A wooden floor consists of many elements, during the installation process of which it is very difficult to achieve a perfectly flat surface. Small defects, scratches, drops often occur. Such problems are common with both new coatings and old surfaces. One of the most effective ways to eliminate all the deficiencies and flaws in the coating is to polish the wooden floor, which can be done manually or mechanically.
Content [Hide]
- 1 Why is wood floor polishing
- 2 Manual sanding of plank floor
- 3 How to grind wood: varieties of special electrical equipment
- 4 What parameters should be considered when choosing a floor grinder
- 5 Technology of sanding wood floor with a sander
- 6 How to grind a board at home with a grinder
- 7 How to sand a wooden floor with your own hands: video
Why is wood floor polishing
Sanding a wooden floor is the leveling and polishing of the surface in order to prepare the substrate for coating it with varnish, oil, wax or other protective and decorative agent. When performing this process, the old paint and varnish coating, existing dirt and surface defects are removed.
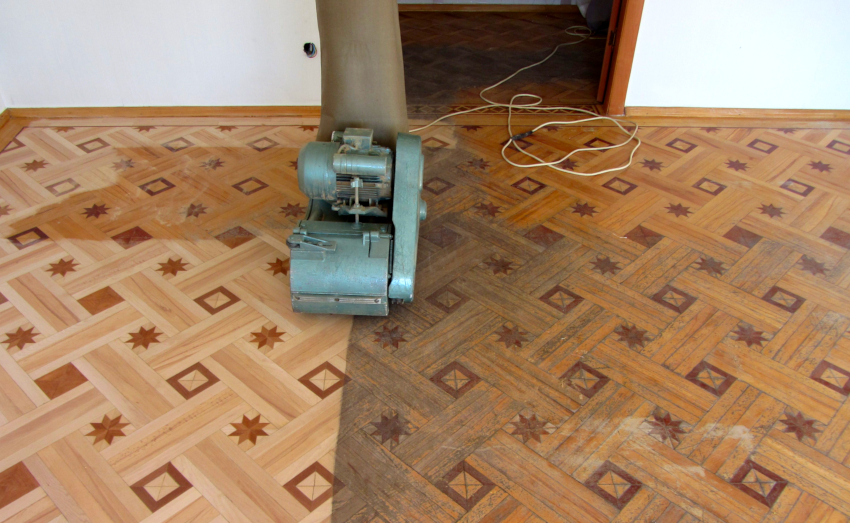
Sanding a wooden floor is carried out in order to prepare the substrate for coating it with varnish, wax or oil
However, there are cases when it is impractical to perform floor grinding. If there are gaps of more than 0.7 cm on the covering between the wooden planks, which are difficult to fill with a sealant or putty, it is recommended to "sort out" such a floor with the replacement of damaged surface areas. You can also repair the base by compacting the canvases with wooden blocks, matched to the size of the gap. Only after carrying out such activities can you start grinding the surface.
Sanding of old wooden floors is not performed if there are places of abrasion on the surface with a depth of more than 4 mm, which are the most loaded, deep scratches, chips, dents, cracks and other defects. It is recommended to replace such areas. Plank or parquet floor may swell due to contact with water. As a result, rotten, moldy areas may appear on the surface. The wood becomes loose, so problem areas need to be replaced before surface treatment.
Sanding a wooden floor is done manually or mechanically. The essence of the technology is to gradually reduce the grain size of the grinding attachment. Thus, at first, a rough surface treatment is performed with a nozzle with a grain of 40-60 units, and then a fine one (100-120, 140-180 units).
Manual sanding of plank floor
Sanding of a wooden coating can be carried out manually or mechanically, which is determined by the volume of work and financial capabilities. The first method is advisable to use for processing small areas. The event is very cheap, but a long and laborious process is expected.
The mechanical method is characterized by a high speed of work. The surface is perfectly flat and smooth, which cannot be achieved with manual grinding. The work is carried out using special units that can be rented. At the same time, it will be possible to save on the price for the work. In this case, sanding of wooden floors will be done independently. Despite the fact that this method involves additional costs for equipment, the surface as a result of processing is of excellent workmanship.
For manual grinding of wooden floors in small volumes, sandpaper is used in the form of a sheet or roll product with a grain size of 40 to 120 units. The grain size of the material is selected based on the individual characteristics of the treated surface: the degree of pollution, the presence of an old paint and varnish coating, the strength of the wood, the presence of defects.
Manual sanding can be carried out with a wooden or PVC float, in which there is a holder for sandpaper. For small areas, you can use a plastic product, and for larger areas it is better to use a wooden fixture with an ergonomic rubber handle.
A hand scrubber or scraper can be purchased to remove old paintwork or to clean heavily soiled areas. The tool consists of a wooden or plastic handle and a 45-degree bent steel plate.
How to grind wood: varieties of special electrical equipment
To perform high-quality and fast grinding of a wooden surface, the machine method is most often used. It involves the use of special electrical equipment, represented by various grinding machines, on the choice of which the prices for grinding a wooden floor depend. There are units of drum, belt, vibration type, surface grinders and eccentric devices.
The drum sander consists of a shaft where abrasive tools are installed. The drum, in turn, can be rolling and centrifugal. It is advisable to use such equipment for primary or rough surface treatment. Also, the unit, depending on the model, can perform scraping in three directions, which is determined by the peculiarities of the fibrous structure of the wooden base. The sander efficiently removes old paintwork and evens out the surface.
The operation of the unit is carried out by rotating the drum thanks to a belt drive from the engine. The belt installed on the shaft is very tightly pressed against the surface under the machine's own weight. This type of grinding equipment is characterized by large dimensions, significant weight and high power.
The machine, thanks to its coarse-grained abrasives, removes thick layers of wood, performing exclusively rough surface treatment. The unit is equipped with a dust collector for storing sawdust.The price of sanding a wooden floor for m² surface is 120-150 rubles.
Belt sanding machine for wood surface
The wood sanding belt machine is equipped with two shafts to rotate the belt. The unit is also used for scraping large floors. In contrast to the drum analog, the belt equipment provides a higher quality of the processed surface. This is due to the fact that the tape, which is mounted on a cylindrical shaft, acts as a working element. Therefore, no joints are formed when grinding. These units are equipped with a more efficient dust collector.
Floor grinding belts can have different capacities. The higher it is, the more work can be carried out non-stop. Some models of sanders are equipped with speed controllers for the abrasive belt, which can have different widths and grain sizes. The price of scraping and sanding a wooden floor with a belt sander starts at 170 rubles.
Important! There are models of belt sander equipped with an automatic belt centering function.
The belt sander, like the drum sander, is produced in a rich variety of species. There are standard and professional models. The units can be single-phase (220 V) or three-phase (380 V) connected. Some models are equipped with integrated dust bags.
Important! There are options for grinders that have an adapter for attaching a construction vacuum cleaner.
Grinding, scraping a wooden floor with a surface grinder
The work of surface grinders is carried out using special cylinders equipped with abrasive pads. Such units are intended for secondary (finishing) surface treatment, which is perfectly flat and smooth. The mechanisms are equipped with a single-disc mono nozzle made of sandpaper or three discs rotating on an internal axis, due to which the efficiency increases and the area of the ground base increases. The grain size of the abrasive wheels is 100-340 units. The units are designed for processing large surfaces.
Single disc wood floor sander is easier to operate. It is advisable to use them for sanding floors in hard-to-reach places, for example, in corners, along walls, under stairs, radiators. The abrasiveness of the nozzles is 40-320 units. The units are equipped with rotary handles for ease of use. All models have dust collectors and adapters for connecting a vacuum cleaner.
In a three-disc wood floor sander, each element rotates around its own axis, and they all revolve around a single center. This principle of operation of the attachments allows you to get the most even and smooth base. The price of polishing a wooden floor per square meter of surface is on average 130 rubles.
Important! The best result of sanding a wooden surface is provided by professional machines equipped with a system of floating fit of working attachments.
Other varieties of floor sanders
Angle grinders are used to process hard-to-reach places. In such units, the working element is represented by a grinding disc (flat, disc, cup or polishing). Such units are equipped with many additional useful functions, namely: the option to maintain a constant speed, the ability to soft start the unit, adjust the speed of the circle, protection against unintentional activation.
Vibration-type devices work on the principle of translational motion. They are characterized by their compact size and versatility. Vibrating machines are recommended for both rough and fine floor processing. Thanks to the forward movements of the rectangular sole, the secondary layer is removed. The higher the amplitude, the higher the speed of work. However, as the speed increases, the processing quality deteriorates. Therefore, for fine grinding, the range of motion should be minimal.
Some vibratory grinders are equipped with vibration and power adjustment. The devices have adapters for connecting a dust collector or vacuum cleaner. As consumables used abrasive sheets with varying degrees of grain, sanding cloths and mesh with spraying. The cost of sanding a wooden floor is on average 180 rubles /m².
Important! Vibratory sanders should not be used on parquet floors.
Eccentric devices work on the principle of a grinding wheel and a vibration machine, which ensures a high quality surface treatment. The performance of the device is controlled by the diameter of the vibrating circle. The smaller it is, the better the finish of the base is.
The type of surface grinding is determined by the speed of the device. The minimum speed is selected for processing parquet boards. The price of grinding wooden floors from boards is 160 rubles. behind m² surface. Parquet base processing will cost 120 rubles /m².
What parameters should be considered when choosing a floor grinder
All kinds of wood floor sander can be divided into household and professional. The first type of units is characterized by compact dimensions, light weight and affordable cost. The power of these devices reaches only 1 kW. Such units are rarely used. They are able to process a 15 cm wide space in one step.
Professional wood floor sanding tools are large and heavy equipment. Such machines are capable of treating an area with a diameter of up to 60 cm in one go. The units are equipped with protection against engine overheating, equipped with attachments that can be replaced very quickly. Also, such mechanisms have various protector elements in the form of limiters, RCDs, speed switches, rotary ergonomic handles. The value of power consumption for such machines is on average 2-2.5 kW.
Professional units have the ability to adjust the downforce of the abrasive. This allows you to ensure a uniform fit of the nozzle to the treated surface, which allows you to get a better result.
When choosing a high-quality grinder, you should pay attention not only to ease of use, but also to the quality of manufacturing of its elements. The unit must have a flat surface without chips, cracks, sagging, coating sagging, significant clearance between parts.
Important! Make sure that all fasteners are strong and reliable.
Some models are equipped with additional functions, among which there may be a soft start option, the ability to adjust the engine speed, usually there is an adapter for attaching a dust collector or vacuum cleaner.
Related article:
Parquet: DIY repair and restoration of flooring
Why defects are formed on the coating. How to get rid of squeaks, scratches, scuffs and sheet divergence. What to do if you get wet.
Choosing a specific model, you should also pay attention to the units of well-known manufacturers such as Aeg, Stanley, Lagler and Bosch, which offer high-quality equipment with a long warranty and proper post-warranty service.
Technology of sanding wood floor with a sander
Sanding wood flooring is a complex and time-consuming undertaking that consists of several stages. To do this, you should get a special sander for horizontal surfaces. For processing a base laid on logs, it is advisable to use a belt or drum type of unit. When a question arises, what is the parquet polishing, the answer is unequivocal. For such a base, an exclusively surface grinder is used. Another type of mechanism can bend or break the coating.
To perform wood floor sanding work, you will also need a machine for processing corner areas and hard-to-reach places. A manual cycle is ideal for this. To remove wood dust, you will need a powerful construction vacuum cleaner. An important material is sandpaper with grains of different sizes - from 40 to 140 units.
Helpful advice! Quality sandpaper is used to indicate the direction of movement of the material for maximum effect.
To eliminate large gaps and crevices, you will need a putty. You should also prepare sandpaper scissors, brushes, roller and varnish for finishing the surface.
Preparatory stage before sanding a wooden floor from boards
The first step in sanding a wooden floor with your own hands is to prepare the base. For this, the room is freed from furniture, carpets and other elements. If linoleum is laid or there is another covering, it must be removed. The plinth is dismantled (if available).
The floor should be checked for visible defects in the form of chips, large gaps between wooden elements, protruding nails, fallen out knots, unsticked dies. If necessary, repair work is carried out on the base, which involves hammering the floorboards, replacing rotten or severely damaged elements, filling up visible significant gaps, cracks and cracks.
Old parquet floors are tested for strength and integrity, secure fixings and surface damage. To eliminate minor imperfections, you can use parquet glue or putty masses. Sealants and grouts should not be used to repair old parquet flooring, as they will not provide sufficient coating strength.
Important! All steel elements must be sunk into the floor by at least 3 mm so that they do not cause damage or breakdown of the machine.
Before performing rough grinding, the base should be repaired with the replacement of old elements, fixing the detached strips with an adhesive composition. Then the surface is thoroughly cleaned with a construction vacuum cleaner or the debris is removed with a damp cloth.
Coarse sanding of the floor from boards with special mechanisms
The next step is to rough the floor. To do this, use a belt or drum type sander. If you are working with the unit for the first time, you must get used to it. To do this, sandpaper is inserted into the machine. The unit is tilted towards itself and turned on. The machine is gradually lowered to a horizontal position.
Grinding, scraping the floor is carried out with an abrasive material of 40 or 60 grain size.This treatment allows you to remove old paintwork, remove scratches, bumps and stubborn dirt. Coarse sanding, depending on the surface quality and the desired result, is carried out 2-4 times.
Helpful advice! To improve the sanding process, the boards can be slightly moistened beforehand.
For deck decking, rough wood flooring is done along the grain from the wall. With this method of laying, lateral movements are performed only when the unit turns around the vertical enclosing structures of the room. If the parquet board is laid in a herringbone pattern, sanding is carried out diagonally with an even movement over the entire surface area. All processing options are shown in the photo of sanding wooden floors.
If for laying the covering the method of "shield", "braiding" or multidirectional installation in the form of a palace parquet was used, the work is performed crosswise without highlighting separate zones. On artistic parquet, grinding is carried out in a circular motion with a spiral twisting. Processing should be done at a medium constant speed. Do not press the unit too hard to the surface. This can cause dents and burns.
Important! Sanding the surface is dusty, so make sure the room is free of drafts.
During work, the condition of the abrasive nozzle should be periodically checked. A worn-out element must be replaced with a new one in time in order to exclude the formation of untreated stripes and areas. After sanding the main surface area, the corners and other hard-to-reach areas are processed. For this, it is better to use orbital machines or units of the "boot" type with circular nozzles with a grain size of 40 or 60 units.
Finishing sanding and painting of wood floor
At the next stage, fine grinding of the wooden floor is performed, the price of which is 120 rubles /m²... For this, one- or three-disk surface grinders are used. Such units allow you to finally eliminate all small cracks, gaps, irregularities and other defects in the base. For this event, nozzles with an abrasiveness of 60, 80, 100 and 120 units are used. There are situations for which the use of wheels with a grain size of 180 or 240 units is justified.
Important! Fine sanding begins with a new wood surface used as flooring.
How to sand a board at home? Processing is carried out along the fibers. The machine should not move along one board, but overlapping the joint, capturing adjacent elements. The surface is sanded twice. As they wear out, the circles change to new elements. Steps, corners and other hard-to-reach places are processed with a "boot" or angle grinder. After finishing work, the surface should be thoroughly cleaned of small debris with a vacuum cleaner or damp cloth.
The next step is to putty the gaps and small defects. For this type of processing, ready-made pasty compositions for wood or special putties of a liquid consistency are used. The second option is considered more preferable, since when mixing the material with sawdust, you can get a mass of the same shade as the floor base, which can fill all the gaps and voids. Moreover, this composition is characterized by good elasticity and does not crack over time.
The material should be applied using a stainless steel spatula, which fills the pores while cutting off small wood fibers that are sticking out at the same time.
The base is polished before the surface is finished. Work begins after the putty has completely dried. Finishing grinding is carried out using an angle grinder or a surface grinder with abrasive wheels with a grain size of 120-160 units. The movement of the unit is also carried out along the fibers. Then the surface is thoroughly cleaned.
The final step is priming the surface with a topcoat. First, the floor is treated with a primer or compound with a bioprotective, tinting and fungicidal effect. If a colored putty was used to seal defects, the floor covering will be multi-colored. After the surface is completely dry, the first coat of oil, varnish or wax is applied. Further, the finest intermediate grinding of the surface takes place with a grinding machine with a nozzle with a grain size of more than 140 units. The coating is cleaned and a final layer of material is applied to it.
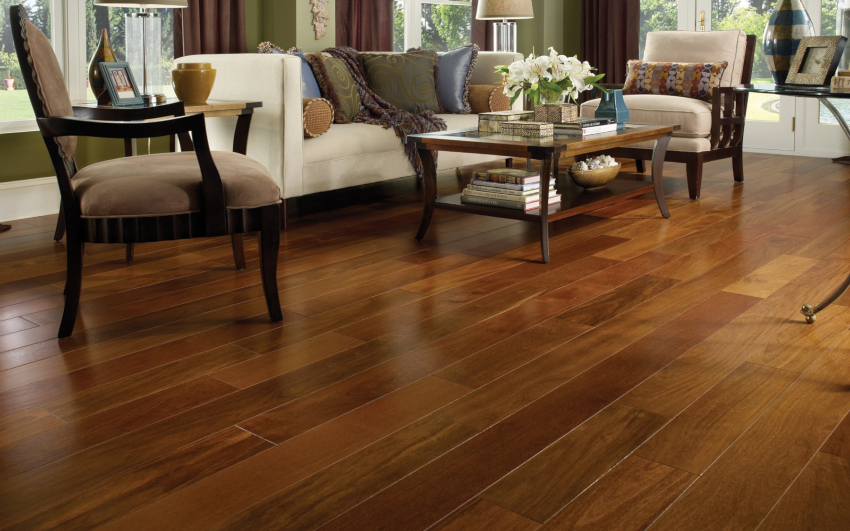
The first coat of oil, varnish or wax is applied after the surface is completely dry from the primer
How to grind a board at home with a grinder
How much does wood floor sanding cost? This event can be very costly. There is an alternative budgetary method of surface treatment, which is carried out using a conventional grinder equipped with a petal nozzle, where an abrasive wheel of the required grain size is located. Such a simple device, which is available in the arsenal of any home craftsman, will process the surface to an almost perfect condition.
The tool allows you to remove from the surface all protrusions, knots, irregularities, protruding nails or screws. Grinding boards with a grinder is performed with variable use of sandpaper of varying degrees of grain.
Useful advice! To get the best possible result, a high-quality consumable should be used for grinding the surface with a grinder.
In the process of sanding a wooden floor with a grinder, a large amount of shavings is formed, which scatters in different directions. Therefore, work must be carried out in goggles and a respirator.
The process of sanding a wooden coating with a grinder begins with the preparation of the base, from which the old coating should be removed. For this, a roughing nozzle for a tool is used in the form of a bowl, in which twisted wires are located around the perimeter. Such a nozzle is presented in several versions, and it is selected depending on the type of surface to be treated. For a wooden base, do not use a roughing bowl with thick strands around the perimeter, designed for processing a metal or concrete surface.
At the next stage, coarse grinding is performed using special grinding and polishing wheels with varying degrees of graininess, which are attached to the Velcro attachment on the back of the product. Fine finishing sanding is carried out to obtain an aesthetic appearance of the coating using a circle from zero. Finally, you can polish the surface. For this, felt cloth circles are used.
Important! Grinding the surface occurs at high speeds of the grinder's engine, and polishing - at low.
Despite the fact that sanding a wooden coating is a difficult, laborious, time-consuming and costly process, this technology provides a perfectly flat, smooth surface with high decorative qualities. You can entrust the processing of the base to a professional or sand the wood floor with your own hands with a machine or grinder.