Concrete is the leading material used in the creation of various projects. Despite the fact that the building material is strong and durable, there are still negative factors that reduce the bearing capacity. This includes changes in humidity and temperature, exposure to ultraviolet radiation, shock and vibration. Ironing of concrete is a process that can prevent premature destruction of a structure by improving its qualities.
Content [Hide]
- 1 Why is it needed and what is the technology of ironing concrete surfaces
- 2 Where is the ironing of cement coatings used and what materials are needed to carry it out
- 3 How is the ironing of the concrete surface carried out
- 4 Dry ironing of concrete: stages and features of implementation
- 5 Wet ironing technology for cement coatings
- 6 Features of the use of polymer impregnations for concrete strengthening
- 7 What are and what are the topping mixtures
- 8 Tips and tricks for DIY concrete ironing
Why is it needed and what is the technology of ironing concrete surfaces
During operation, the hardened concrete is constantly subjected to various kinds of dynamic and mechanical loads. The ability to withstand negative factors will depend on the initial consistency of the concrete solution and its density. In order to improve the characteristics of the mixture, first of all, it is recommended to carry out the following activities:
- use sand of various fractions;
- correctly select the optimal ratio of cement, water, plasticizers and fillers.
No matter how competently the concrete is laid, there are still pores or microcracks, which become the gates for moisture penetration. This is especially dangerous in a situation where there is a constant temperature difference (from plus to minus and vice versa). The smallest ice crystals that form inside the voids are able to expand them even in a short period, which will lead to the fact that the concrete begins to rapidly lose strength and collapse.
In addition, moisture that has penetrated inside can negatively affect the reinforcing elements located inside reinforced concrete structures. Chemically active elements that can penetrate into the structure along with precipitation also have a negative effect on concrete.
Important information! Despite the fact that concrete is considered one of the most durable building materials, it still has a certain shelf life.Considering that it is on reinforced concrete structures that the strongest and most responsible impact is exerted, one must be prepared for the fact that, without performing additional measures, the surfaces may begin to crumble.
Closing cracks and small pores by ironing the surface is considered a proven and effective way to combat such phenomena. The procedure is carried out at the stage of building construction and when carrying out interior finishing activities. Ironing itself is a technological process aimed at increasing the strength of monolithic structures by applying special compositions to the surface that have high adhesion to the upper layers.
Where is the ironing of cement coatings used and what materials are needed to carry it out
The procedure is also important to apply when performing interior finishing work, because even the process of applying plaster is accompanied by the penetration of moisture into microvoids, which leads to the destruction of monolithic parts. Under mechanical action on the floor surface in the room, cracks appear, which eventually lead to the beginning of the crumbling process, which can be dealt with by ironing the floor screed with cement. It is important to perform treatment with a special compound immediately after pouring, because this is how it will turn out to maximize the service life.
During construction, the blind area is ironed, which makes it possible to make the foundation stronger and delay the implementation of repair measures. In fact, the main goal of the process is to increase the strength of the monolith, for which various components are used, including:
- dry mixes based on high grade cement;
- liquid or colloidal solutions with the addition of additives - most often it is liquid glass;
- materials with a high content of special polymers.
Interesting fact! Contrary to the name, in the process of ironing a concrete screed, neither iron nor other materials with this element are used in the composition. The name only indicates the fact that surface hardening occurs, which is compared with the positive characteristics of iron.
The advantage is that you can do the work yourself, for this you just need to comply with the technology and all the requirements of the manufacturer of the composition. Even the slightest non-observance of the rules will lead to a violation of the composition, and the concrete will not meet the necessary requirements. If we talk about the process as a whole, then the following functions are assigned to it:
- improvement of waterproofing;
- increasing the resistance of the surface to loads;
- formation of a reliable layer that prevents abrasion;
- protection against crumbling, delamination and the formation of pores and cracks;
- quick preparation of surfaces for use.
How is the ironing of the concrete surface carried out
After the formation of a concrete layer under the influence of gravitational forces during hardening, heavy fillers slowly settle, which leads to the fact that the density of the upper layer decreases. This process has an extremely negative effect on the strength of the structure as a whole, so it should be prevented.
Concrete is strengthened using a special technology, which includes several mandatory manipulations:
- thorough cleaning of the treated surface from dirt;
- preparation of the composition (subject to all requirements and recommendations given by the manufacturer);
- applying the finished solution to the surface.
After carrying out the listed activities, it is required to give the concrete some time so that it completely solidifies. There is no need to rush here, because the strength of the finished surface will depend on this.Reinforcement of concrete surfaces can be done in two ways:
- Dry. A dry cement mixture is used as an adhesive layer, after which the surface is well leveled.
- Wet. For strengthening, a liquid composition based on cement, colloidal mass or polymers is prepared.
Helpful information! If the concrete is ironed by hand, the proportions of the composition should be maintained in accordance with the instructions on the package. It is impossible to change the ratio recommended by the manufacturer on your own, because it is quite possible to achieve the opposite effect and waste a large amount of material.
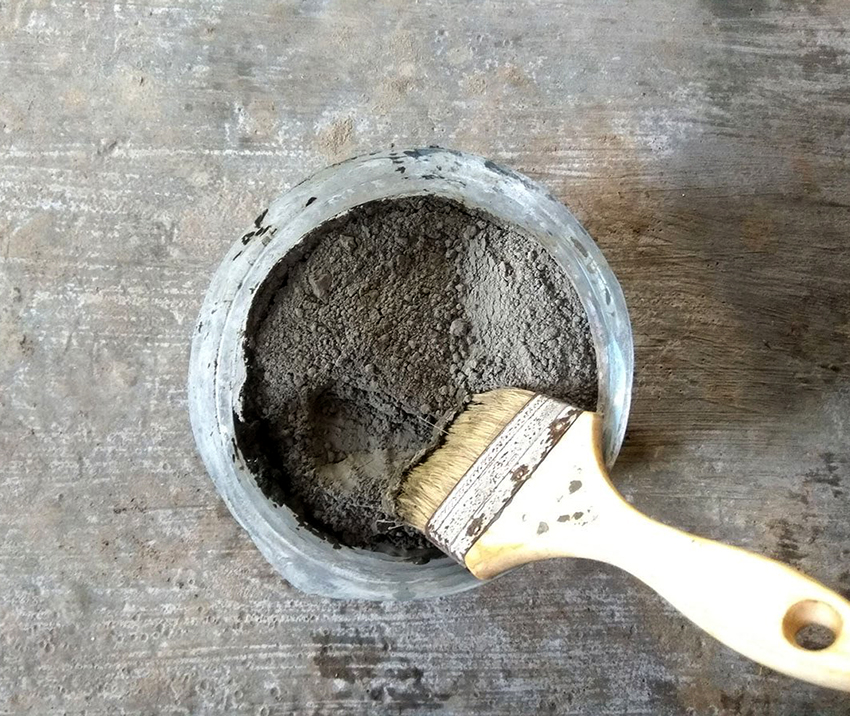
When preparing the composition, it is necessary to strictly adhere to the manufacturer's recommendations.
Dry ironing of concrete: stages and features of implementation
Dry ironing of concrete with cement is considered the simplest and cheapest option. This method is carried out mainly with the aim of strengthening horizontal surfaces, because the composition simply cannot hold on to a vertical wall. It is this drawback that is considered the most significant, because it reduces the scope and does not provide an opportunity to strengthen vulnerable wall surfaces. For work, both pure Portland cement and a mixture of other materials are suitable.
Reinforcement of a concrete floor can increase the strength of the surface by increasing the amount of cement in the surface layer of concrete. The negative side of use is considered to be low adhesion. The cement mixture does not sufficiently saturate the concrete and does not penetrate to the required depth, which may cause the top layer to peel off over time.
Important! In order for the screed to be ironed with cement to give the desired result, high grade cement should be used for the preparation of the mixture, and multi-component mixtures will provide the best adhesion.
Dry ironing of a floor screed or other horizontal surface should be carried out after the concrete has set, but the moisture on the surface will not completely evaporate. In most cases, experts recommend waiting 6-8 hours. After this time, a dry cement-based mixture is prepared with the addition of fine, clean, dry sand. In general, the technology of cementing concrete surfaces with cement involves the following stages:
- High-quality cement is poured onto the practically frozen concrete base. In this case, the thickness of the layer should not be less than 3 mm.
- To improve the efficiency, it is recommended to sift the cement through a sieve. Consumption is approximately 5 kg per m² of surface.
- After falling asleep, you need to wait for the cement layer to completely absorb all moisture from the screed surface. The readiness of the work is indicated by the mushy consistency of the mixture.
- Use a trowel or spatula to rub the cement into the concrete. This should be done until the top layer is completely dry and dark gray.
Operation is possible within a day after the work on ironing the floor or other surfaces, but it is better to wait 4-7 days. This period will be enough for the surface to reach its maximum strength.
Ironing the screed will be more effective if you rub a cement mixture with the addition of other components into the surface:
- quartz sand;
- liquid glass;
- sodium aluminate;
- basalt;
- polymer fibers.
Mixing these ingredients not only strengthens the surface better, but also shortens the time it takes to absorb excess moisture. It is especially important to use improved mixtures when treating floors in wet rooms, for example, in a bathroom, kitchen, bathhouse or sauna. The use of sodium aluminate not only improves the moisture-repellent properties of the floor, but also significantly reduces the amount of dust that forms and accumulates on the surface.
Wet ironing technology for cement coatings
The wet ironing method is considered universal, because it can be successfully used for processing both horizontal and vertical surfaces. At the same time, they use not only the factory composition for ironing concrete (in compliance with the supplier's instructions), but also the mixture prepared independently.
Conducting wet cementing of concrete surfaces requires preliminary preparation of the solution. It will also require Portland cement or a mortar of fine, clean sand, cement and water in a 1: 1 ratio. The dry components are mixed in a container until smooth, and then water is gradually added and, using a mixer nozzle from a perforator, brought to readiness.
The finished mixture should resemble thick sour cream in appearance. If it is planned to process vertical surfaces, the consistency should be such that the applied layer (3-5 mm) does not drain from the walls and adheres tightly.
Checked! To increase the plasticity of the cement mortar, experienced owners recommend adding 10% milk of lime. When ironing plaster, it is permissible to include various dyes and dry pigments in the solution.
You can get the most smooth and perfectly flat surface by adding liquid glass, which will also increase the surface's resistance to moisture. It is better to carry out work on the ironing of cement or concrete a week after pouring the concrete solution, until it fully sets and the water has not completely evaporated.
Wet ironing of concrete surfaces with cement: how to carry out correctly, tools
Before starting work, clean the surface. After applying a layer of the required thickness, the surface is gently smoothed and then polished. To give an attractive appearance, a polyurethane coating or paint for concrete is used. After the concrete is wet-ironed, the surface reaches its maximum strength after 3-5 days. At the same time, during this period, it is recommended to moisten the surface using a spray gun or spray gun.
Among the disadvantages is the possible separation of the formation due to insufficient adhesion to the base. To avoid such problems, it is recommended to use a primer to strengthen concrete and increase the adhesion strength of the compounds.
For surface polishing, polishing trowels, graters and other mechanical methods are often used. If we are talking about a large area that needs to be processed, such methods will be expensive not only physically, but also in time. Therefore, in such cases, the best way out of the situation is the use of trowels, in a large assortment presented on the shelves of construction stores. Many recommend purchasing a used tool in order to save money, but it should be carefully inspected and checked before purchasing.
Cars have their drawbacks too. So, with their help it is convenient to process flat surfaces, but it will not work to process corners or embossed areas of concrete. In this case, only manual work is suitable.
Related article:
Liquid glass for concrete: versatility of silicate mixture
The composition of the solution, scope, rules of use. Composing proportions. The cost of the mixture and customer reviews.
Features of the use of polymer impregnations for concrete strengthening
Polyurethane compounds for iron are in greatest demand among consumers, because they are considered an effective way to increase the strength of concrete surfaces. It is easy to do it yourself and still get an excellent result.Colloidal mixtures are characterized by the presence of liquid glass and polyurethane in the composition.
Important information! Strengthening with liquid glass has a large number of advantages, where fast drying of the surface and smoothness can be considered the main ones. The negative aspects include the fact that during wet cleaning, the glue is gradually washed out from the surface, which leads to a decrease in strength.
In general, the polymer is considered a deep penetration impregnation to strengthen concrete, because it is embedded 5 mm into the pore depth. The compositional characteristics allow polyurethane-based solutions to be used even under extreme environmental conditions, for example, at constantly low temperatures.
To obtain a protective layer, concrete hardening liquid is applied using a spray gun. After 1-2 hours after application, the concrete is rubbed with a brush. In addition to the fact that the solution can be used in construction and repairs, it is also suitable for restoration work, when the walls of an old building are strengthened to prevent its destruction.
As in previous cases, before carrying out ironing, the surfaces should be thoroughly cleaned of dust and other contaminants, and then treated with a primer. It is better to repeat the process of applying the primer 2-3 times. In this case, the material should be distinguished by its ability to penetrate deep into the concrete.
To improve the efficiency of work, before buying, you need to clarify the permissible temperature range of use, as well as other application rules. Also available for purchase are products intended for dry ironing, used on the principle of dry cement compositions. But due to their low efficiency, they have not become widespread.

Polymer impregnations are able to reliably strengthen concrete due to the ability of deep penetration
What are and what are the topping mixtures
According to the degree of strength, topping compositions are divided into groups:
- quartz - they have an average level of strength;
- corundum - reliable mixtures;
- metallized - heavy-duty.
Quartz topping is considered the most popular because, as already noted, quartz is suitable for surfaces that are in a room with high humidity and are intended for continuous use.
Corundum is considered one of the hardest stones, and additives based on this material not only increase the strength characteristics of concrete, but also improve its ability to withstand significant mechanical loads. Corundum-based mortars are excellent for strengthening concrete surfaces at gas stations, service stations, parking lots, in underground and surface parking lots.
Topping with metal shavings in the composition is used to improve the strength properties of reinforced surfaces in factories and industrial enterprises. Due to the fact that the material is subject to corrosion processes, it is not recommended to use it in social or residential buildings. The mixture is applied to the prepared surface 6-7 hours after pouring.
The composition is evenly distributed over the surface. After excess moisture is absorbed, the plane is smoothed out. Then the remnants of topping are applied again, after which the surface needs to be wiped again. After 3 hours, the surface is sanded and treated with curing - a special impregnation for concrete. Before final solidification, the surfaces are covered with a film. After 2-3 days, using a grinder, expansion joints are made, going deep into the surface of the slab, which are filled with polyurethane filler in order to completely seal.
Tips and tricks for DIY concrete ironing
The blind area is considered a multi-layer waterproofing protection of the house, therefore, it is in dire need of additional strengthening in order to increase the durability of the entire structure and protect the house. This is due to the fact that it is this part that first experiences the negative impact of natural forces.
Important! The duration of operation, the strength of the coating and the reliability of the future construction entirely depend on the quality of the building material, so you should not save on the purchase. In addition, it is necessary to give preference only to trusted brands.
It is recommended to strengthen the foundation formwork before pouring concrete, as well as to carry out measures to strengthen the already finished base. Ironing in this case is best done 2 weeks after the end of the main work. In this case, it is appropriate to apply any of the methods:
- with the dry method, the cement is hardened by means of plasticizers that strengthen the top layer;
- it is better to supplement the wet strengthening of the blind area with the help of liquid glass.
If the weather is hot, you should periodically moisten the surfaces with a spray bottle. The wet method is not recommended to be carried out earlier than 1.5-2 weeks after concreting. For greater reliability, you can additionally use a variety of toppings to improve adhesion to the concrete surface and enhance the bearing capacity. Important tips for ironing that may become relevant during work:
- It is possible to strengthen not only fresh, but also old concrete structures. For example, it is important to reinforce slopes in an old house with monolithic concrete, as a result of which it will be possible to increase the strength characteristics of the entire building.
- It is important to responsibly clean and prepare the surface. All fragments that do not adhere well, as well as elements of dust and dirt should be removed.
- When preparing the mixture, you need to pay attention to its appearance, because if the composition contains particles of different sizes, there is a possibility of uneven moisture absorption. This is hello to the complication of work and a decrease in the quality of the application.
- When buying a mixture, it is better to give preference to trusted manufacturers and not to purchase too cheap options. Otherwise, there is a chance of getting a dubious result of work.
- If the composition is prepared independently, it is imperative to observe the technology and the necessary proportions so as not to spoil the materials.
Having chosen a suitable method of ironing concrete, it will be possible to strengthen the screed, slopes, plastered walls, foundation, formwork, blind area and any other concrete or cement surface on our own. Despite the simplicity of execution, reinforcing compounds improve the strength characteristics of any surface and prevent premature failure.