The hydraulic press is widely used in everyday life. It is necessary for work that requires a lot of pressure on the material being processed. A high-quality multifunctional tool has a high cost, which is completely unjustified for domestic use. You can make a do-it-yourself hydraulic press based on a car jack.
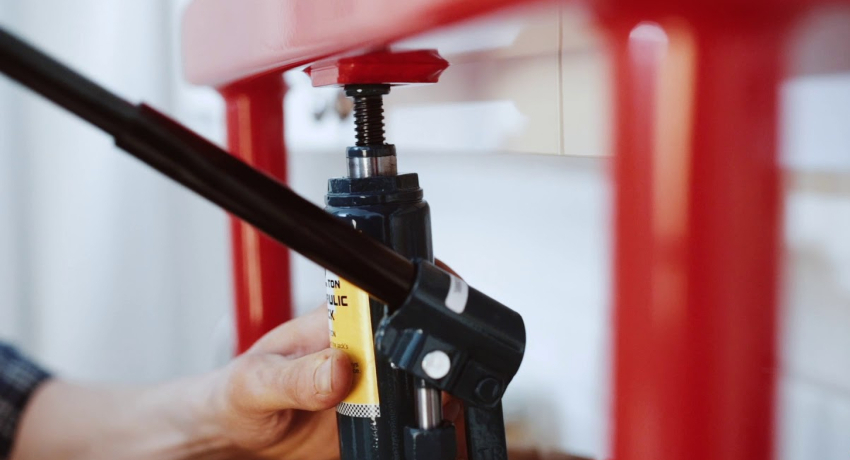
The hydraulic press is used for work in which it is necessary to exert great pressure on the material being processed
Content [Hide]
- 1 Purpose and scope of the hydraulic press
- 2 Variants of using a hydropress at home
- 3 Design of a homemade press from a jack
- 4 Homemade garage press device: design feature
- 5 Features of DIY hydraulic press
- 6 Designing a homemade hydraulic press for a garage with your own hands
- 7 The sequence of making do-it-yourself press from a jack
- 8 Features of creating a hydraulic oil press with your own hands
- 9 How to use a hydraulic jack: design features
- 10 Features of a DIY electro-hydraulic press
- 11 DIY hydraulic press repair from a jack
- 12 How to make a hydraulic press with your own hands: video instruction
Purpose and scope of the hydraulic press
A hydraulic press is a device that exerts great pressure on the material to be processed with little effort. This principle of operation is based on Pascal's law, according to which the applied force acting on a certain area is transmitted throughout the volume and is equal in all directions.
The hydraulic press device is represented by two cylinders. When exposed to a smaller chamber, the pressure of the liquid in it increases, which is transmitted through a special channel to the large chamber. The working fluid exerts pressure on the piston, which contributes to the effect of the element on the workpiece being processed. Cylinders are usually arranged vertically, but there are options for horizontal placement. A special oil is used as a working fluid.
The installation is used for pressing, stamping, extrusion, assembly, forging, bending, straightening of metal elements. You can buy or do it yourself a cardboard press, which will become indispensable for packaging, briquetting, pressing and recycling materials from plastics, paper and rubber. The equipment is characterized by its versatility and can be used in various spheres of life for repair, maintenance and preventive maintenance. Depending on this, the press has a certain design.
Variants of using a hydropress at home
To squeeze metal elements out of the shell or base, you can buy or make a hydraulic press with your own hands in the garage. The equipment is also suitable for extrusion of bearings and silent blocks, which are not amenable to manual assembly and disassembly. With the help of such a device, you can straighten, dock two elements, bend a metal workpiece.
Useful advice! When making a press with your own hands, you need to decide on the further purpose of the device, its dimensions, piston indicators, weight and the possibility of installing a pressure gauge.
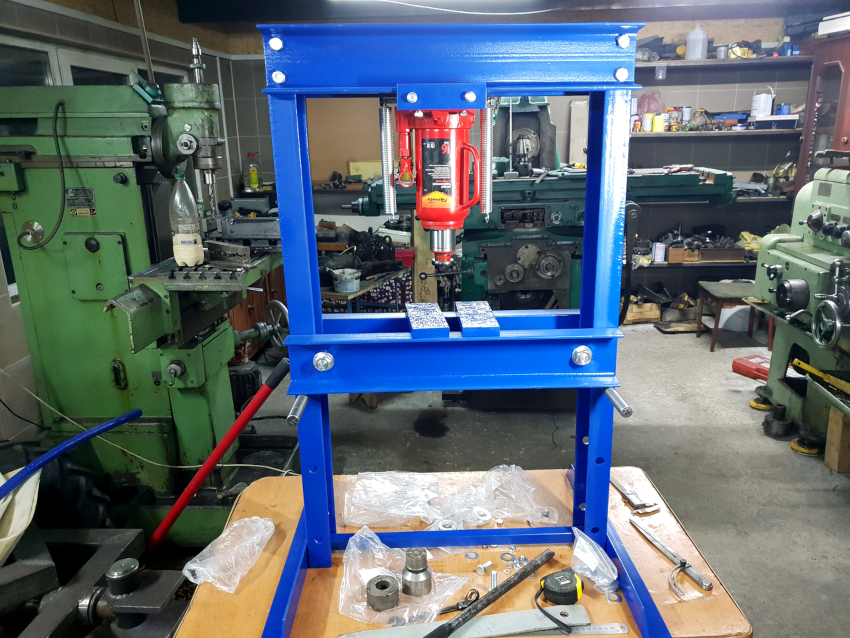
When making a hydraulic press for a garage, it is necessary to take into account the dimensions of the serviced vehicle
When building a hydraulic press for a garage, consider the size of your vehicle. For light vehicles, it is enough to make a simple structure, and for large cars it is better to make a more complex and dimensional unit.
The device is often used as a waste paper press. With your own hands, you can make good fuel for the furnace from old paper. For such purposes, it is enough to make a simple structure with an average power rating, which will allow the disposal of a large amount of waste paper.
The equipment is also suitable for pressing sawdust. Such briquettes are good fuel for stove heating, they burn for a long time without the formation of smoke, creating a strong heat. Instead of sawdust, coal chips are also suitable as filler for the press. Such a unit will consist of a desktop, a base, a power frame and a drive.
A good result is ensured by a self-made press for PET bottles, which turns the container into neat layers. The hydraulic tool can be used as a hay pick-up. In this case, the design is complemented by a frame frame made of timber or metal without an upper part. The element is fixed to the forehead using special fasteners. You will also need a transport pick-up and undercarriage.
Design of a homemade press from a jack
Before you make a hydraulic press with your own hands, you should figure out what constituent elements are included in its design.
For the stability of the device, a strong and reliable base is required, which acts as the base of the installation. It looks like a platform and is made of massive thick rolled metal. For this, channels and metal corners are mainly used.
As can be seen from the press diagram, the vertical parts of the structure are represented by racks. The elements are made of steel corners and welded to the base so that a right angle between the elements is ensured. The height of the posts is calculated as the sum of the height of the jack, the length of its rod and the thickness of the workpiece. A fixed stop is fixed at the top of the racks. A corner is used for its manufacture.
A hydraulic jack is used to create the required force on the work surface. It will need to be fixed to the movable stop. The jack is operated with a hand lever or electric drive.
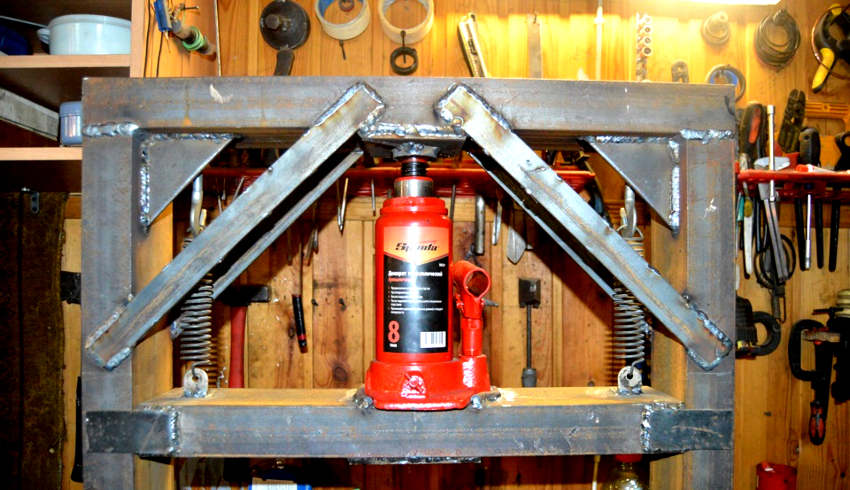
The height of the side posts must correspond to the sum of the thickness of the workpiece, the height of the jack itself and the length of its rod
The movable stop exerts pressure on the pressing mechanism. The element is made of steel strips or corners. A return device is used to move the stop to its normal position. It is represented by several springs. Their length and degree of stretch are calculated based on the parameters of the press.
Homemade garage press device: design feature
Before making a hydraulic press, you should decide on the type of installation. Depending on this, the equipment can be table-top or floor-standing. The first type of tool is located on a workbench, and the second is placed on a special pedestal. Such presses differ in size and carrying capacity. A hand-made table hydraulic press provides a force of up to 12 tons, and for a floor device this value reaches 25 tons.
The tabletop design is more stable and mobile. Due to its small size, it does not take up much free space. This press is used for processing small workpieces.
The hydraulic floor press is characterized by its large size and heavy weight. To install it, you will need the construction of a special platform. Such a machine will cope with the processing of large metal elements, disassembly and assembly of complex units.
Important! To expand the functionality of the floor hydraulic press, it should be equipped with an electric motor.
You can make a complex structure that will be used for a wide range of tasks. However, the manufacture of such an option will take a long time and will require the use of specialized tools and equipment. As a garage hydraulic press, it is better to make a manual model equipped with a hydraulic pump and drive. This design is two-speed, its piston is characterized by mobility.
A self-made hydraulic press for a garage can have a horizontal or vertical design. The first type of device is used for straightening, cutting and bending individual metal elements. The vertical equipment is designed for unloading and pressing in parts. The DIY hydraulic waste paper press is gaining popularity.
Features of DIY hydraulic press
A self-made design must perform the required list of tasks. A device that creates an effort of 15-25 tons is sufficient. For its manufacture, you will need to prepare a do-it-yourself working drawing of a hydraulic press from a jack with the dimensions of all structural elements (such a diagram can be found on the Internet). In this case, one should take into account the type of tool, which can be stationary or removable, the dimensions of the product, the piston stroke and the design of the bed.
The working cylinder of the hydraulic press is located separately or built into the structure. Moreover, it can be at the top or bottom. In the case of the first option, the pressure will be applied to the lower surface of the base. If the working element is located on the bottom of the bed, pressure will be directed upward as a result of the operation of the main stem.
A jack is used as a hydraulic cylinder, which acts as the main working element. It should be borne in mind that the tool can be presented in different versions.Therefore, when choosing a jack, it is necessary to decide for what purposes the press will be used and take into account the maximum effort of the device.
Remember, however, that a bottle-type industrial tool will not function upside down. Therefore, before making a press from a jack, it is necessary to complete the product. The design should provide for the installation of a socket that will contact the hydraulic cylinder rod. To make it, you need to use a piece of pipe.
The material for the bed is selected with a margin of safety, which will exclude damage to the frame when applying the maximum possible force. After completing the task for processing the workpiece, the rod should return to its original position. To do this, it is necessary to choose the right springs based on the degree of rigidity, due to which they will be able to effectively fulfill their purpose. Their edges are attached to the movable upper and fixed lower parts of the base.
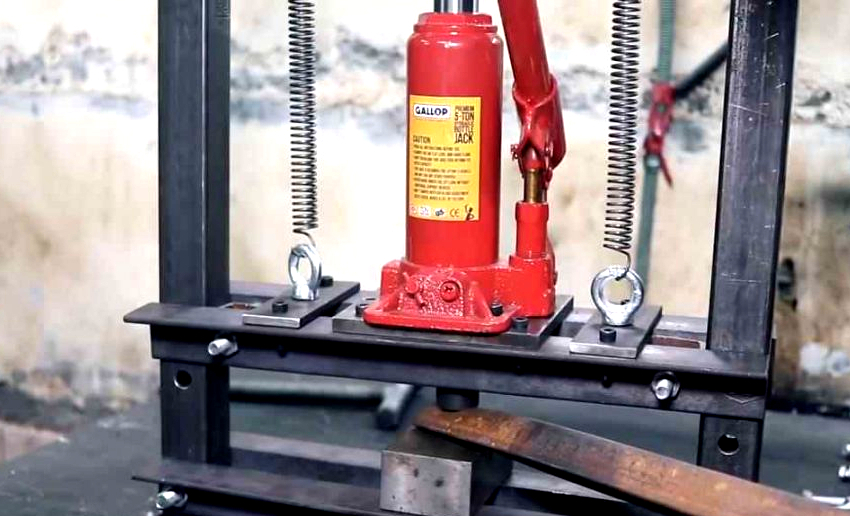
The material for the racks and the bed must be selected with a safety margin, this will exclude damage to the press when a lot of pressure is applied
Designing a homemade hydraulic press for a garage with your own hands
After choosing the jack, you should start designing the bed, which will be pressured by the hydraulic cylinder. For this, a do-it-yourself hydraulic press drawing is created. And the dimensions on it are applied for each individual element of the device. The structure must be strong, because during operation of the device, the jack will exert both downward and upward pressure on it, trying to break the frame.
The base must ensure the stability of the equipment, the best solution is to implement it as a platform. The width of the table is determined based on the dimensions of the product that will be processed on the press. However, it should not be less than the total width of all elements of the press equipment.
The height of the bed is calculated as the sum of the dimensions of the jack, the value of free movement of the rod, the height of the parts to be machined and the thickness of the mobile work platform.
The jack is fixed to the base. The top of the frame acts as an emphasis for products. With the help of a movable table, pressure is transferred to the part. The surface is installed on top of the jack on the bed, along which it moves freely up and down with fixation on the sides.
To ensure the adjustment of the free movement of the jack rod, replaceable insert-liners from a solid or hollow metal profile can be installed. Another option involves the implementation of a removable stop in the form of a working table that moves. It should be secured to the bed with nuts and bolts or rods. To do this, it is necessary to make holes in the frame with a height less than the range of movement of the jack rod.
Another solution is to create a so-called screw press with your own hands using a steering wheel drive. It will be possible to reduce the clearance for the workpiece inside the frame by tightening the screw with the plate.
Useful advice! To regulate the free movement of the stem, it is better to use a combination of several of the above options.
The sequence of making do-it-yourself press from a jack
Before you make a press with your own hands, you need to prepare a welding machine, electrodes, grinder, drill and drills. For the finishing of metal structural elements from burrs, you will need a sander. At the first stage, the press frame is assembled. The quality and efficiency of the work process depends on its strength and reliability. The bed will contain the working cylinder (in the form of a jack) and the workpiece to be processed.
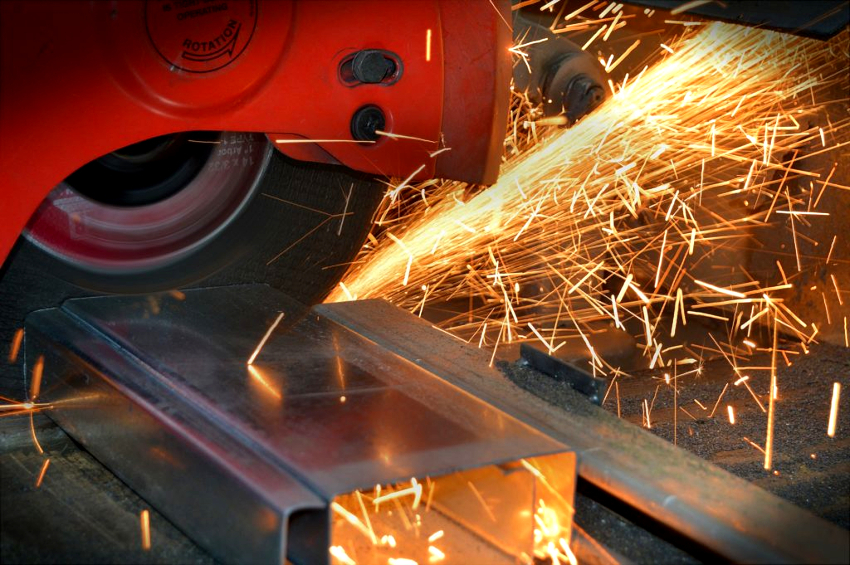
To manufacture the base of the installation, designed for a pressure of up to 5 tons, a channel of standard size 8P is required
The bed material, its design and assembly variant are determined based on the perceived pressure of the jack. According to the do-it-yourself press drawing, the base of the device is represented by a U-shaped rectangular frame made of a channel or welded steel angle. The main effort will be concentrated in the central part of the horizontal bars. Achieve the maximum possible stability of the structure by welding it to the base of a metal plate with a thickness of 08-1.2 cm.
Related article:
Hand Hydraulic Presses: Features of High Efficiency Tools
The device and the principle of the tool. Types of fixtures. Areas of use of the hydraulic press. Selection and operation rules.
To manufacture the bed of the installation, designed for a force of up to 5 tons, you will need a channel of standard size 8P and two hot-rolled corners of 50x50 mm, which are connected by a solid welded seam or connected by rods every 25 cm.If the tool will perceive a force of up to 10 tons, a channel is required for the bed 10P and paired corners measuring 63x7 mm. For the manufacture of a press with the required compression force of 15 tons and more, a 14P channel and a twin corner with a size of 75x8 mm should be used.
Important! The frame made of the above-mentioned rolled metal will have a tenfold margin of safety, which will contribute to the normal operation of the device - without destroying the frame.
Features of assembling a garage press bed with your own hands
All elements for the frame are interconnected according to the drawing of the hydraulic press. First, the base is assembled, then the side parts and the upper frame of the frame. It is important to monitor the observance of the geometry of the structure, in which all elements should be sides of a right angle.
Docking takes place by performing welded one-piece double-sided seams with trimming products end-to-end. An alternative is to use cotter pins or bolts to assemble parts. In doing so, the maximum permissible shear load must be taken into account. With such a connection, the main load will be concentrated on the bolted connections. Therefore, it is important to correctly calculate their number.
Next, a movable bar is made for a do-it-yourself hydraulic forging press. For this, a square tube or channel is used. In its central part, a piece of pipe is welded, which will later serve as a socket for the stem. The guides are made of two steel strips, the length of which must be equal to the outer width of the body. Elements are bolted to the side posts of the mobile structure.
A removable stop is made in the same way. It is necessary to make holes in its guiding parts to adjust the height of the working space. At the final stage, the jack and springs are installed.
How to remodel a press jack to work upside down
The most affordable option, which is used as a hydraulic cylinder for a do-it-yourself hand press, is a bottle jack. The main problem with such a tool is the inability to function upside down. In this case, you can fix the tool permanently to the upper beam. In this case, the bottom base will be used as a reference element. Before making a press with your own hands, you will need to refine the hydraulic mechanism.
There are several options for altering the jack that can be used when assembling a homemade hydraulic press.The first is the additional installation of a 300 ml expansion tank. The container must be connected to the jack filler hole using a conventional silicone pipe. In order for the element to be firmly fixed, you must use the oxygen hose fittings, which can be purchased at any auto parts store.
The second option for altering the jack involves disassembling the tool. To do this, completely drain the oil from it and bleed the plunger. Next, the upper clamping nut is twisted by clamping it in a vice. Then you need to loosen the outer glass with a rubber mallet. The element must come out of the seat ring, which is located at the base of the jack.
After the plunger arm, there is a fluid intake hole. If the glass is not completely filled in its inverted position, the hole does not come into contact with oil. This is a major problem when using a homemade press jack. You can solve it with a tube, which should be pressed over the entire length of the glass.
The jack can be left in its original design. However, to ensure the operability of the structure, an additional third beam will need to be installed. It is attached to the side walls quite tightly, which contributes to the stationary position of the jack when creating pressure. The tool is fixed in an inverted position to the central part of the upper beam with M8 or M10 bolts.
How to make a press: making and installing pressure pads
Large workpieces require a large area of compression beams. The jack rod in this case will not provide this, since during pressing, the force must be evenly distributed over the entire area of the treated surface, excluding the formation of deformations.
As pressure pads for a self-made hydraulic press for a garage, you can use full-bodied ingots, in which blind holes with threads are made, whereby the elements are fixed to the press structure.
The best option is to make do-it-yourself press pads with a jack. To do this, you can purchase four pieces of a metal corner or two channels. The elements are used to create a parallelepiped with open side faces. Butt areas that perceive the main force should be welded from the inside with a continuous seam. The rest of the places are welded outside.
One of the faces must be plugged with a square insert, and the inner cavity must be filled with concrete M500 mortar. After the solution has solidified, the block is welded on the other side. Thus, there are two incompressible elements.
A jack with a rod is attached to the upper block. For this, a blind hole is made, where the heel of the tool is inserted with a minimum clearance. Holes are also made here to fix the return spring mechanism. The bottom block is attached to the adjustable beam. For greater reliability and limiting shear, a pair of corners of metal rods are welded onto it.
Installing a movable support beam of the return mechanism for a homemade hydraulic press
The lower and upper beams must have the same cross-section. Elements differ only in design. To make the lower support element, two channels are used, which should be turned with their ribs outward. They must be applied on different sides relative to the posts and welded to their central part by using inserts from corners or thick reinforcement.
The fixation of the beam on the racks is carried out using massive steel pins. Under them, a series of circular cuttings should be made at different heights with parallel placement in vertical channels. The diameter of the holes must match the cross-section of the bolts.
Another structural element of a do-it-yourself hydraulic garage press is a spring mechanism, thanks to which the jack returns to its original position when the bypass valve is opened. For this, you can use simple door finishing springs, which can be purchased at your hardware store.
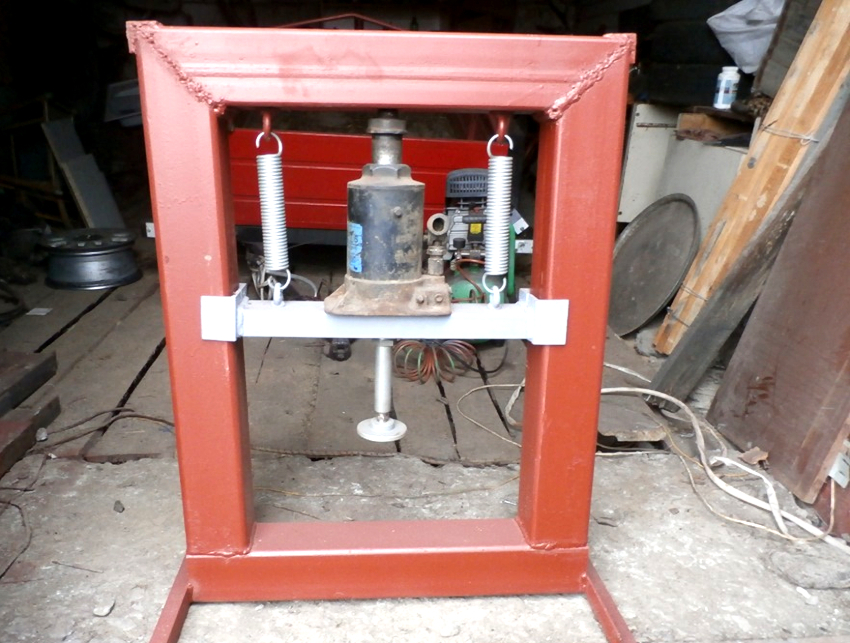
The springs used for finishing the doors ensure the operation of the resettable support beam of the return mechanism
The task is complicated by the upper pressure beam, which has a significant weight, as a result of which the spring may not be compressed. You can get out of the situation by increasing the number of spring elements to 4-6 pieces, which is acceptable for a do-it-yourself table hydraulic press. It is also possible to use more powerful elements designed for doors, which is more relevant for floor installations.
If there is no upper block, the springs are attached to the jack rod. The fixing is done with a washer, which has an inner bore larger than the stem adjusting screw, but smaller than the piston diameter. The spring should be fastened by means of two small outer holes with fixation to the upper beam in the same way. The spring may not be installed strictly vertically. Excessive element length can be compensated for by its inclined arrangement.
Useful advice! Welded hooks can also be used to secure the spring.
Features of creating a hydraulic oil press with your own hands
A homemade jack press can be used as an oil squeeze device. However, in its manufacture, it is necessary to provide for some design features.
A metal plate must be attached to the upper crossbar of the frame. It should move easily along the guides when acting on the screw shaft. This mechanism makes it possible to control the gap between the clamping block and the material being processed.
Bolts are used to fix the removable movable block of a homemade press from a jack. They are installed in pre-created holes at a specific pitch, as determined by the working process. However, the distance between the holes should not be greater than the amount of free movement of the hydraulic jack rod. Clamping elements are made of metal of different thickness and are removable. Using this technology, you can also make a paper press with your own hands.
Useful advice! The fixing of the pressure beam to the guides can be carried out using fingers made of durable metal, the diameter of which is selected based on the size of the body and the force applied during the operation of the device.
How to use a hydraulic jack: design features
Most often, a homemade press is made from a hydraulic jack. This is due to the design features of the product and the principle of its operation, which is based on the laws of hydraulics.
A piston is located in the jack cylinder. Above it or in a separate reservoir is the working fluid in the form of mineral oil. The hydraulic jack is driven by a small pump that pumps oil through a relief valve above the piston. Force is minimized due to the difference between the diameters of the plunger and the tool barrel.The working fluid, which is located above the piston, pushes it out, which helps to lift the load located above it.
To lower the tool, you need to know how to use a hydraulic jack. To do this, slowly bleed the operating oil from under the piston into the reservoir or into the top of the cylinder. For this purpose, a round head relief valve with shoulders is used, which must be loosened.
During the operation of the device, certain difficulties may arise, which occurs as a result of insufficient oil level in the device. For troubleshooting, it is important to know how to fill a hydraulic jack with your own hands. To do this, unscrew the filler plug on the tool body and insert a hose into the hole to fill the reservoir to the required volume. At the end of the process, the jack is pumped.
Features of a DIY electro-hydraulic press
You can independently make not only a manual hydraulic press, but also a device equipped with an electric drive. Such a device is capable of developing enormous efforts, which expands the functionality of the equipment and increases its efficiency.
The principle of operation of a self-made hydraulic press with an electric drive is as follows. The hydraulic pump is driven by a motor that is connected to the mains. In turn, the hydraulic pump helps maintain the required pressure of the working fluid in the first press chamber. The piston ensures the transfer of pressure to the second reservoir of the press, where it increases several times. Thus, the resulting force is transmitted from the second cylinder to the material being processed.
Important! The amount of force transmitted to the workpiece will depend on the ratio of the areas of the pistons in both cylinders.
With an electric motor, you can create both a floor-standing and a table-top hydraulic press with your own hands. Both options will differ in size and value of the force exerted on the workpiece being processed. For tabletop devices, it does not exceed 20 tons, and for floor-mounted devices - 100 tons.
DIY hydraulic press with an electric motor
The manufacture of the device begins with a do-it-yourself drawing of a hydraulic press with the application of all structural elements and an indication of their dimensions.
The frame of the structure must withstand significant loads, therefore it must be made of durable material. The best solution is to use a T-beam that will not bend under the hydraulic press.
The frame is represented by a U-shaped bed, which is installed on a base from thinner corners or channels. In the central part of the frame in height, it is necessary to install a working platform from a thick-walled channel by welding.
The next step in making a homemade hydraulic press with your own hands is to install a hydraulic cylinder on the bed, which is carried out in a certain sequence. To ensure reliable fastening of the hydraulic pump, it should be fixed to a metal plate using a flange. The slab itself is mounted on the frame I-beams.
The flange can be made from an automotive hub by turning it on a lathe. In the metal plate for installing the hydraulic cylinder, you need to weld a round boss to fix the lathe in the chuck. After boring the hole, the plate is welded to the base of the frame.
A flange with the required bore is put on the hydraulic cylinder and welded in a circle. For the reliability of the device, it is required to manufacture and fix another flange to the upper part of the hydraulic cylinder, welding it to the beams.
Important! The flange and the hydraulic cylinder must be welded to each other as evenly as possible, therefore the surface of the first one is pre-processed on a lathe.
A metal plate with welded beams is fixed to the bed by welding. Holes for fastening bolts are made in it. To ensure the normal operation of the press, an oil station should be installed by connecting it to the hydraulic cylinder using hoses.
DIY hydraulic press repair from a jack
To maintain the long-term performance of a hydraulic press, made on the basis of a jack, a self-made device needs proper operation and maintenance. During operation, it is necessary to monitor the oil level in the hydraulic cylinder, lubricate moving parts, check the condition of the sealing joints, and the reliability of fastening the assembly elements.
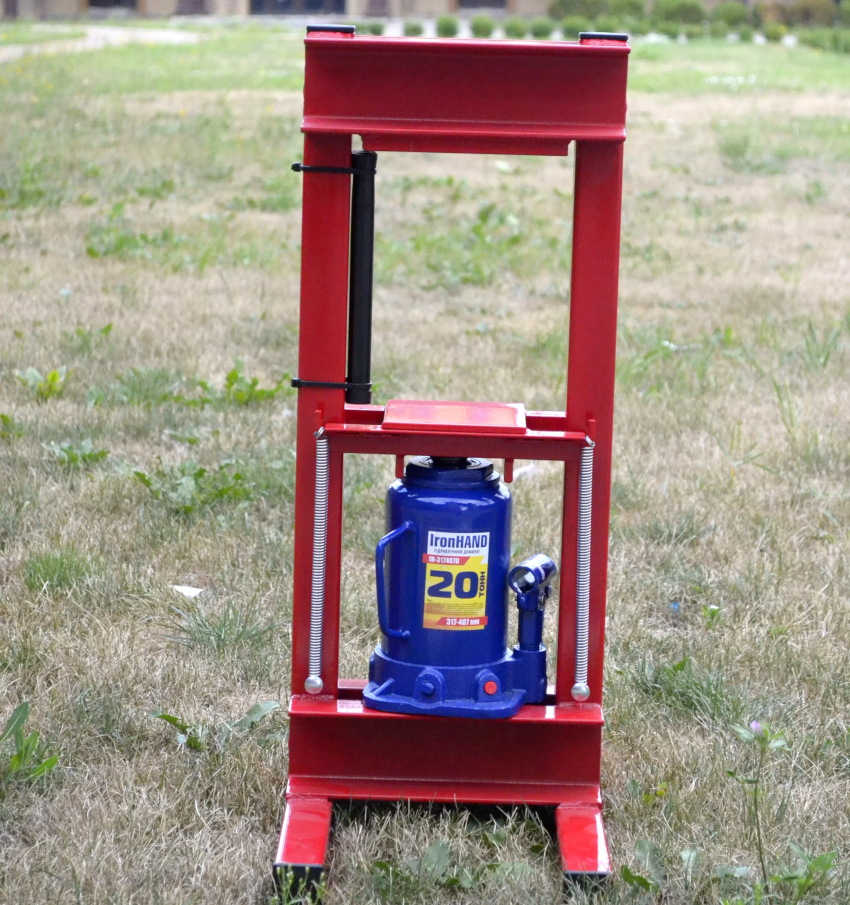
To maintain the performance of the press, it is necessary to monitor the oil level in the hydraulic cylinder, check the reliability of fastening of the elements and lubricate the moving parts
However, any mechanism may malfunction, which is the cause of improper operation or wear of individual structural elements. If a garage hydraulic press created by your own hands has stopped or does not start, you should check the oil level in the hydraulic cylinder. If its volume is insufficient, it will be necessary to fill the container with the subsequent pumping of the jack.
If fluid leakage is observed, this indicates mechanical damage to the structure or breakdown of its individual elements. To eliminate the defect, it is necessary to disassemble the jack, check all its parts for corrosion damage. The stem is inspected for deformation. The damaged elements must be replaced with new ones. The operating oil must be completely drained. The inner cavity of the jack and all its elements are washed with kerosene and dried. Old gaskets and gaskets must be replaced with new ones.
Other malfunctions of a DIY hydraulic cylinder press
If there is an insufficient level of effort of a manual hydraulic press, done by hand, or the mechanism works intermittently, such a problem is associated with the possible ingress of air into the cavity of the jack, which negatively affects the operation of the piston. To repair the damage, the working fluid must be added to the cylinder by removing air through the tubes.
The low pressure of the mechanism is due to damage to the valve, which has moved away from the compartments, is dirty, or the springs in it are weakened. In the first two cases, the element is repaired or replaced. The valve is cleaned with a damp cloth, followed by drying the element. In case of heavy contamination, the mechanism is washed with kerosene or gasoline and dried with compressed air. If the reason lies in the wear of the springs, they must be replaced with new elements.
Important! If the housing or piston of the jack is damaged, a complete replacement of the mechanism is required, which cannot be repaired.
After disassembling the jack for repair work, the mechanism must be assembled under certain conditions. The valves must fit snugly against the seats. It is necessary that there is a sufficient amount of fluid in the hydraulic cylinder. There must be no air in the system.
The hydraulic press is a multifunctional, versatile equipment that can be used to solve different tasks where effort is needed.The tool can be purchased at a specialized store or you can make a do-it-yourself press from a hydraulic jack, which will save money. For this, it is important to choose the right material and adhere to the algorithm for assembling elements.