Linoleum is rightfully considered the leader among floor coverings. The versatility of the material has been confirmed by the practice of using it for decades. They are attracted by the price and ease of installation. At the same time, a dilemma often arises regarding the need to lay a special material on the base. What is a linoleum underlay, what is its structure and when is it needed? This article will help you understand these issues.
Content [Hide]
- 1 Do I need a substrate for linoleum: functional features and material structure
- 2 In what cases is a linoleum substrate necessary, and when an excess
- 3 Installation of linoleum on different bases: types and requirements
- 4 Linoleum base: concrete floor underlay
- 5 What should be the substrate for linoleum on a wooden floor
- 6 How to lay linoleum on a wood floor: laying the backing
Do I need a substrate for linoleum: functional features and material structure
Linoleum backing is an additional building material that plays the role of an interlayer between the floor and linoleum. There has long been a debate among builders as to whether to use a substrate. Some are sure that it is desirable, and in some cases even necessary, others are adherents of the opinion that laying additional material is a waste of time and money.
In fact, both sides are right: in some cases, you cannot do without a backing, and in some, it will be an extra element. If you have a question about the need to use it, you must first familiarize yourself with the wide list of functions that the substrate performs:
- Reliable sound insulation. This feature is important in multi-storey buildings, as it prevents the penetration of noise from rooms located below.
- Additional thermal insulation. This function is relevant for apartments with cold floors, for example, those located on the ground floor and above non-residential premises that are not heated. It is the substrate that can become an excellent insulation.
- Leveling the surface. An additional layer excludes tight contact of the main floor material with the floor, levels pits, cracks, bumps, which helps to level the base and extend the life of the linoleum. After all, the presence of flaws on the floor entails rapid damage to the material.
Various technologies and raw materials are used in the production of substrates, in particular, natural and synthetic ones. The variety, advantages and disadvantages of its main types are described below. The name and structure of the natural substrate correspond to the material that was taken as a basis for the manufacture:
- jute;
- cork;
- linseed;
- wood fiber;
- combined.
Helpful advice! Now on the building materials market there is a wide range of multilayer linoleum with a special layer of different sound and heat insulating materials. Their use eliminates the need to lay additional material under the linoleum.
Jute, linen or cork backing for linoleum: a comparative characteristic
Jute. The basis of such a substrate is natural jute plant fiber. In order to prevent decay and fire, a special fire retardant is added to the raw material. Such a base is capable of absorbing and removing moisture. At the same time, the material itself does not get wet. Its main disadvantage is its high cost.
Cork. The raw material is crushed bark of a cork tree. Such a substrate is characterized by environmental friendliness (100%), because it excludes the use of synthetic substances. This is an excellent insulation for linoleum and a soundproofing layer. Along with the listed advantages, there are also disadvantages. The main one is the high price. In addition, the material has a low degree of rigidity, which leads to the punching of the coating under the influence of furniture and subsequently to its deformation.
Linseed. The production technology is a double piercing of linen fibers with needles. Treatment with special agents prevents the growth of bacteria and insects. The main advantage of the material is to provide free ventilation between the floor and the covering. Air circulation prevents moisture build-up and the spread of harmful bacteria and fungi.
Mixed and synthetic substrates: which is better for linoleum
Wood fiber. The main material is coniferous trees. A fairly new type of substrate with high sound and heat insulation qualities. The disadvantage is the same as with the cork base - the tendency to slip. In addition, coniferous resin, which protects wood from moisture and pests, has a strong, not very pleasant smell. This inconvenience "disappears" over time.
Combined underlay. It is made by mixing linen, jute and woolen fibers. Even the thinnest material of 2 mm has a high density - up to 700 g / m². This quality significantly improves the insulating properties. At the same time, such a substrate, like all natural ones, tends to slip, although to a lesser extent. It is considered to be the most practical base for any kind of flooring.
Foamed. It belongs to the category of synthetic, it is based on a porous polymer material. It has good noise and heat insulation qualities, as well as a relatively low cost. However, experts do not recommend using it under linoleum. Such a substrate is heavily punctured and soon loses its shape, all this negatively affects the state of the main coating. This material is better suited for laminate flooring.
Helpful advice! The best option for insulating and dry flooring is a combination of linen, jute and woolen fibers. It is a versatile substrate with a high degree of wear resistance and insulation.
In what cases is a linoleum substrate necessary, and when an excess
There are a number of significant arguments in favor of a linoleum underlay. In particular, its use is mandatory in such cases:
- a cold floor is the main precondition for laying an additional base before laying linoleum. The high degree of thermal insulation of the material serves as a protective barrier against cold, which comes from the basement or lower floors where non-residential premises are located. Therefore, experts do not recommend saving on the comfort and health of loved ones, neglecting the layer between the floor and linoleum. It is worth buying a good substrate, preferably from natural raw materials;
- uneven floor surface. Only an experienced craftsman can make a perfectly even screed, therefore, in order to avoid irregularities, it is better to use a substrate that will hide all the flaws;
- single layer linoleum. A coating without a base, although it is much cheaper, will not be able to provide the necessary thermal insulation; in such cases, a special base is required - a substrate.
You can do without an additional layer in a number of cases, given below:
- linoleum is laid on the old floor. In such a situation, the base should be as flat as possible, without flaws, otherwise it is better to dismantle the old material;
- multilayer linoleum with a foamed or jute base, which in its properties is in no way inferior to the substrate, greatly simplifies the installation process. This multilayer material consists of fiberglass, a layer impregnated with a PVC paste with a fabric backing, jute, polyvinyl chloride foam and polyester;
- Despite the fact that commercial homogeneous Tarkett linoleum is single-layer, it creates reliable insulation. This option is the best choice of linoleum in the hallway. Photos show different types of such material.
Installation of linoleum on different bases: types and requirements
Before you start laying linoleum, with or without a backing, you need to study the technical features of the base and prepare it carefully. Linoleum itself is a material that is quite flexible and elastic, so you need to take care of meeting a number of requirements in relation to the base:
- the surface must be firm and level. Exceptionally smooth drops from 2 to 7 mm are allowed, so a preliminary leveling procedure by pouring the floor may be necessary;
- the hardness of the sub-floor;
- the base must be perfectly dry and clean. If necessary, the surface is cleaned of old paint, getting rid of greasy and oil stains.
Helpful advice! When deciding on the advisability of using a substrate, it is necessary to take into account exactly where it is planned to lay the linoleum. In the corridor, you can do without it. Here you can use a single layer of commercial linoleum, the thickness of one layer of which will create the necessary insulation.
Compliance with the requirements for the preparation of the base helps to extend the life of the linoleum. As for the base itself, it is divided, depending on the material, into the following types:
- concrete;
- wooden floor;
- old coating;
- tile;
- plywood base covering concrete or wood floor (sheet materials such as plywood, fiberboard or OSB boards can be both the base for the floor and serve as a substrate for the floor covering).
Each type of base implies a special preparation and method of installing linoleum and a substrate for it.
Wood-based materials instead of a substrate: plywood on the floor under linoleum
Usually, plywood under linoleum is used as a substrate on a concrete base. This technology is used even more often on wooden floors. Other wood-based materials are also used - fiberboard and OSB boards. Their main advantage is to provide a perfectly flat surface. In addition, they guarantee the required rigidity of the base.The presence of plywood under the linoleum does not exclude the possibility of laying an additional layer of any soft substrate, which will give an additional heat and sound insulation effect.
Fiberboard is the thinnest and most affordable material in terms of price. Its thickness is up to 2 mm. For this reason, fiberboard is not suitable for laying on a very curved floor, since the substrate is quickly deformed, as a result of which defects are reflected on the linoleum.
OSB is an order of magnitude stronger and thicker (from 6 to 12 mm) of the previous material, therefore it is more suitable for a base under linoleum. Such plates will help level the floor, but before use, you need to clearly determine the required level. At the same time, the material quickly wears out under the influence of loads, part of the board peels off over time, which leads to the formation of defects.
Plywood, based on the characteristics of the coating products described above, is the optimal solid base material. Its layered structure does not allow bending, which contributes to an excellent leveling of the floor. The only drawback to plywood is that it costs an order of magnitude more than other alternative solid substrates.
Related article:
What is the best laminate substrate: types, properties and technical characteristics
The main criteria for choosing a material. How to do it yourself. Rating of the 5 best manufacturing firms.
All wood-based materials have a common disadvantage: they are vulnerable to moisture, so they should not be laid in the kitchen or bathroom. Under the influence of moisture, wood-based panels begin to rot, changing shape and volume. All this has a negative effect on the basic coverage. Fiberboard in general can, like paper, get wet when moisture gets in. Chipboards are susceptible to insect damage and are prone to fire. But with proper pre-processing, all these negative aspects can be leveled.
Helpful advice! In order to level the surface, it is better to take plywood with a thickness of at least 10 mm. On a flat screed, sheets with a thickness of 6 mm are suitable.
Linoleum base: concrete floor underlay
A concrete base is ideal for laying linoleum, provided it is first leveled. For this, special mixtures are used, screeds are made or the floating floor method is used. On a concrete floor, a substrate is most often used. The laying procedure provides for a certain sequence of work:
- Substrate preparation includes cleaning and leveling the surface. After applying the concrete screed, the floor must be completely dry. This may take up to 30 days;
- elimination of defects. After pouring the floor, small flaws sometimes form. The bumps can be knocked down or cut off, and the pits must be filled with a self-leveling mixture;
- waterproofing. After final drying, the surface is covered with a waterproofing layer. For this, a simple plastic wrap is suitable, covering the floor with a solid sheet. It is imperative to provide for an overlap on the walls of 3-4 cm;
- the installation of the leveling layer involves the laying of plywood or other wood-based materials. Plywood sheets are laid with a margin of 5 mm from the wall. Subsequently, the gap and seams between the plates are filled with sealant. Fix the material with small dowel-nails (5 mm) at a distance of 60 mm from each other. The fastening material should not protrude, and the dents are covered with putty;
- flooring of a roll substrate. The material is rolled out and laid end to end, without overlaps. The seams are glued with gray reinforced tape.
What should be the substrate for linoleum on a wooden floor
Wooden floors are very popular due to their environmental friendliness, practicality and thermal insulation characteristics.But such a floor wears out over time, it becomes necessary to update it. Faced with such a problem, the owners are wondering whether it is possible to lay linoleum on a wooden floor. It turns out that laying PVC material is the optimal solution for renovating a floor with a wooden base. In this case, dismantling of the floorboards is not required.
Naturally, the question arises of whether it is necessary to buy a substrate for linoleum. The answer should be sought in each specific case, taking into account the quality of the wooden base and the purpose for which it is planned to use this layer.
In particular, the underlay will help improve thermal insulation. Even in the coldest season, such a floor will retain heat as much as possible. It is not necessary to lay the substrate if you plan to install warm linoleum on a plywood base.
It is also advisable to use an additional base before placing the linoleum on a wooden floor that creaks excessively. In addition, it will help level irregularities and small depressions on the surface.
Helpful advice! The easiest way is to purchase linoleum with a backing. Its price is much higher, but the money needed to buy the substrate is saved, plus a gain in time, besides, you do not need to spend effort for installation. The ideal option is semi-commercial linoleum. The characteristics of such a coating provide for good insulation and unevenness compensation.
If the thickness of the semi-commercial linoleum is insufficient, then you can additionally use the substrate. How to properly lay linoleum and a substrate on a wooden floor, we will figure it out below.
How to lay linoleum on a wooden floor: leveling the surface
Wood flooring is a common base. As a rule, even an ideal plank floor has cracks, bumps from nails and other defects. Therefore, it is best to mount plywood with a thickness of 7 mm or more on such a base. On the question of whether it is possible to lay linoleum on a wooden floor, experts give a positive answer, provided that the surface is first leveled.
Before leveling the wooden floor under the linoleum, you need to prepare the floorboards. Irregularities and cracks should be covered with a special putty. This will ensure tightness and good insulation of the floor.
If the floor is new and even, then you can do without a plywood layer, and before putting the linoleum on the wooden floor, you need to carefully fix the boards, level the base with a plane or grinder, drown the nail heads in the wood as much as possible and fill the holes. With the help of putty, seams between floorboards and other flaws are removed. If the boards form an undulating surface, then the floor will have to be rebuilt in places or completely dismantled. The coating must be clean, fine debris and dust in cracks must be removed with a vacuum cleaner.
How to lay linoleum on a wood floor: laying the backing
After leveling the surface and cleaning it from debris, the process of installing the substrate consists of the following stages:
- Laying the insulating layer. As with a concrete floor, it is advisable to use a regular plastic wrap before placing the linoleum on the wooden floor. It will protect the wood from moisture and create the necessary insulation.
- Substrate flooring. The rolled material is laid in strips without overlaps - end-to-end, then they are connected with a sealant or special tape.
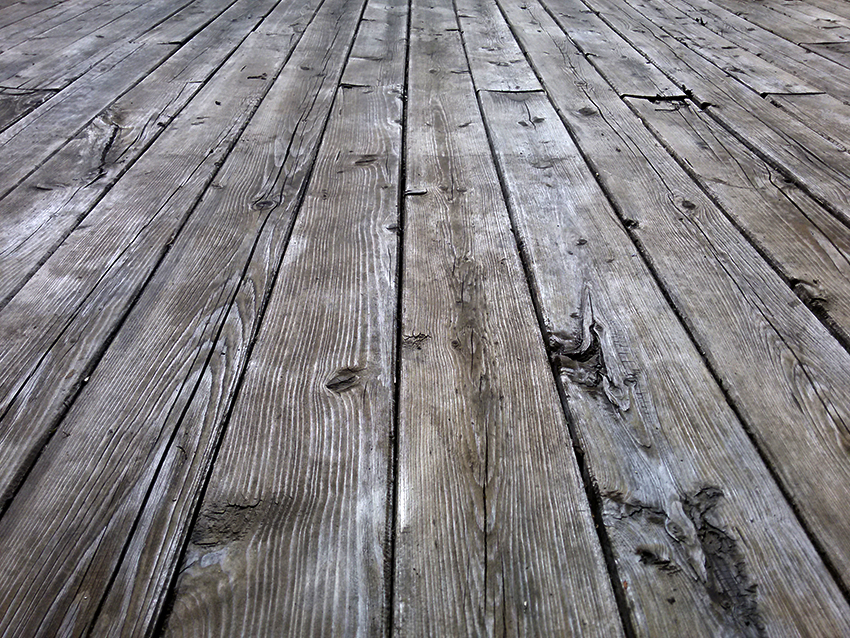
Before laying the substrate on the wooden floor, it is necessary to putty all pits, cracks and irregularities
After that, you can start laying the linoleum on the wooden floor. If plywood is used as a substrate, then the process is more laborious, it implies the following sequence of work:
- surface primer.Before laying linoleum on a wooden floor, the surface is cleaned of old paint and a primer is applied to it;
- the installation of plywood is carried out after the primer has completely dried. Plywood is laid with some offset. The distance from the sheet to the wall must be at least 5 mm;
- fastening plywood. For fastening to a wooden base, it is best to use self-tapping screws, which are easy to use and capable of providing reliable fixation;
- elimination of defects. Burrs are removed at the edges of the plywood sheets using a planer, and the depressions in the places where the screws are screwed are covered with putty.
Helpful advice! If you intend to use linoleum glue on a wooden floor, then remove the old layers of paint and varnish.
How to properly lay linoleum on a wooden floor
There are many tips and tricks on the Internet about how to properly lay linoleum on a wooden floor. Summarizing them, we can come to the conclusion that the direct laying of the linoleum itself is a simple process, preceded by more painstaking preparatory work. The material itself spreads easily. In order for the linoleum to take the necessary shape, you should let it lie down for a couple of days in an unfolded state. The time depends on the flexibility of the material, which is influenced by the specific gravity of 1 m² of linoleum. It is usually more difficult to install natural types of coverings.
It is recommended to use commercial linoleum as a floor finish in rooms with high traffic. GOST characteristics of such a flooring indicate a high degree of strength and durability, superior to laminate. The quality of the flooring is evidenced by a special quality certificate from the manufacturer.
The more flexible types of material are easy to attach. It is enough to carefully align the coating and then grease the edges with special glue. The final fixation will be provided by the installation of the skirting boards. If there is uncertainty in actions and fear of spoiling expensive material, then it is recommended to entrust the work to professionals.
Thus, it is not necessary to always use a linoleum underlay, but sometimes you simply cannot do without it. As an additional material, it contributes to the quality improvement of the floor. The main thing is to decide on the set of functions required from the substrate and choose the right option. Laying the material is quite simple. As a result, it will give additional heat and sound insulation properties to the main coating. On a concrete floor it protects from the cold, and on a wooden floor - from damage and squeak of floorboards.