The putty is intended for leveling surfaces before finishing work indoors. It can also be used as a topcoat. This type of material is present in the construction market in a huge variety. The article will help you figure out what the putty is: types of mixtures, their characteristics and features of application, as well as the nuances of choosing the right composition for certain types of work.
Content [Hide]
- 1 Putty: types of mixtures by purpose, their characteristics
- 2 How to choose the best finishing putty: types of compositions, their advantages and disadvantages
- 2.1 Advantages and disadvantages of dry wall putties
- 2.2 Advantages and disadvantages of ready-made finishing putties
- 2.3 Characteristics of gypsum finishing fillers, their advantages and disadvantages
- 2.4 Features of cement finishing putties, their pros and cons
- 2.5 The best finishing putties: consumer reviews
- 3 Review of the best finishing putties: polymer compositions
- 4 The technology of applying the finishing putty and its consumption
- 5 How to apply the finishing putty correctly: video
Putty: types of mixtures by purpose, their characteristics
The putty hides flaws on the walls and ceilings well, masks the seams in those areas where the cracks were repaired with plaster. The material is presented on the market in a huge range. Each variety is designed for a specific type of work.
There are several types of putties for interior work:
- starting;
- finishing;
- universal.
Starting mixtures are used at the initial stage of repair work. They allow you to align the relief of ceilings and walls. The material completely masks traces of self-tapping screws, eliminates damage - chips and cracks. The leveling fillers contain large particles. Thanks to this, the coating is strong and durable. Starter mixes can be applied in thick layers.
The leveling putty dries quickly and is almost impossible to sand. The surface treated with such a mixture becomes rough. Most often, starters are used to level brick and concrete walls. They even allow you to abandon the application of a layer of finishing putty. However, in this case, the surface will be unsuitable for painting or wallpapering. Alternatively, wall panels can be used.
Note! Starter fillers are not suitable for eliminating deformations larger than 5-7 mm.
Universal compounds can be used both for leveling and for creating a finishing layer. This type of mixture is suitable for all surfaces. It should be noted that the cost of a universal compound is higher than the price of a finishing putty.
The use of universal formulations has its advantages:
- the coating turns out to be even and smooth;
- damages on the walls are well masked;
- the treated surface is completely ready for any type of finish;
- the coating has a large margin of safety.
Such a coating is easy to sand. However, despite all the advantages, the combination of starting and finishing mixtures still gives a better result than the universal putty.
In addition, the specialized mixture "Seam" is considered separately. Craftsmen use it for finishing plasterboard to hide the joints between the sheets. This type of mixture is only suitable for minor repairs.
How to choose the best finishing putty: types of compositions, their advantages and disadvantages
Finishing compounds are applied in a thin layer. This material prepares the surface for further finishing. Treated walls can be safely painted, plastering or wallpapering. Finishing mixtures are composed of fine-grained particles. Due to their plasticity, such putties are able to create an absolutely smooth surface. They have a creamy consistency and can only be used on flat walls. The maximum permissible layer thickness is 5 mm.
The material is sold as ready-to-use formulations or dry powders, which must be diluted with water before use. Each of them has its own advantages and disadvantages. On a basic basis, the compositions are gypsum and cement. According to the type of binder component, dispersion, polymer putties and oil-glue are distinguished.
In addition, chakril is found on sale. This finishing white putty has a highly specialized focus. It is used for leveling plastered surfaces and skirting boards. The composition is suitable for preparing ceilings for whitewashing and walls for tiling.
Note! When choosing a putty, it is imperative to take into account the material of the surface that will be leveled, as well as the operating conditions of the room (temperature and humidity level).
A certain type of putty is suitable for each type of work:
- walls - for offices, bedrooms, living rooms, hallways and children's rooms, it is preferable to use a plaster-based mixture. In the kitchen and bathroom, where the level of humidity is increased, it is advisable to use acrylic putties or cement-based compounds;
- ceiling - both gypsum and acrylic mixtures are allowed. The second option is more suitable for these purposes, since it provides a smoother and more even coating;
- wooden surfaces - only acrylic compounds are used for processing;
- drywall - acrylic putty is most often used. If the air in the room is dry, the use of gypsum mixtures is allowed;
- outdoor work, facade decoration - it is better to take acrylic mixtures and cement-based compounds, which are designed for outdoor conditions;
- surface preparation before painting - polymer and gypsum putties are suitable to create an even and beautiful coating.
Advantages and disadvantages of dry wall putties
Manufacturers of dry putties pack the material in bags weighing from 5 to 25 kg. The shelf life of the powder is 12 months. Before starting work, the required amount of the mixture is calculated. Diluted compounds dry out quickly and lose their properties, therefore one portion is prepared for surface treatment, and the remaining material is stored dry.
The advantages of dry powders:
- convenient packing;
- to prepare the composition, no special knowledge and experience is required; this can be done independently;
- the master can select the consistency of the mixture himself and adjust it;
- long shelf life without temperature restrictions, provided that the package is closed;
- low cost.
The disadvantages of dry material are mainly related to the application technology and storage conditions of the powder:
- applying self-prepared formulations requires certain skills. In the absence of practical experience, there is a high probability of obtaining a short-lived coating with a low level of quality;
- if the technology for preparing the mixture is violated, the material may lose its properties and it will not be possible to use it for its intended purpose;
- homemade formulations are susceptible to rapid drying. After this, the mixture is no longer suitable for use. For this reason, the calculation of proportions causes some difficulties for inexperienced craftsmen. In addition, the mixture must be applied immediately after dilution, which is not always convenient.
Important! It is not allowed to store dry putty in rooms with high humidity, and where water can get on the material. Under such conditions, the powder deteriorates and loses its properties.
Advantages and disadvantages of ready-made finishing putties
Ready-made compositions are polymeric (latex and acrylic) and dispersion. Manufacturers use plastic buckets as packaging for them. This type of putty is in high demand among consumers due to its convenience and simplicity. The ready-made mixtures contain special components. They provide a long shelf life for the material.
The advantages of ready-made formulations:
- the putty is plastic;
- even in open packaging, the shelf life of the material is very long;
- there is no need to calculate the proportions and mix the composition;
- simple application technology;
- wide range of applications (processing of wood, metal and plasterboard surfaces is possible);
- repair time is reduced.
The only drawback of ready-made mixtures is their high cost. Polymer putties are universal. They perform well on concrete, cement, polyurethane and plaster surfaces. They are environmentally friendly, safe for use. Forms an elastic coating. Water-dispersive compositions are suitable for processing concrete and brick, stone and aerated concrete walls. They go well with wood and other types of materials.
Characteristics of gypsum finishing fillers, their advantages and disadvantages
Gypsum-based putties are sold as dry, fine-grained powders. These materials contain special additives. In addition to soluble polymers, putties contain mineral fillers. Most often it is marble flour or quartz sand with a fine fraction. In the assortment of gypsum putties, there are both finishing and starting mixtures, and even universal ones. This type of material is used to mask the joints between drywall sheets and slabs.
Advantages of gypsum-based mixtures:
- environmental friendliness - can be used for surface treatment in residential premises;
- high adhesive properties - the material fits perfectly on all types of surfaces, providing good adhesion;
- excellent permeability - the coating does not interfere with the natural circulation of air, therefore, the likelihood of mold development is excluded;
- affordable cost;
- the material is easy to process - the surface can be sanded.
Important! The scope of application of gypsum compositions applies exclusively to interior finishing work. These mixtures cannot be used in high humidity conditions or outdoors.
Disadvantages of gypsum mixes:
- the mixture sets quickly - the speed of application of the composition must be high, which requires a certain amount of experience and skill;
- high hygroscopicity does not allow the use of putty for exterior decoration. Under the influence of moisture, the coating will collapse;
- it is not recommended to use gypsum mixtures on clean concrete. Before applying, its surface is treated with a special primer;
- short shelf life in an open package - after opening the package, the material must be used within a few days, otherwise it will absorb moisture from the air and become unsuitable for further use.
Features of cement finishing putties, their pros and cons
Cement-based putties are considered the most durable of all existing mixtures. They are suitable for interior and exterior work, as they are resistant to moisture, durable and not afraid of temperature extremes.
In addition to the main varieties, cement putties are:
- decorative;
- basement;
- front;
- heat insulating.
Cement is the main component of the putty, although gypsum, various polymers, lime may be present in its composition.
Advantages of cement compositions:
- simple application technology - the material hardens long enough that
- allows even a beginner to successfully cope with the application of putty and promptly correct mistakes;
- starting mixtures can be used on surfaces with large differences - from 5 to 15 mm;
- the coating is resistant to moisture, high and low temperatures, and other negative factors;
- affordable price;
- simple and clear instructions for preparing the mixture.
Related article:
GVL for flooring: the best way to make the surface perfectly flat
What are gypsum fiber boards, technical characteristics. Advantages disadvantages. Installation rules and technologies.
Cement-based putties are practically devoid of disadvantages. Experienced craftsmen note some inconveniences due to the long setting time, but for beginners this is rather an advantage. Unlike polymer and gypsum mixtures, cement compositions are more granular.
Note! Cement mixes can be used in unheated rooms. These include verandas, garages, summer kitchens or summer cottages for seasonal use, open balconies and cold-glazed loggias.
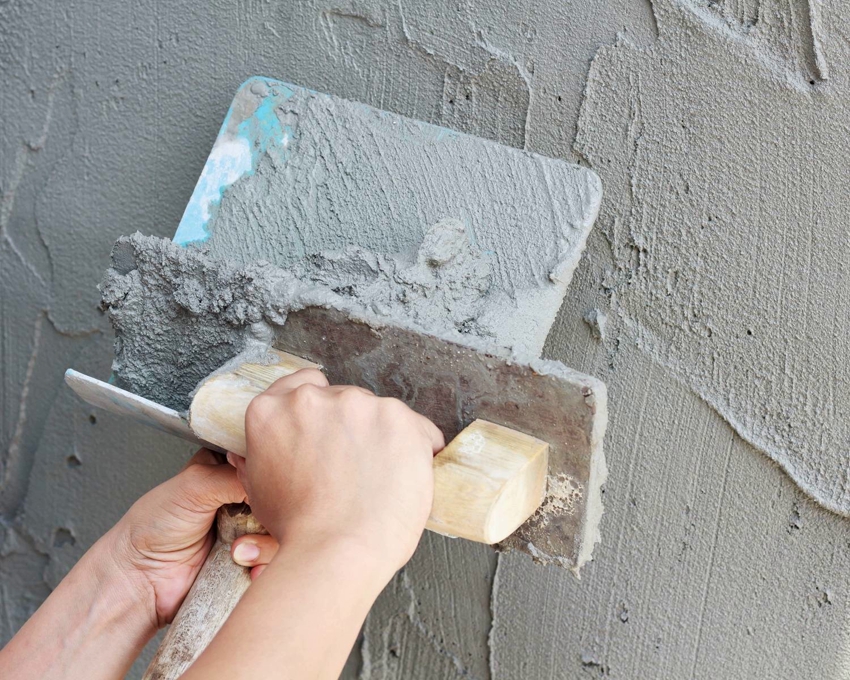
Cement putty hardens for a long time, which makes it possible to correct inaccuracies during application
The best finishing putties: consumer reviews
Having decided on the type of putty for indoor repair, it remains only to choose a high-quality and reliable manufacturer. Before going to the store, it is advisable to weigh all the pros and cons of the most popular brands and read customer reviews.
Many users share their opinions and personal experience of using putties on the forums:
“As an experienced craftsman, I am a fan of Knauf putties, I used polymer mixtures many times and the result was quite satisfactory. Recently I decided to align and update the ceilings in my country house. Usually for these purposes I use Shitrok, but at that moment it was not at hand. I decided to take the gypsum-based Rotband finishing putty and was very disappointed.
After application, the entire surface is covered with scratches and some streaks. This is despite the fact that this is not the first time I have done this! A lot of time and effort had to be spent on grinding. In the end he spat, went to town and bought Shitrok. I had to apply two layers to cover this mess. There are no complaints about Knauf's finishing polymer putties, but I won't touch Rotband again. Too grainy. Well not suitable for a topcoat! "
Evgeny Sidorov, Moscow
“My budgetary possibilities were only enough to buy Bolars polymer finishing putty. In the process of applying, it turned out that the composition dries very quickly, so it is advisable to mix it in small portions. The rest of the putty is very comfortable, plastic, it bridges cracks well. In general, I highly recommend it. "
Marina Fomicheva, St. Petersburg
“I never thought that cheap putties could give such a high quality result. Usually manufacturers shove a bunch of plaster or chalk. Naturally, the effect of such mixtures is not very good. But I took a chance and bought a polymer finishing putty Prospector. This time my instinct did not fail. The material is really high quality. At this price, the putty worked out 200%.
Finishing putty packing - 20 kg. After opening the package, I was a little confused by the grayish color of the powder. After dilution with water, the mixture turned white. The consistency is uniform, easy to apply, perfectly masks irregularities. The best investment is 350 rubles. in the entire history of my renovation ".
Igor Prigozhin, Tomsk
Review of the best finishing putties: polymer compositions
Polymer putties are made on the basis of acrylates, which are perfectly combined with other components in these mixtures. Thanks to this, the material is homogeneous. On most surfaces, the putty forms a dense, perfectly smooth coating.
Ready-made polymer putties have a wide range of applications. For outdoor work, there are facade types of mixtures. Both latex and acrylic compounds exhibit moisture resistance and are not subject to rapid wear. The coating surface is easy to sand. They fit well over wood, concrete and other surfaces covered with plaster. For interior work, acrylic mixtures are used.
Important! Acrylic compounds are afraid of low temperatures.
General characteristics of Shitrok finishing putties
The manufacturer offers three options for ready-to-use formulations at once. Danogips SuperFinish is a polymer mixture with high adhesion properties. The material is suitable for processing the following types of surfaces:
- drywall;
- fiberglass;
- walls covered with paint.
The product creates a perfectly smooth layer on the surface, but it is not suitable for repairing large damage and for sealing joints.
In the category of polymer mixtures, there is also a universal putty - Danogips ProSpray. The material is used to solve such problems:
- the creation of decorative finishes;
- alignment of joints on brick walls;
- sealing cracks and seams.
Danogips Fill & Finish Light is another finishing mixture that is suitable for leveling surfaces with minor imperfections. Creates a lamination effect. The mixture contains latex, so the coating is durable, moisture-resistant, not afraid of scratches.
General characteristics of finishing putties Vetonit
Polymer putties Vetonit are made from natural raw materials. All compounds are easy to apply and distribute well over the surface, increasing its soundproofing qualities. Differ in efficiency. High quality white limestone and finely ground marble are used as the basis for the production of Vetonit LR + finishing putty. In addition, polymer additives are mixed into the composition. The material is applied to clean, pre-leveled surfaces with a starting mixture.
Characteristic features of the material:
- small particles (up to 3 mm);
- drying time - 24 hours (at a temperature of 20 ° C);
- recommended coating thickness - 1-5 mm;
- consumption - 1.2 kg / m² (with a layer thickness of 1 mm);
- the shelf life of the prepared mixture is 24 hours (open), 48 hours (in a closed container);
- shelf life in dry form - 18 months.
Important! Before applying the Vetonit LR + finishing putty, the surface must be cleaned of small particles and debris and degreased.
The finishing polymer putty Vetonit JS contains finely ground marble chips and polymer glue. Suitable for leveling the surface for wallpapering and painting. Effectively copes with grouting and filling drywall. Processing of previously painted surfaces is allowed.
Material properties:
- high level of adhesion;
- forms an even and smooth coating;
- increased strength due to the presence of reinforcing microfibers;
- drying speed - from 3 to 24 hours.
The scope of application of the LR finishing putty extends to the treatment of walls and ceilings. It adheres well to concrete and plaster surfaces. The material is applied in one layer. The putty is not suitable for rooms with high humidity.
Characteristics of Volma polymer finishing putties
Volma Polyfin putty based on polymers has good covering ability, plasticity and increased whiteness.
Features of the composition:
- shelf life of the finished solution - 24 hours (open), 72 hours (in a closed container);
- layer thickness - up to 3 mm;
- intended for interior work in rooms with normal humidity levels (not recommended for use in kitchens and bathrooms);
- the optimum air temperature in the room for applying the mixture is from 5 to 30 ° C);
- the optimum moisture level for application is no more than 80%;
- it is recommended to use a stainless steel tool.
High quality and plasticity of Volma Polymix finishing putty allow using this material to create a snow-white base for any type of finish. Application of the composition can be carried out both manually and by machine. In consumer reviews, this mixture is noted as an easy-to-apply and practical putty.
Overview of polymer-based Hercules finishing putties
Putty Hercules-GT 53 is used to eliminate defects and finish leveling of surfaces covered with plaster. The composition is well combined with aerated and ordinary concrete, plasterboard, gypsum and gypsum fiber sheets. Before applying the mixture from the surface, it is imperative to remove stains and dirt, degrease it.
Helpful advice! If it is planned to apply Hercules polymer finishing putty on loose surfaces prone to crumbling, it is advisable to use a strengthening impregnation of the same brand. For highly absorbent and coarse-porous substrates, the manufacturer offers a stabilizing primer.
Hercules-GT 73 mixture is a polymer putty with a high margin of safety. Possesses frost-resistant and moisture-resistant properties. The permissible layer thickness varies between 0.1-5 mm. It can be used in rooms with high air humidity.
Features of Axton Polymer Finishing Putty
The putty is designed to create a high-quality leveling of ceilings and walls before finishing work. Designed for rooms with a humidity level within normal limits. The scope of application of the Axton polymer finishing putty (25 kg) extends to the sealing of joints between gypsum fiber and gypsum plasterboards. In addition, it can be used on mineral substrates and other surfaces that will be painted, pasted over with wallpaper and other decorative materials.
It is advisable to use a metal spatula to apply the mixture. The material is distributed in a uniform layer with a thickness of 0.1-2 mm. If the mixture is applied several times, then before each layer the previous one is thoroughly dried and treated with a primer. Drying time - 24 hours.
The technology of applying the finishing putty and its consumption
According to the technology, the putty is applied in at least two layers. First comes the starting one, then the finishing one. If the walls are in poor condition and covered with a lot of defects, the number of layers increases.
First you need to determine the required amount of material. The consumption rate of the finishing putty depends on the following factors:
- surface type;
- kind of mixture;
- layer thickness.
Consumption of epoxy putty for wood is 1.1 kg per 1 m². The indicator reflects the amount of material required to process the specified area with a layer thickness of 1 mm.
How to apply the finishing putty:
- The starting mixture is applied with a wide spatula from bottom to top. It is advisable to quickly and evenly distribute the material, without unnecessary strokes and irregularities. The layer should dry out.
- The finishing mixture is applied over a reinforcing mesh with cells up to 3 mm so as to completely cover it.
- After drying, the main layer of finishing putty is applied with a thickness of no more than 2 mm.
- Small inaccuracies on the coating are removed with fine-grain sandpaper without a fabric base.
If you act carefully and comply with the requirements of technology, you can level the walls and ceilings with putty yourself, saving on payment for the services of the master. In the absence of experience, it is advisable to use ready-made mixtures in order not to make a mistake with the recipe for the solution, and also to be able to eliminate the mistakes made in time.