, due to the ability to evenly distribute the load, will provide a solid foundation and immobility of the frame of structures.
Reinforced concrete products are manufactured in factories using the vibrocompression method, which ensures a high level of strength, reliability and rigidity of blocks. Reinforced concrete products are made of concrete of classes B7.5 to B15. The finished working mixture is poured into special molds, where the solution can be pressed. The finished products are kept under certain conditions, acquiring the required level of strength.
Typical advantages and disadvantages of reinforced concrete blocks
Reinforced concrete blocks are distinguished by increased frost resistance, moisture resistance, low thermal conductivity, resistance to temperature fluctuations and fire, which allows them to be used in regions with different climatic conditions. The blocks are capable of withstanding up to 50 cycles.
The products are characterized by vapor permeability, resistance to external influences, unfavorable chemical and biological factors, good sound and heat insulation properties, environmental friendliness, high resistance to static and dynamic loads, and a long service life of up to 100 years. This makes it possible to build a full-fledged house from concrete blocks.
The laying of reinforced concrete blocks is carried out according to the principle of assembling the designer, which helps to reduce the amount of work and time, and reduce labor costs. This is best reflected in the economic component of construction. When assembling products, the installation and subsequent dismantling of the formwork is not required. In addition, after the construction of the structure, there is no need to wait for the moment of concrete hardening.
The disadvantages of the blocks include their large weight and cumbersomeness, in connection with which it will be necessary to attract special equipment to perform masonry work. When erecting foundations from blocks, insufficient tightness is observed in the zone of butt joints, which requires the arrangement of waterproofing. Another disadvantage is the high cost of concrete blocks in comparison with other building materials.
Varieties of reinforced concrete blocks, depending on the purpose
All reinforced concrete blocks, regardless of their dimensional parameters, can be divided into three types: FBS, FBV and FBP.
The most common type of blocks in construction is FBS. Block foundations, lintels in basements, walls of structures are erected from them. The sizes of reinforced concrete blocks are varied, which is reflected in the special marking. The distinctive advantages of the products include increased resistance to existing loads and low thermal conductivity. Installation of elements can be carried out on a sand-gravel base or directly on the soil.
FBV blocks are represented by monolithic structures and are made exclusively to order for a specific construction object. The main distinguishing feature of the elements is a longitudinal groove, which is used for laying utility lines. The products are manufactured in lengths of 880 mm, height 580 mm and widths of 400, 500 and 600 mm. For the manufacture of blocks, concrete of grade B7.5 and higher will be used. These elements are laid in the underground for technical purposes and in the ceiling area of the basement structures.
FBP products are hollow concrete blocks. They are available in lengths of 238 cm. Inside the elements are square voids. Such blocks are unable to withstand a significant load, since they are not highly durable. However, they are characterized by high thermal insulation properties. FBP should be used in the construction of light structures, frame structures, erection of partitions in basements. These blocks are made of concrete grade M150, which is reinforced with structural steel. Hollow structures are more expensive. This is due to the laborious technology of their production.
Types of bulk reinforced concrete blocks depending on the length and type of concrete
The reinforced concrete block is produced in lengths of 20-240 cm. The width and height of the products are also standardized. All blocks can be divided into short, medium and long. The first design option is characterized by a low weight, reaching 31.7 kg. The dimensions of the concrete block are 20x20x40 cm.
Medium-sized elements include concrete blocks for pillars and other structures with a length of 1180 mm, a height of 280 and 580 mm, a width of 400, 500 and 600 mm. Large-sized items are produced with a length of 2380 mm, a height of 580 mm and a width of 300-600 mm with a step of increasing the size of 100 mm.
Different types of blocks can be made of heavy, light composition or expanded clay concrete. In the first case, concrete of grades M250, M300 and M400 is used, which ensures the density of products up to 2400 kg / m³. One element has a weight of 300 kg, depending on the size of the product. Heavy concrete blocks are characterized by high frost resistance and thermal conductivity.
Important! If granite filler was used in the production of blocks, they can be used for the construction of buildings on acidic soils.
For light composition, concrete mixtures of grades B100 and B150 are used, providing concrete density from 1800 kg / m³. The weight of a concrete block is in the range of 0.3-1.63 tons. Such products are used for construction on dry soils.

Reinforced concrete blocks can be made of expanded clay concrete, as well as light or heavy compositions
In the production of expanded clay concrete blocks, expanded clay is used, which is characterized by high thermal insulation properties. However, products are quickly saturated with moisture, which requires the organization of a waterproofing layer to protect structures. The density of the material is less than 1800 kg / m³. The weight of one product is in the range of 260-1500 kg. This type of block is used for the construction of small lightweight structures such as a garage or a bathhouse.
Features of marking of reinforced concrete products
Each manufacturer, which is engaged in the production of concrete blocks, carries out their marking, which is regulated by the current standard. This product designation provides complete information about the type and size of concrete blocks. The price of products may also depend on these characteristics.
Important! Marking of all reinforced concrete products is necessary in order to determine the required number of elements to complete the assigned construction task.
The three capital letters in the name of the reinforced concrete blocks indicate the type of product, providing information about the structural features of the structure. This is followed by a digital index, which consists of a group of numbers that indicate the dimensions of the block in decimeters. It should be borne in mind that all values are rounded to the nearest whole number. For example, a block 118 cm long, 40 cm wide, 28 cm high will be designated FBS 12-4-3.
The last capital letter indicates the type of concrete from which the product was made. The letter "T" indicates heavy concrete, "L" - about light composition, "P" indicates that expanded clay is present in the elements, and "C" denotes silicate products.
Varieties of wall concrete blocks and their area of use
Wall concrete blocks are used for the construction of walls and partitions. They can be hollow and full-bodied. The first option is suitable for wall construction work. Solid concrete blocks are recommended to be used to create load-bearing supports, foundations of basements and technical rooms.
Products are available in different shapes and sizes. Concrete blocks can be reinforced with a reinforcing component or have special grooves used for laying reinforcement. Regardless of this, products are divided into subspecies, which is determined by the specifics of use. Many manufacturers have decorative concrete blocks for facade cladding in their product range. They have a different color and texture. Products that imitate torn stone are in great demand.
Cloisonné concrete products are lightweight and lightweight. The tongue-and-groove elements are distinguished by a specific shape, which allows you to reduce the cost of masonry material and erect a structure in the shortest possible time.Concrete blocks with internal holes provide convenience when transporting and installing products. Monolithic elements and floor slabsi are used to create load-bearing wall structures.
Hollow elements can be reinforced or lightweight. They are also divided into one-, two- and three-hollow blocks. Some manufacturers produce slotted products that have 4-8 parallel slots. To create lintels, erect door and window openings, during the construction of facilities for water drainage, supplying communications, laying hidden wiring, U- or U-shaped concrete structures are used. Additional items are used as non-standard elements.
Characteristics and varieties of reinforced concrete rings
Reinforced concrete rings are made from a cement mixture by pouring into a special form where the reinforcement is laid. The products are widely used in the construction of wells, tunnels, filtration and gas pipeline systems, for laying utility lines.
Reinforced concrete rings are available with and without rebates. Simple products have smooth and flat edges. Rings with rebates are characterized by a notch at the base and protrusions at the end. Such elements will contribute to the creation of a reliable and sealed structure of rings, which are attached to each other using lock joints.
Depending on the purpose, which reflects the marking of products, reinforced concrete rings are divided into the following types:
- KO - supporting products that are laid in the foundation of the well;
- KS - wall rings laid in the narrowed areas of the wells;
- KVG - elements for gas and water supply wells;
- KFK - rings designed for collectors and drainage networks;
- KLK - products for water treatment systems.
Important! Reinforced concrete rings are produced in the form of conventional products and elements, completed with a bottom and overlap of the appropriate size.
In the case of the construction of an object of considerable width, where several rings are needed, you can order a monolithic structure, which is made according to individual dimensions. In this case, there are no seams, which eliminates the possibility of leaks.
Reinforced concrete rings are available in round or square shapes. The outer diameter of the products is from 84 to 220 cm, the inner diameter is from 70 to 200 cm. The wall thickness is 7-10 cm. The standard height is 29, 59 and 89 cm. The first size is typical for rings with an inner diameter of 70 cm, and the last one is for products with a size of 2 m.
How to build a basement from concrete blocks: sequence of actions
The basement is often used for storing food and other items. It is better to make a structure of a semi-buried type, since in this case the possibility of flooding the premises with groundwater is excluded. For the construction of the foundation and walls, products are used that are regulated by GOST 13579-78. Concrete blocks are made of heavy concrete and have a density of 2 t / m³.
The first step is to select a site for construction. It is marked with pegs with the plotting of the axes of the structure. According to the markings, a pit is being developed, the depth of which is determined by the dimensions of the structure and must be at least ½ of the height of the building. After the excavation works, drainage, leveling, leveling and compaction of the pit bottom are carried out. A 15 cm high sand and crushed stone pillow is laid on the base. The bedding is soaked in water and compacted.
Related article:
Hollow core slab: an important element for building reliability
Design features and characteristics of the material. Basic parameters, bearing capacity indicators.Pros and cons of using panels.
By means of diagonal measurements, the right angles of the structure are determined. Next is the outline of the waterproofing material to protect the foundation elements. For this, roofing material or concrete mortar is used, reinforced with tied reinforcing bars.
Since the concrete blocks for the basement walls are of sufficient weight, they are laid with the use of a crane. Corner elements are laid on the waterproofing. Concrete blocks are laid according to the principle of erecting a brick wall. A 2 cm thick masonry mortar is used to connect the elements. Each row should be checked for horizontalness.
Important! When laying a foundation from blocks, it is necessary to leave ventilation gaps in the structure.
Each subsequent row of concrete blocks with their own hands is laid on the mortar and, according to the principle of displacement of the elements, is tied with the previous row. If cushion slabs are used in the base, the central parts of the FBS of the second row should be located above the vertical seams of these slabs or in the middle of the gap between them. The spaces between the slabs are concreted.
At the end of the construction of the last row, the crown of the foundation is put into the formwork around the entire perimeter and a concrete grillage is created. After removing the formwork, the outer part of the structure is coated with a waterproofing material and covered with a roll. Backfilling of the excavation is carried out.
Secondary use of reinforced concrete blocks in the construction of buildings
For the construction of the basement foundation, construction of a garage or other small non-residential building, you can safely use used reinforced concrete blocks. This will significantly save on material, which will lead to a reduction in the cost of the construction process.
However, when purchasing used reinforced concrete blocks, you should weigh all the advantages and disadvantages of this event. The main advantage is the relatively low price of concrete blocks 200x200x400 mm. It is only 40 rubles. per piece, while the price of a concrete block 20x20x40 cm from the manufacturer is about 70 rubles.
Before purchasing used reinforced concrete blocks, it is recommended to check each element for the integrity of the structure, the correct geometry of the product, for the presence of visible microcracks, defects and corrosion processes of the reinforcement. Products must have complete fasteners.
Important! When buying used reinforced concrete blocks, you should find out the conditions and period of operation of the products, which is important for choosing the scope for further use and the application of protective measures.
Boo foundation blocks not recommended for use in high humidity and low load conditions.
How to make wall or ventilation reinforced concrete blocks at home
To make concrete blocks with your own hands, you will need cement of the M400 or M500 brand, sand with a fraction of no more than 1.5 mm, crushed stone and water. The sand must be free of debris and dirt. Better to use a career lineup.
First of all, dry components are mixed in a ratio of 1 part of cement and 7-9 parts of fillers, liquid is gradually added to the composition in a proportion of 0.5 part. When mixing the solution, special attention is paid to its consistency. The thinner the mass, the lower the strength of the product. To increase the indicators of strength, moisture resistance and frost resistance, a plasticizer can be added to the mixture.
Useful advice! A vibrator will provide a quick and effective preparation of mortar for blocks.
You should first prepare special forms for reinforced concrete blocks.They are made of durable material that can withstand the significant weight of the finished product. For this, silicone, iron formwork or laminated plywood molds are suitable. The form must be of such a size as to obtain a ready-made concrete block 400x200x200 mm. It is also possible to make blanks for half-pieces of 200x200x200 mm, which can be used in the construction process as additional blocks.
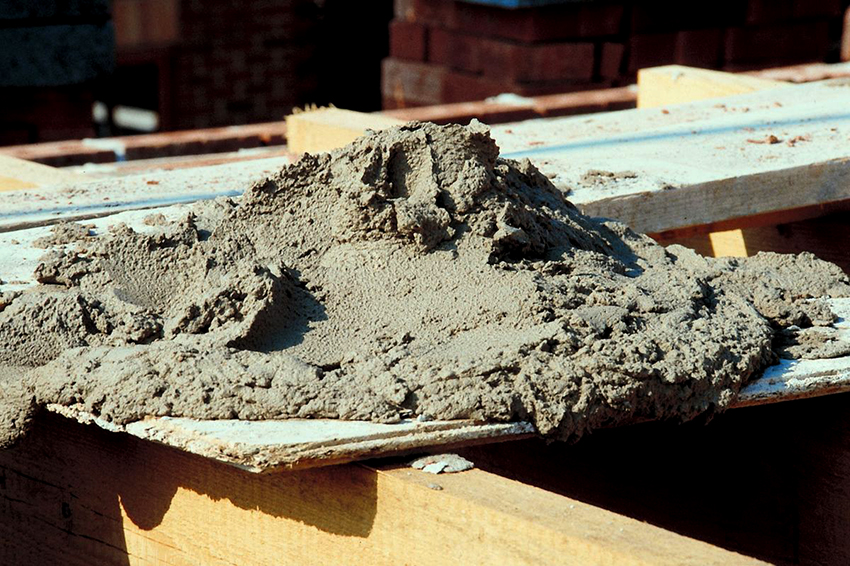
To make reinforced concrete blocks with your own hands, you will need cement, crushed stone, sand and water
Forms for concrete blocks 20x20x40 cm are lubricated with machine oil or special grease, which will facilitate easier removal of the product from the formwork. Next, the containers are filled with a ready-made mortar, followed by its reinforcement, then it is carefully compacted. To obtain voids, pre-oiled bottles can be used.
After shrinkage and preliminary hardening of the mixture, which occurs in 1-2 days, the product is removed from the mold and stored in a dry room with good ventilation until the moment of full strength gain. This will take at least 2-4 weeks.
The reliability and durability of the future structure depend on the correct type and size of reinforced concrete blocks. The use of products reduces the duration of the zero cycle, speeds up the process of performing work, reducing labor costs and the amount of masonry material. However, in this case, one should not forget about the rather high price of concrete blocks. Due to the high technical and operational characteristics of the material, it will be possible to build a solid structure that will not cause any problems for many decades.