From this article you can find out the features of a tool such as a disk cutting machine for metal: types of structures, advantages and disadvantages, technical characteristics. Here you can get acquainted with the products of the most popular and demanded manufacturers. The article discusses in detail the technical and operational features of machines designed for metal cutting, and also provides a comparative description of market prices.
Content [Hide]
- 0.1 Disc cut-off machine for metal: scope
- 0.2 The device of a disk cutting machine for metal
- 0.3 Classification of cutting machines for cutting metal
- 1 How to buy a disc cutting machine for metal profitably: an overview of tools and manufacturers
- 1.1 How to choose and buy a disk cutting machine for metal
- 1.2 Features of the choice of pendulum saws for metal
- 1.3 How to buy a metal cut-off saw: a review of the best models
- 1.4 Review of pendulum saws for metal: prices and specifications
- 1.5 Features of wire straightening and cutting machines
- 1.6 Technical features of straightening and cutting machines PromTechOsnastka
- 1.7 Overview of cutting-off machines for metal: prices and technical characteristics
- 1.8 Features of abrasive cutting machines for metal
- 1.9 Which is better to buy a metal cutting machine with an abrasive cutting element
- 1.10 Overview of abrasive disc machines for metal: prices and technical characteristics
- 2 Rules for the operation of cutting machines for working with metal
Disc cut-off machine for metal: scope
Cutting machinedesigned for metal working is a high performance electric tool. This type of equipment is used for cross-cutting of rolled metal blanks, as well as products made on the basis of metals and various alloys.
Disc machines are used to form workpieces from materials such as:
- corner;
- metal strip;
- rod;
- I-beam;
- shaped pipe having a round or square section;
- channel;
- other elements of rolled metal.
Note! Disk equipment is considered the most demanded. Bandsaws and hacksaws are also used for metal cutting, but they are less popular.
Disc equipment is used at metalworking facilities, as well as in factories that manufacture metal structures. A circular saw is used as a cutting element.
Machine-tool designs have many advantages:
- simple structure;
- high-quality metal cutting;
- ergonomic control;
- ease of use.
The equipment can be operated by an operator without special qualifications.
Band-cutting machines for metal use a long toothed saw as a cutting element, which looks like a closed belt. The material for the manufacture of this part is high-speed steel. Thanks to the minimum kerf, material wastage is reduced and an accurate cut is obtained. This type of equipment is most often used in large and mass production.
A hacksaw blade is used to cut metal blanks in hacksaw units. It is attached to the saw frame. Such machines can be manual or electromechanical. Hacksaw machines are used in small enterprises and in procurement shops.
The device of a disk cutting machine for metal
The equipment is assembled on the platform. This design can be metal or rigid. Moreover, the placement of the components of the machine is not stationary, but removable. A vise with a reliable stop is installed on the tool, thanks to which workpieces with different types of configuration are firmly held during the cutting process.
For cutting metal, a disc made of high speed or carbide steel is used. Instead, a wheel made of a material with an abrasive hard surface can be used.
The rotary movement is transmitted to the cutting element from the electric motor due to a gear or belt drive. The first option is installed on stationary equipment with a high power reserve, the second is suitable for compact tools with a portable design.

In disc cut-off devices, wheels made of carbide steel or abrasive material are used as cutting tools
Note! There are machine modifications where the disc is connected to an electric motor without a drive (directly). Such a structure has household appliances with low power.
Classification of cutting machines for cutting metal
Disc equipment for metal cutting is divided into 4 classes. A tool belonging to the first category is considered universal. With the help of such machines, you can process any metal products, and in large quantities. The fourth class of equipment includes tools for household use.
Tool classification based on the number of cutting edges:
- Single-head - there is one disc in the design, so the equipment has a low efficiency. The tool can only be used for performing one operation, for example, cutting a blank for a frame profile.
- Two-head - the tool is equipped with 2 cutting elements, which allows performing several operations with metal simultaneously. One of the heads is rigidly fixed, and the other moves. It only takes one operation to cut the frame profile, so the double-head machines can be used in automatic mode. Thanks to this, the efficiency of the tool is doubled.
Equipment classification by the method of feeding the cutting element:
- pendulum cutting machines for metal;
- tool with front disc feed;
- machine with bottom feed of the cutting element.
Varieties of machines:
- correct and detachable;
- abrasive cut-off;
- cutting saws.
Useful advice! Equipment should be selected taking into account the tasks for which it will be used. Only in this way can the tool's capabilities justify the costs of purchasing it.
How to buy a disc cutting machine for metal profitably: an overview of tools and manufacturers
Before proceeding with the choice of the manufacturer and model of the device, it is worth deciding on the required characteristics. To correctly select the size of the cutting disc, it is necessary to take into account two important factors: the dimensional parameters of the workpieces that will be processed on the machine, and the material from which they are made.The modification of the instrument itself depends on these nuances.
Next, you need to select the type of structure placement. It can be desktop or outdoor. The second version of the equipment is used to work with massive, dimensional products. To cope with heavy loads, such a tool is equipped with an electric motor with an increased margin of power, so that the operator can cut metal workpieces with a large wall thickness.
Constructions of desktop modifications are mobile, so they can be used even on construction sites. With their help, you can repair various metal structures, etc.
How to choose and buy a disk cutting machine for metal
When choosing a machine for cutting metal, technical characteristics are of paramount importance, since they have a direct impact on the quality of cutting, equipment productivity, its service life, etc.
List of technical characteristics that you should pay attention to when choosing a cut-off tool:
- power level of the power plant (nominal value);
- method of transmission of torque (gear or belt transmission);
- the number of revolutions per 1 minute, as well as the ability to customize their number;
- dimensional parameters of the cutting element (size of the landing and outer diameters of the disc);
- the upper limit of the dimensional parameters of blanks with a different type of configuration (the permissible size of the section of a circle, pipe, plate, angle, etc.);
- total weight of the structure, its dimensions;
- the ability to rotate the cutting unit to a certain position in relation to the workpiece.
Useful advice! The most important technical parameter for a large tool with high efficiency is the CNC unit, its type. These indicators have an impact on the operation of the machine: cut accuracy, automation and programming features. Do not lose sight of this criterion for choosing a tool.
At the final stage of the selection, you should pay attention to the technical parameters of the built-in vice. The dimensions and indicators of this element determine the dimensions of a metal part that can be machined on a machine.
Features of the choice of pendulum saws for metal
Circular saws are used to cut various types of profile parts, the material for which is steel, non-ferrous metals or cast iron.
The machines cope with cutting of the following types of rolled products:
- square;
- channel-type;
- round;
- I-beam;
- rectangular.
The equipment is suitable for small-scale or one-off production of parts.
Scope of application:
- furniture manufacture;
- Finishing work;
- carpentry work;
- installation work.
Based on what type of workpiece is used, a specific type of disc is selected and its speed is adjusted. The cut can be made at any angle.
Due to the fact that the rotation of the disc circumference is carried out at high speed, and also the power capabilities of the drive of the machine itself are added to this indicator, the cutting element wears out very slowly. At the same time, the efficiency of cutting metal is maintained.

Circular saws are used for cutting various types of profile parts made of steel, non-ferrous metals or cast iron
How to buy a metal cut-off saw: a review of the best models
One of the most popular models is the Makita 2414NB, which has a portable design.
This modification is used for cutting workpieces from the following materials:
- metal;
- a rock;
- ceramics;
- PVC.
The manufacturer Makita produces quality and reliable products, but despite this, this model is designed for medium loads.
Note! Makita model 2414NB has a high level of operational safety.The manufacturer has provided for the presence of a limiter in the design, which acts as a spark shield. In other words, the possibility of tool contact with the working surface is eliminated. The blade has a protective guard made of durable material.
The shaft locking function allows quick tool changes. The design is characterized by small dimensions and light weight (16 kg). The machine is double insulated.
The Hitachi CC14SF pendulum saw for metal can be classified as a professional tool. The 2000 W motor provides high cutting quality and a fairly large depth - 11.5 cm. Due to improved technical performance, this type of equipment has an extensive scope of use.
Disc change is easy and completely safe due to the fact that the spindle is equipped with a special locking device. The presence of clamps makes it easier to work with the workpiece. The machine has double insulation, and its body is made of aluminum. The handle is rubber coated for a secure grip. The cutting width is 13 cm. The total weight of the structure is 18 kg. The engine produces 3800 rpm.
Review of pendulum saws for metal: prices and specifications
Overview table of popular models:
Tool model | Motor power, W | Cutting width, cm | Rotation frequency, rpm | Cutting depth, cm | Disc diameter, cm | Structure weight, kg | price, rub. |
Makita 2414NB | 2000 | 23,3 | 3800 | 13,7 | 35,5 | 16 | 11030 |
Hitachi CC14SF | 2000 | 13 | 3800 | 13 | 35,5 | 18 | 11350 |
Matabo CS 23-355 | 2300 | 17,5 | 4000 | 17,5 | 35,5 | 17 | 12700 |
Makita LC1230 | 1750 | 11,5 | 1300 | 11,5 | 30,5 | 19 | 24800 |
Makita 4131 | 1100 | 6 | 3500 | 6 | 18,5 | 5 | 21700 |
ENKOR Corvette-433 | 2200 | 10 | 2670 | 10 | 40 | 75 | 32300 |
DeWALT DW872 | 2200 | 10 | 1300 | 10 | 35,5 | 23 | 56700 |
ENKOR Corvette-431 | 2400 | 11 | 3800 | 11 | 35,5 | 17 | 80000 |
BOSCH GCO 2000 | 2000 | 11 | 3500 | 11 | 35,5 | 18 | 13800 |
ENKOR Corvette-432 | 2200 | 13,5 | 2670 | 13,5 | 40 | 73 | 31500 |
Bison ZPO 355-2200 | 2200 | 13,5 | 2800 | 13,5 | 35,5 | 22 | 14400 |
Evolution rage 4 | 1200 | 4,5 | 1400 | 4,5 | 18,5 | 9 | 28000 |
JMS 10S | 1600 | 7,5 | 2950 | 7,5 | 25,5 | 22 | 39900 |
MAC NEW 250 DV | 1300 | 10 | 2800 | 10 | 25 | 84 | 123250 |
MAC NEW 315 EDV | 2200 | 11 | 3000 | 11 | 31,5 | 193 | 123250 |
MAC NEW 350 S | 2200 | 12 | 3000 | 12 | 35 | 280 | 468000 |
Features of wire straightening and cutting machines
Correct cutting equipment is used for cutting metal products in coils or spools:
- metal strip;
- reinforcing steel;
- trumpet;
- wire;
- a bar with a profile or round section.
Note! Unwinding of rolled metal from coils or coils is carried out automatically.

Automated hydraulic straightening and cutting machine METAL KING GJH-14 in the production of metal structures
A wire or other type of product is pulled through a straightening mechanism, where the material is straightened along all planes. The straightened metal is fed onto a table equipped with a measuring device. There, the wire is automatically cut and placed in the receiving tray.
The structure of the straightening and cutting unit consists of:
- unwinder (driven type, stationary or non-driven);
- dressing unit (rotary or roller);
- cutting unit (guillotine type or flying).
Thanks to such a large selection of components in the design, this type of equipment can have individual parameters, which allows you to choose a tool taking into account different needs. In the process of processing the wire, a high quality cut is ensured with minimal surface roughness.
The scope of the machine tools extends to:
- construction;
- mechanical engineering;
- instrumentation;
- mass and large-scale production;
- other types of industries in the industrial sector.
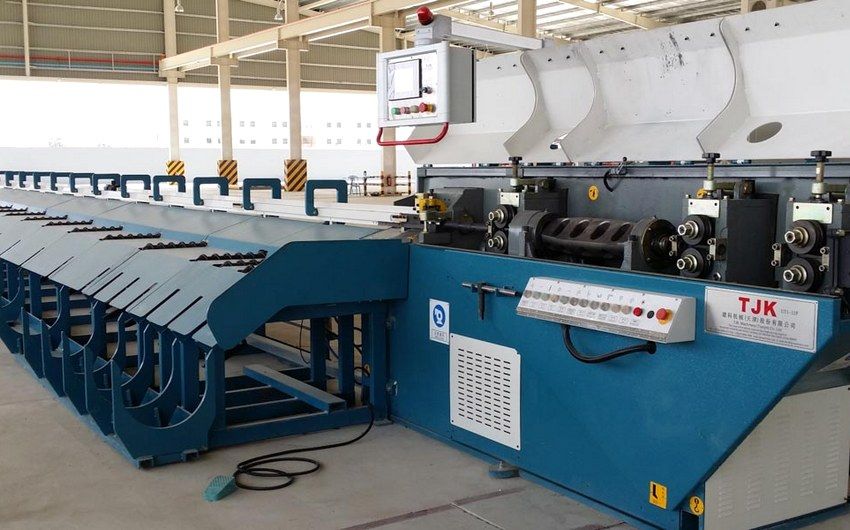
Straightening and cutting machine GT 5-12Q, used for processing reinforcement with a diameter of 5-12 mm
Technical features of straightening and cutting machines PromTechOsnastka
Each straightening and cutting machine manufactured by PromTechOsnastka has a receiving table of 8 m in size. If the client wishes, this indicator can be increased. Uncoilers are not included in the package of devices, which must be ordered additionally.
The most popular model of the manufacturer is the GT 4/14. It is used to work with steel reinforcement, the diameter of which is 0.4-1.4 cm. The range of lengths for cutting bars is within 0.3-8 m.The cut elements enter the receiving tray through the hole located on the knife. Upon reaching the limit switch, which is placed to the required length, the bar activates it and the knife is started to cut the material.
Note! The equipment control panel makes it possible to immediately set the required number of blanks.
Advantages of the GT 4/14:
- high power level;
- minimum errors in length when cutting material;
- simple system of use and maintenance;
- the ability to cut for a long time without interruption;
- high processing speed;
- low level of noise impact;
- operational safety;
- automatic shutdown in the event of a power outage.
Straightening of the material is carried out by rolling rollers acting on the workpiece from all sides.
The package includes:
- receiving line and switch;
- section where cutting is carried out;
- section for straightening;
- receiving tray.
The machines can be installed in a preparatory workshop, at a construction site. The equipment will be useful to entrepreneurs selling metal meshes and bars.
Overview of cutting-off machines for metal: prices and technical characteristics
Overview table of popular models:
Tool model | Motor power, W | Workpiece diameter, mm |
Processing speed, m / min. | Cut length, m |
Weight, kg |
price, rub. |
PromTech-Osnastka GT 4/14 | 2200 | 4-14 | 18-45 | 0,3-8 | 500 | 280000 |
PromTech- Equipment GT-2-8 | 1350 | 2-8 | 30-100 | 0,005-80 | 1200 | 600000 |
A-21 PRA-499 | 3600 | 5-16 | 30-45 | 0,1-9 | 5400 | 1690000 |
A-21 PRA-498 | 1650 | 4-12 | 31,5-45 | 0,5-6 | 1900 | 770498 |
A-21 SPR-12 | 1650 | 4-12 | 31,5-45 | 0,5-6 | 1900 | 630000 |
Teams 2/6 | 1150 | 1,8-6 | 140 | 0,1-12 | 1040 | 979000 |
Teams 3/10 | 1250 | 3-10 | 60 | 0,1-12 | 1430 | 949000 |
Teams 5/12 | 1250 | 5-12 | 60 | 0,1-12 | 1430 | 1341000 |
Teams 6/16 | 4500 | 6-16 | 50-100 | 0,1-12 | 3000 | 1878000 |
VPK PRO-12 | 750 | 4-12 | 35 | 0,5-12 | 255 | 275000 |
VPK PRO-14 | 400 | 4-14 | 50-60 | 0,9-8,6 | 1250 | 690000 |
VPK PRO-14 Compact | 1100 | 5-14 | 50 | 0,5-30 | 520 | 428500 |
Note! The table shows the average prices for equipment. The exact price depends on the exchange rate and the store selling products.
Features of abrasive cutting machines for metal
Circles are used as cutting elements in abrasive cutting machines. They are made from abrasive materials.
Equipment of this type is used for:
- cutting lengthy materials into blanks;
- cutting off excess material on rolled metal products;
- cutting profile elements at the required angle.
Such a tool is in demand in production facilities (assembly and procurement shops) and in repair shops. The equipment copes with the processing of non-ferrous metal blanks with any profile configuration. The working angle is in the range of 0–45 °.
Some models make it possible to install a dust extraction system. A pumping unit is included in the standard equipment of some modifications. It cools the cut of the workpiece with water. There are options equipped with a special mechanism that eliminates burrs during parts processing.
Which is better to buy a metal cutting machine with an abrasive cutting element
Among the abrasive cutting tools, the pendulum machine SOM-400 is especially popular. This type of equipment is used for cutting metal profile elements at an angle of 0–45 °. The torque is transmitted using a belt drive.
Useful advice! The installation of the unit must be rigid. It is imperative to use a previously prepared foundation for this. The machine is attached to it with the help of anchor bolts. For these purposes, special holes are provided in the tool frame.

In order for the operation of the equipment to be effective, and the costs of purchasing it to be justified, the type of cutting machine must be selected taking into account the tasks that will be performed with the help of it.
The SOM-400 modification is considered the base model. An electric motor is installed in this device, the power of which is 2200 W. The total weight of the structure is 52 kg. The diameter limit of the material that can be cut on the machine is 4 cm.
The COM series of machines includes other equipment modifications:
- 400 B;
- 400 V;
- 400 g;
- 400 E;
- 400 I.
Each of these tools has its own capabilities and technical characteristics. Such as: size, weight, power level of the motor, design features, number of belts in the drive.
Overview of abrasive disc machines for metal: prices and technical characteristics
Overview table of popular models:
Tool model | Motor power, W | Workpiece diameter, mm |
Rotational speed, rpm | Abrasive wheel size, cm | Weight, kg |
price, rub. |
SOM-400 B | 4000 | 60-120 | 3500 | 40 | 113 | 40100 |
SOM-400 G | 2200 | 40-100 | 2860 | 30-40 | 65 | 25900 |
SOM-400 V | 2200 | 40-100 | 3500 | 30 | 65 | 25900 |
SOM-400 E | 5500 | 60-140 | 2860 | 40 | 120 | 43300 |
ENKOR Corvette-430 | 2000 | 100 | 2800 | 35,5 | 20 | 11480 |
Stalex SQ-40-1 | 2200 | 40 | 2242 | 25,4 | 90 | 35750 |
Rules for the operation of cutting machines for working with metal
After the model of the machine is selected and purchased, it is necessary to carry out the installation of equipment.
Requirements for room conditions:
- sufficient level of lighting;
- the presence of an exhaust type ventilation system;
- the absence of flammable and flammable materials in the vicinity of the device.
The basis for mounting the device must be reliable and solid. Under the influence of the weight of the equipment and its vibrations during operation, the foundation should not undergo deformation changes.
Operating rules:
- workpieces must be securely fixed on the working surface;
- the saw blade is installed only when the equipment is turned off, a similar requirement applies to changing speeds;
- in mobile versions, for safe work outside the premises, protection against moisture ingress (insulation) must be provided;
- Do not use discs with parameters unsuitable for workpieces.
When installing the tool, it is imperative to adhere to all the manufacturer's requirements regarding the RCD, the ground loop, as well as the maximum loads on the electrical network.