At the heart of any floor and ceiling is a hollow core slab, which plays the role of a horizontal support that directly affects the stability of the building. Not a single panel or frame building could do without these slabs, with which all interfloor ceilings were made. Basically, the material is made from various types of concrete. The characteristic feature is the presence of longitudinal voids, and the main advantages are light weight and long service life.
Content [Hide]
- 1 Basic types and sizes of hollow core slabs
- 2 The main types of markings: what data can be found from the name
- 3 What are hollow core slabs and how are they made?
- 4 Hollow core slab: design features
- 5 The main advantages of using hollow floor panels
- 6 Types of loads for which floor slabs are designed
- 7 Floor slab weight and other important product parameters
Basic types and sizes of hollow core slabs
More recently, GOST 9561-91 regulated the production process of hollow-core floor slabs, according to which the products were specially marked. In the passport, a certificate was attached to the building material, indicating the dimensions, the grade used in the production of concrete and the load for which the slab was designed.
The specified GOST was developed back in Soviet times and, obviously, needed improvement. Therefore, from June 1, 2017, a new standard has been put into effect in the territory of the Russian Federation. According to international GOST 9561-2016, hollow core slabs are distinguished by new transportation rules, control methods and general technical requirements. It is these norms that are now fundamental in the development of products and technical conditions, as well as in the preparation of standard design documentation.
It is interesting! The norms governing the production process of the 1.141-1 series hollow core slabs were developed by the USSR State Construction Committee on May 28, 1970 and to this day remain relevant in Russia.
Hollow reinforced concrete floor slabs are widely used in the construction of prefabricated buildings. Depending on the characteristics of production, products are divided into hollow-core and non-formwork slabs. The width of a hollow core slab has several meanings:
- 1m;
- 1.2 m;
- 1.5 m;
- 1.8 m.
The thickness of the hollow core slab is mostly unchanged at 22 cm, although 16 or 30 cm thick options can also be found.The length may vary depending on the manufacturing method, which does not affect the reliability of the building material. Basically, length indicators are in the range from 1.7 to 9 m.
Table of sizes and prices of hollow core slabs:
Parameters: length, width, height, m | Minimum price, rubles / piece. | Maximum price, rub / piece |
1780x990x220 | 2780 | 3469 |
2080x990x220 | 3483 | 3766 |
2580x990x220 | 3840 | 4356 |
3180x1490x220 | 5601 | 7766 |
3780x1190x220 | 5619 | 7493 |
5380x990x220 | 6886 | 7938 |
7180x1490x220 | 12843 | 18686 |
A separate group can be divided into lightweight interfloor slabs, which are marked with PNO. The main difference from standard slabs is the height, which is not 22, but 16 cm.
Table of sizes, prices of lightweight floor slabs:
Size of hollow floor slabs: length, width, height, m | Price, rub / piece |
1580x990x160 | 2173 |
1780x1190x160 | 2584 |
1780x1490x160 | 3294 |
2080x1490x160 | 3812 |
2980x990x160 | 3257 |
The main types of markings: what data can be found from the name
The standard marking of floor slabs, regardless of the type, has the following meanings:
- letters indicate the type of product and design features;
- numbers indicate length and width, height is considered a relatively constant value and is not used in marking;
- bearing capacity, where the unit of value corresponds to the withstand load of 100 kg / m²;
- the class of reinforcement used is usually indicated at the very end.
Sometimes additional values are found in the marking, such as resistance to aggressive environments, seismic impact, temperature extremes. You can also find a value indicating the amount of voids in the panels. For example, we can consider the decoding of the marking of the hollow-core product PK 23.15-8:
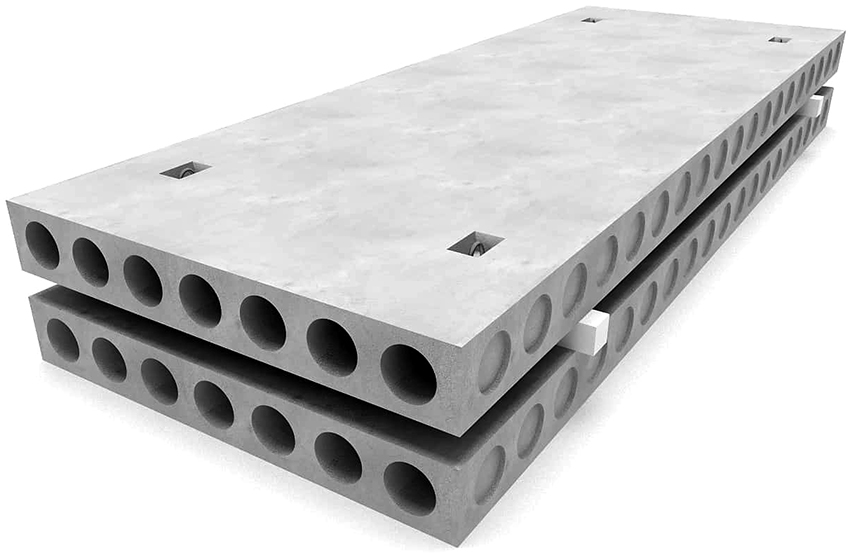
From the marking, you can find out the type of board, dimensions, bearing capacities and class of application
- The abbreviation PC means that the slab was made by pouring into the finished formwork, and the slab has round cavities.
- 23 - denotes the length in decimetres, which is most often rounded up.
- 15 - rounded slab width 14.9 dm.
- 8 is a value indicating the bearing capacity of a hollow block, which corresponds to 800 kg / m².
The designation of the overlap PB 72.15-12.5 is deciphered in a similar way:
- PB - these letters are used to mark the product made by means of a non-formwork method. The abbreviation also means that it is a plate with cylindrical cavities.
- 72 is a rounded length of 71.8 in.
- 15 is the width parameter.
- 12.5 is a coefficient indicating the bearing capacity of a product, which corresponds to a value of 1250 kg / m².
What are hollow core slabs and how are they made?
In the production of hollow-core floor slabs of the circular-hollow type, formwork is used that limit the slab along a special contour. For this reason, the length of the finished slabs varies from 1.8 to 7.2 m, the size changes in increments of 30 cm. The production process is as follows:
- The concrete mortar is poured into a stationary metal formwork with fixed reinforcement and a metal mesh.
- The concrete mix is well rammed, after which the finished slabs can be processed in hydrothermal boxes.
- After complete solidification, the finished panel is removed from the formwork using the pre-mounted lugs.
Formwork slabs are produced without the use of formwork with continuous casting of concrete. The final shape of the product is given by a molding machine, as a result of which a long plate is obtained, which is then cut to the required dimensions, while the accuracy can reach several centimeters. In this case, the maximum length of floor slabs reaches 9 m, the height remains unchanged at 22 cm. The main advantage of non-formwork slabs is that when trimming the edge, you can give any shape that matches the architectural idea of the building.
Most often on sale there are slabs made according to the formwork principle, because to create them, you do not need to use additional equipment. This type of slab is produced in almost all precast factories.
For the convenience of transportation and construction, all products are equipped with mounting loops. To make the slabs more reliable, they are additionally reinforced. Wire rope or other high-strength material is used as reinforcement. It is the use of reinforcement that increases the safety margin of products and allows the plates to withstand increased loads during operation.
For production, concrete of the W4 brand is used, which has a strength index of A22.5, and the bearing strength of the floors themselves is in the range of 2000-2400 kg / m3. Most often, the following types of concrete are used for the manufacture of panels:
- silicate;
- light;
- heavy.
In general, hollow-core floor slabs consist of the following materials:
- Concrete. Products are made on the basis of Portland cement grade M300 and higher. It is on the quality of the concrete used that the strength indicators of finished products depend.
- Steel reinforcement. The use of reinforcing material belonging to the A3 and A4 classes increases the load properties of slabs used as interfloor floors.
Hollow core slab: design features
The main advantage of using hollow-core floor slabs that meet the GOST standard is a significant simplification of the construction process and laying of utilities. In addition, the peculiarities of the production of panels provide the finished building with increased thermal insulation of interfloor ceilings. Also, the slabs guarantee improved sound insulation and prevent the penetration of external noise into the room. The main design features include the following points:
- Correct geometric shape. Finished products are distinguished by the shape of a parallelepiped, which has flat face surfaces.
- The presence of through holes on the front sides. The presence of internal voids increases the sound and thermal insulation properties, and also reduces the final weight of the floor slab.
- The correct shape of the internal cavities. The configuration of the longitudinal section of the cavities is in the form of a regular circle or oval.
- Dimensions of hollow floor slabs. In general, the length, thickness and width of the slabs, as well as the diameter of the internal section of the holes, depend on the manufacturer, but are mainly regulated by GOST standards.
- Number of internal holes. According to GOST, hollow core slabs have from 5 to 9 through holes.
Interesting information! It is the presence of voids inside the floor slabs that provides the products with high performance properties. In contrast to solid panels, the weight of the hollow core slab is significantly lower, therefore, the foundation will be less affected. At the same time, hollow slabs are not inferior to solid panels either in sound insulation or in thermal insulation properties.
The main advantages of using hollow floor panels
The main advantages of a hollow slab are:
- Reduced weight. With the same dimensions of the hollow core slab and the solid panel, the weight of the former will be less. The presence of voids does not affect the decrease in the safety factor, but at the same time hollow-core products load the foundation base of the building less.
- More affordable cost. The price of hollow core slabs is significantly lower than the cost of monolithic panels, because a smaller volume of concrete is used in the production process, which allows to reduce production costs.
- Improved sound and heat insulation properties.Due to the presence of voids, an air gap is formed, which is located inside the concrete mass and provides high performance properties.
- Reduced construction time. Installation work using any size of hollow core slabs is carried out in a rather short time, especially when compared with the construction of a monolithic reinforced concrete structure using formwork.
- Large assortment of floor slabs. Manufacturers have a decent size range of products, where products differ in parameters and characteristics. A large selection of standard sizes allows you to choose different slabs for the construction of complex structures.
Useful advice! Only products manufactured in an industrial environment are capable of meeting the requirements of current standards. Plates made in artisanal conditions by small enterprises will have only small standard dimensions.
The main positive and negative aspects of using plates
Other advantages of different sizes of hollow-core slabs:
- Internal through holes can be used for laying all kinds of communications and you do not have to prepare special grooves for them.
- Increased resistance of reinforced concrete products to fluctuations in humidity and ambient temperature.
- The ability to withstand vibration loads, which makes it possible to use slabs for the construction of buildings in regions with increased seismic activity. Subject to construction standards, the building can withstand shocks with an amplitude of 8-9 points.
- The smooth surface of the panels facilitates interior finishing work after construction is completed.
- Minimal susceptibility to shrinkage of hollow-core products.
- Increased resistance of concrete to corrosion processes.
In addition to the listed advantages, builders also highlight the fact that when using hollow floor slabs, there is no need to install additional support posts. Despite such a number of advantages, the plates also have some negative sides.
So, the large weight of the concrete slab leads to the fact that it will be necessary to additionally use lifting equipment in construction. Due to the fact that it is necessary to order a manipulator, firstly, it is necessary to provide it with a sufficient construction site, and secondly, an item of additional costs will need to be included in the estimate.
Related article:
Profile pipe: dimensions, production conditions and costing
Dimensions according to GOST, types and format of the issue. Technologies for the production of rolled pipes. Profile standard of measured and unmeasured length.
In addition, before starting construction, it will be necessary to calculate the bearing capacity of the hollow core slabs and estimate the possible maximum load. In this case, it is imperative to take into account the magnitude of the impact of both a static and dynamic nature, and also calculate the load capacity of the walls.
Important! Before forming overlappings from hollow panels, it is first required to concrete the armored belt located along the contour of the box. To prevent freezing of the slab, from the inside, the holes in the end corners are sealed with insulation and cement.
Types of loads for which floor slabs are designed
According to the standard, the value of the bearing capacity of the product is 800 kg / m², but there are also options designed for an increased load in the range of 1200-1600 kg / m². It should be borne in mind that the cost of this type of hollow core slabs will be higher. Basically, panels are subjected to two types of loads:
- static;
- dynamic.
Static load is the cumulative effect on the slab from the floor covering together with the screed mass. This also includes the mass of interior walls, installed furniture - all this makes up the total pressure that is applied to the product from above. Below there is an additional load in the form of ceiling lights, plasterboard structures, fixed cornices and all other attachments that use the ceiling during their installation.
As for the dynamic loads, they arise as a result of the movement of all residents. In addition, the installed sports simulators, as well as sliding partitions, which are mounted on the floor or on the ceiling, create dynamic load.
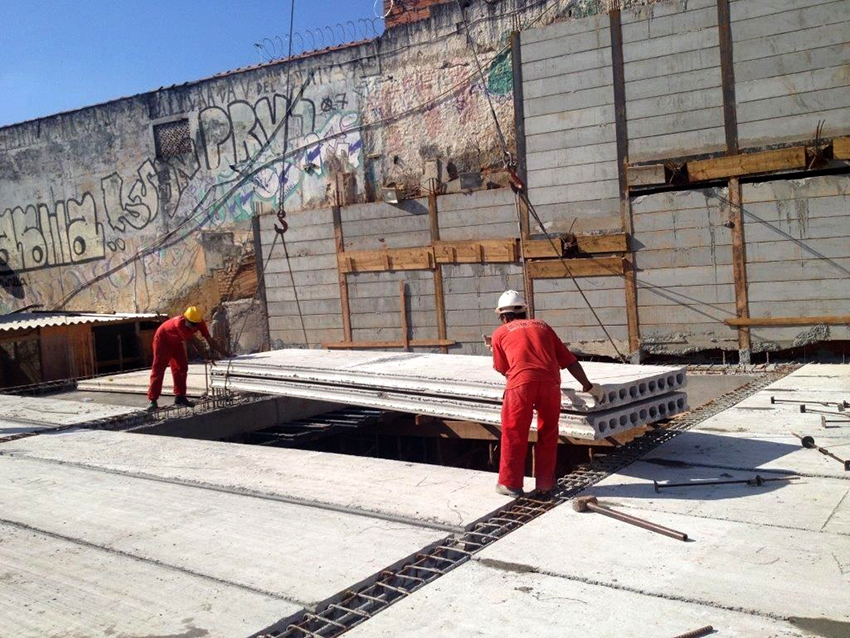
800 kg / m² - standard bearing capacity floor slabs
A complex load is distinguished into a separate category, which, for example, can be attributed to the pressure exerted by the bathroom, which changes depending on the filling of the bowl, the presence or absence of a person in it. If the bathroom is installed on legs, then each of the supports will create local pressure on the stove.
How to find out the maximum load on a hollow core slab
In order to calculate the pressure during construction for which a reinforced concrete base with cavities is designed, you need to perform the following actions:
- Draw a detailed construction plan, taking into account the number of supports that, after completion of the work, will exert a load on the base plate. Mark how they will be located.
- Approximately estimate the total mass of elements exerting pressure on the floor.
- Divide the calculated value by the number of precast panels.
After calculating the maximum planned load on the slab, you should choose the type of product most suitable for the characteristics. When calculating, do not forget that the slab's own mass is also taken into account. As for the calculation algorithm for the support structure marked PK 23.15-8 with a bearing capacity of 800 kg, which differs in size 1.49x2.29 m and a total weight of 1180 kg, it will look like this:
- To find out the area of the base, you need to multiply the length by the width: 1.49x2.29 = 3.41 m².
- To calculate the load on the square of the base, the total mass is divided by the area of the 1180 slab: 3.41 = 346 kg / m².
- Then, the resulting value 800-346 = 454 kg is subtracted from the bearing capacity.
The resulting indicator is the maximum mass for which the slab is designed taking into account its own weight. It is customary to take a value equal to 250 kg for the total mass of all objects acting on the plate from above per m². Thus, 454-250 = 204 kg - it is this weight that can be considered a margin of safety per m² of panel area.
Interesting information! Most of the reinforced concrete products have a bearing capacity of 800 kg / m², which is considered optimal for residential premises.
Floor slab weight and other important product parameters
According to GOST, the dimensions of hollow floor slabs must be within the following values specified in the table:
Options | Minimum value | Maximum rate |
Length, m | 1,68 | 12 |
Floor slab width, m | 0,98 | 1,48 |
Thickness, cm | 16 | 30 |
Diameter of voids, cm | 11,4 | 15 |
Concrete grade | M200-M400 | |
Weight, kg | 750 | 4820 |
Bearing capacity, kg / m2 | 800 | 1200 |
If you order products for individual production, then all indicators may vary depending on the requirements of the buyer. Changing the parameters should in no way affect the reliability or manufacturing technology. Despite the fact that the thickness of the slabs varies, in most finished products it is 22 cm.
Weight is considered a particularly important criterion, all products manufactured at Russian factories differ in indicators from 750 to 4820 kg. The weight of the product is important to consider, because, based on the value, the method of installing the panels during construction is determined. Usually, on a small construction site, cranes with a lifting capacity of up to 5000 kg are used.If the stove is heavier it can lead to serious problems.
For example, a concrete slab with a volume of 2.91 m³ marked PK 89-15.8 has a length of 8.88 m, a width of 1.49 m and a standard height of 22 cm. A product with such parameters differs in weight 4150 kg, in this case, use a crane with a lifting capacity of up to 5 tons can be dangerous. It should be noted that in some cases the weight of plates with the same marking is different, but usually the difference does not exceed several kilograms, so it does not play a significant role in the calculations. More often the weight changes due to wetting of one of the products.
Weight table of hollow core slabs depending on dimensions:
Size: length, width, height, m | Volume, m³ | Weight, t |
1680x1190x220 | 0,44 | 0,61 |
1980x1190x220 | 0,54 | 0,76 |
2380x1190x220 | 0,62 | 0,905 |
2680x990x220 | 0,58 | 0,83 |
1780x1190x160 | 0,34 | 0,463 |
2080x1490x160 | 0,5 | 0,686 |
5780x990x220 | 1,26 | 1,71 |
Reinforced concrete hollow ceilings are widely used in the construction of multi-storey buildings, both private and public. The panels gained their distribution due to the high performance characteristics, which were appreciated by both users and professional builders. To speed up construction, the main thing is to choose the right size, weight and type of slab, while not forgetting to take into account the bearing capacity of the products. As a result of construction in compliance with the rules and technologies, when hollow floors are used, a high-quality and stable building is obtained.